A canned drinks supplier in the UK is using Kawasaki robots to automatically and precisely place adhesive labels on pallet straps prior to dispatch.
The RS10-N robot was selected by Blackstar Handling, a manufacturer and installer of bespoke conveying and packaging systems, on behalf of the unnamed supplier, who required a solution that eliminates the possibility of contact between the cans and adhesive labels applied to every pallet dispatched.
Almost 9,000 cans are contained on each of the hundreds of pallets delivered by Blackstar’s customer weekly.
The robot thus places the labels onto 12mm-wide retaining straps that secure the load, instead of directly onto the pallets themselves.
Ian Pegler, managing director of Blackstar Handling, said: “This application was especially interesting for us, from an engineering viewpoint.
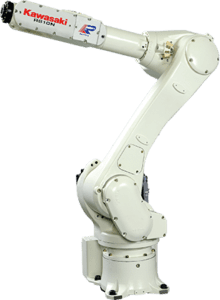
“Applying the label direct onto the strap, rather than onto the pallets themselves, was not in itself a major challenge, other than identifying the correct adhesive.
“But achieving the combination of the required speeds, position, precision and repeatability made us think very carefully about the best ways to automate the process.”
According to Pegler, the RS10-N robot applies two labels per pallet direct onto the retaining straps and typically works through 60 large pallets an hour, which equates to one every minute.
Working on a cycle time of 25 seconds per pallet for labelling, the solution has so far reported zero faults.
An additional advantage of the RS10-N system, said Pegler, is that it doesn’t require a programmable logic controller, which reduces costs and complexity, while also improving efficiency.