The largest robot in the history of Spanish carmaker SEAT joins the more than 2,200 others that work together to build the company’s latest models…
More than 2.5m tall and weighing three tonnes. This is how the new giant at Spanish carmaker SEAT’s Martorell plant measures up. The largest robot in the history of the factory joins the more than 2,200 others that collaborate in the assembly of the company’s latest models.
Below are the figures behind this technological giant in the automotive industry…
3,000kg of precision. Many of the parts that make up the car ‘puzzle’ weigh hundreds of kilos on their own. When it comes time to assemble them, the weight multiplies. “In order to transport and assemble the car’s bulkiest parts and to ensure that its structure doesn’t suffer in the slightest, we had to use a larger robot” says Miguel Pozanco, head of robotics at SEAT. Standing almost 3m tall, this robot is capable of assembling three of the heaviest parts of the vehicles, those that make up the side of the car, weighing almost 400kg.
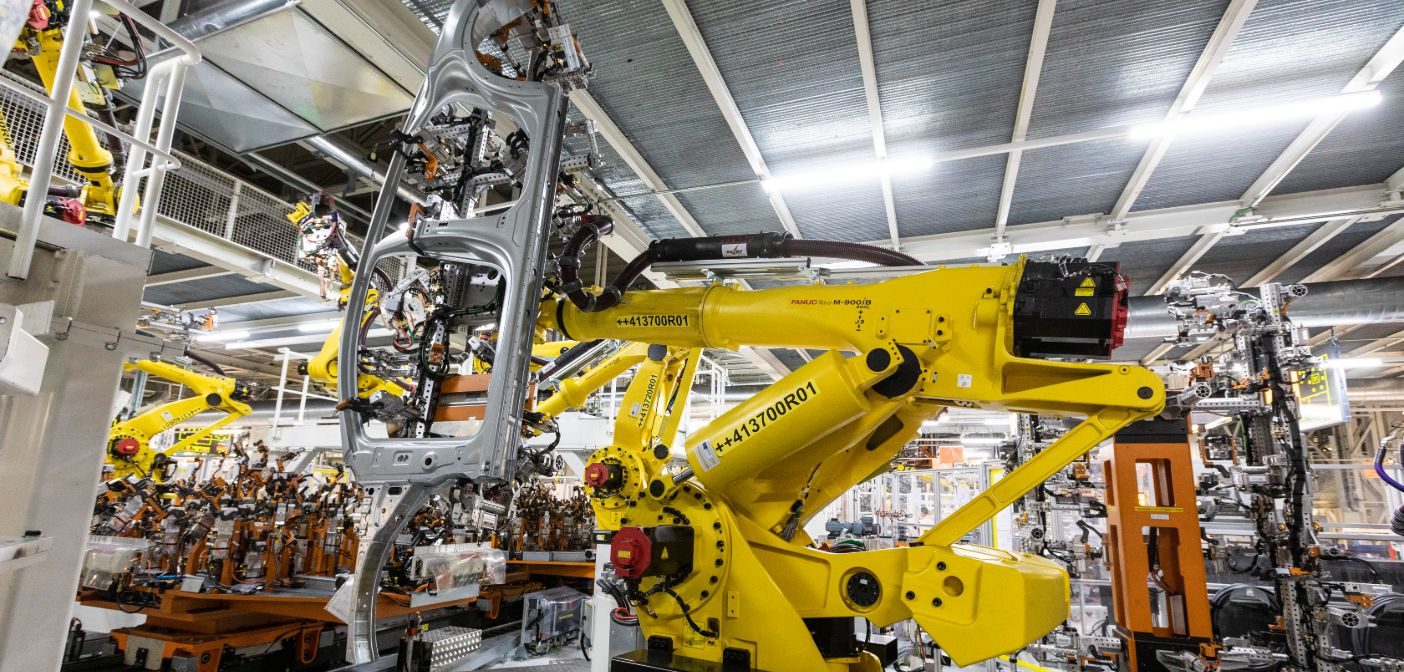
Two among 2,200. Martorell already has two of these giant robots. They work side by side in the body shop together with another 2,200 robots in the facilities as a whole, coordinating with 1,700 workers to manufacture one complete car body every 68 seconds. Their incorporation simplifies part of the vehicle assembly process and reduces the footprint of the manufacturing line. “These robots assemble key sections of the vehicle, such as the sides. As they can lift more weight, they carry out two operations at the same time, increasing the quality of the parts,” according to Pozanco.
2.5m with a 400kg payload. SEAT has other robots capable of carrying up to 700kg, but in this case, they needed to go a step further, exactly four more metres. “There’s a relationship between the weight the robot can carry and its reach. In other words, holding a bucket of water with your arm next to your body isn’t the same as holding it with your arm outstretched. This giant can carry 400kg at almost 4m from its central axis,” explains Pozanco. This is a great novelty, as the same robot can join the three side parts and transfer them to the welding area without any other robot having to handle them again. This has been achieved thanks to the incorporation of a linear axis that enables it to move up to 4m.
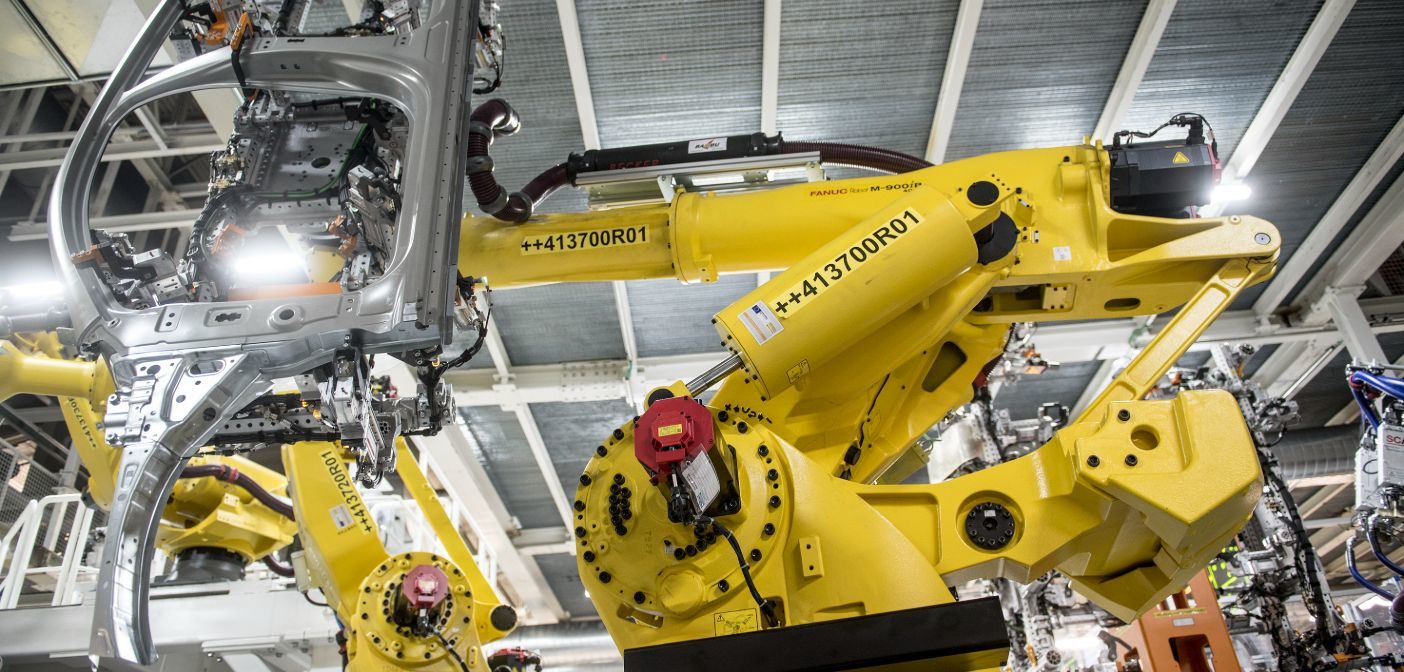
Industry 4.0. The robots are equipped with software that enables remote monitoring of all their operating data, such as motor consumption, temperature, torque and acceleration. “By analysing this data, we can anticipate any unforeseen events. In other words, predictive maintenance is carried out, which ensures quality and precision on an ongoing basis” concludes Pozanco.