The Eigenstetter Joinery in Rehna, Germany has installed industrial robots from manufacturer Kuka to enable it to take on large, complex projects.
The carpenter, which specialises in interior fittings and the manufacturing of windows and doors, worked with Kuka to create a robot milling centre of impressive dimensions that is unique in the woodworking trade.
The robot can choose between a total of twelve different attachments to mill or grind various free-form shapes. Additionally, the parts to be worked on are placed in the machines by the robot, which can carry up to 500kg.
Master carpenters Alex Eigenstetter and son Martin Decker could not imagine a robot in joinery. Decker said: “But I have to admit that it has opened some doors.”
The carpenter and project manager was faced with a project for an architect in England that pushed the old CNC milling machine to its limits. “It involved a large bench into which a seat was to be milled. But the machining height of the five-axis CNC milling machine was too small,” explained Decker.
They found a supplier in Tyrol that had a Kuka robot and are now able to tackle even larger projects. “We were able to mill parts for huge tree houses, as well as elliptical staircase stringers or unusual free-forms,” Decker added.
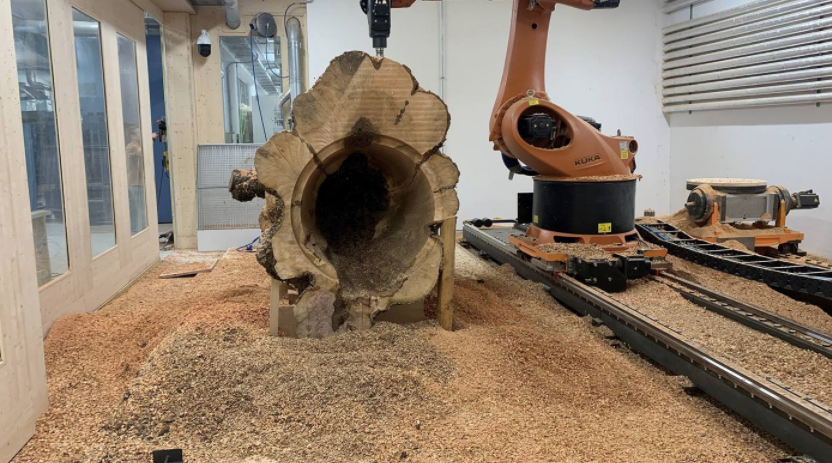
Eigenstetter is already working on the next project with the local Fraunhofer Institute. “We want to use smaller robots in medium series on carpentry machines such as a milling machine or a belt sander according to the part-to-tool principle,” he explained.
Furthermore, the company are working with other joineries from the surrounding area to supply special parts, as well as working with trainees who can learn CNC skills in a four-year carpentry technician training program.
“You really have to dare to take this step – and also become a little inventive yourself. But it’s worth it,” Decker concluded.