A collaborative project between Cranfield University and Network Rail is looking to develop an autonomous integrated inspection and repair system for railways.
The In2Smart 2 project features a Warthog unmanned ground vehicle (UGV) from manufacturer Clearpath Robotics combined with a collaborative arm from Universal Robots. The project aims to demonstrate the command and control of autonomous inspection and repair.
Starting from a job control system, an instruction could be fulfilled using a physical system which seeks a fault, and then carries out any necessary repair actions. Furthermore, the team are working to demonstrate range, navigation, and communication challenges at scale.
Using an autonomous system for railways comes with a range of challenges, according to the project. This includes the tough environment of the railway infrastructure for UGVs, there are some places with no communication, no GPS such as in tunnels and Faraday cages, few opportunities for charging, and uneven surfaces with obstacles.
The scale of the challenge also requires millimetre accuracy within a 1,000km network. In2Smart 2 intends to bridge those gaps.
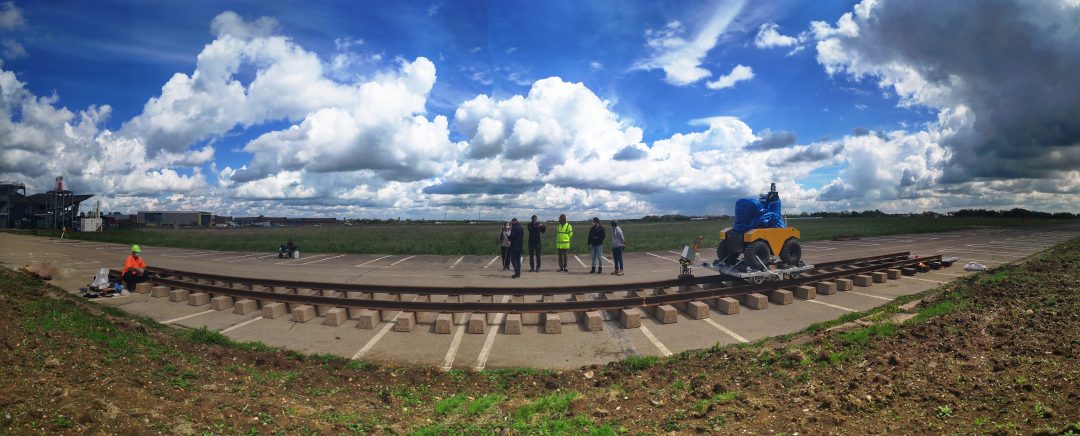
To get the project up and running quickly, particularly for accelerated hardware integration, the In2Smart 2 team opted to utilise the Warthog UGV robotic platform. The Warthog UGV allowed the team to test sensor systems, navigation concepts, and obstacle detection and avoidance within ready-to-run hardware and software.
The robust running gear was particularly suitable for running across railway infrastructure, and additionally, the team built a trolley to mount Warthog UGV on the railway to increase its range while carrying more instruments.
One of the core challenges was the integration of the sub-systems with the team finding there are often unexpected outcomes in hardware, electronics, and software. This resulted in the need for a diverse team with range of skill sets, as well as the right equipment.
Warthog UGV’s main role for this autonomous rail inspection and repair system is to carry the sensors and tools needed for fixing the railway track, this included odometer systems, lidar sensors and network cameras.
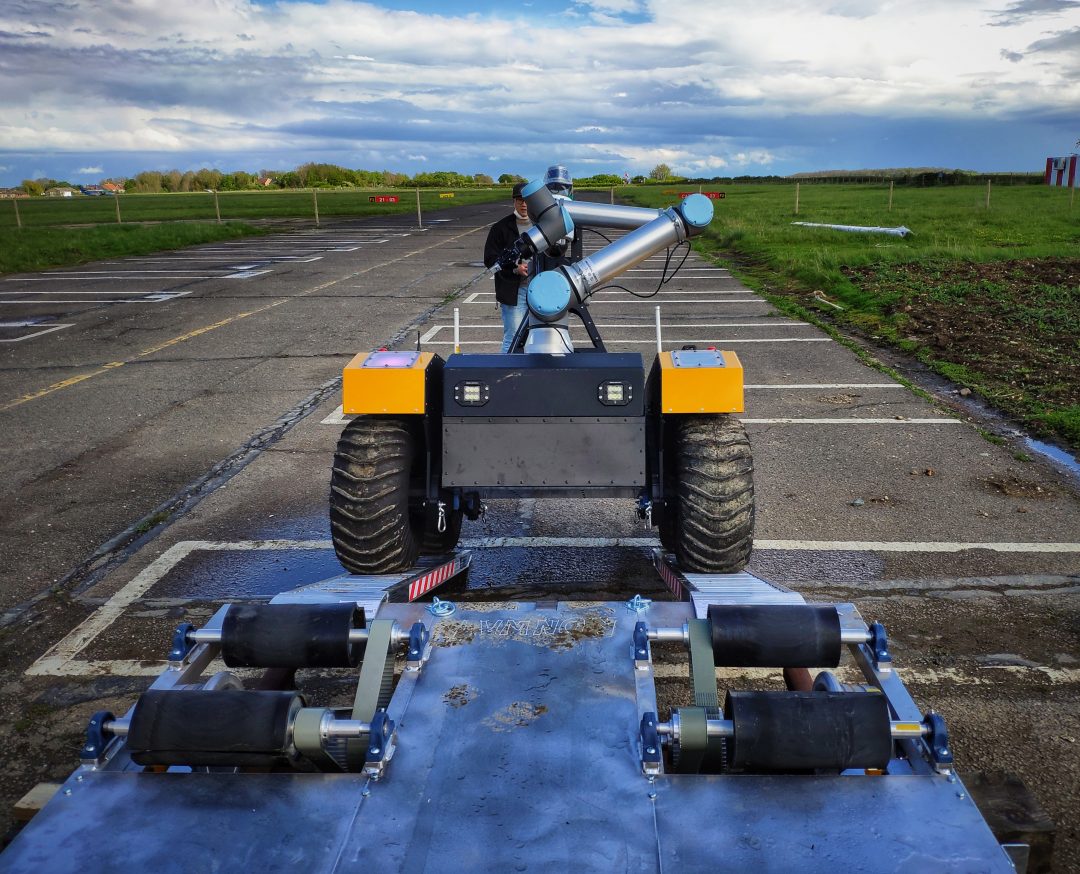
According to the team, Warthog UGV offered them a mobile platform that could easily be fitted with the sensing systems and accessories that they required. They found the robot to be robust, ready-to-run and were able to leverage its sensor suite.
“The Warthog worked perfectly and the GPS was good for 0.2m including RTK.” said Andrew Starr, head of centre for life-cycle engineering & management.
The team’s next steps will be to develop measurement sequences on a railway test track with improved location measurement. Their goal is to understand how autonomous vehicles can be permitted to operate on a working railway.