US-based ULC Technologies has partnered with British gas distribution company SGN to develop what is said to be the world’s first robotic roadworks and excavation system (RRES).
The collaboration presented the solution virtually on 13 April, providing both a look at the RRES in action, as well as an overview of the three-year design process.
Robert Kodadek, president of ULC, explained that the AI-driven autonomous system has been developed to be an all-in-one solution for excavation.
It can be deployed across the utility industry as well as for rail and transport applications.
The track platform features an ABB robotic arm, which various sensors and tools can be automatically attached to, providing an end-to-end solution.
The system has been designed to enhance safety by fully automating roadwork operations. For example, RRES can reportedly eliminate physical labour injuries such as hand-arm vibration syndrome.
Furthermore, the system prevents “devastating” cable strikes as it not only removes the operator from the situation but also, through the use of AI, is constantly aware of its surroundings including cable locations.
According to developers, this means fail safes can be programmed in, reducing cable damage risks.
What’s more, the system can be programmed to perform repeatable tasks and, using a key-hole strategy, works within the smallest possible core hole, minimising distribution.
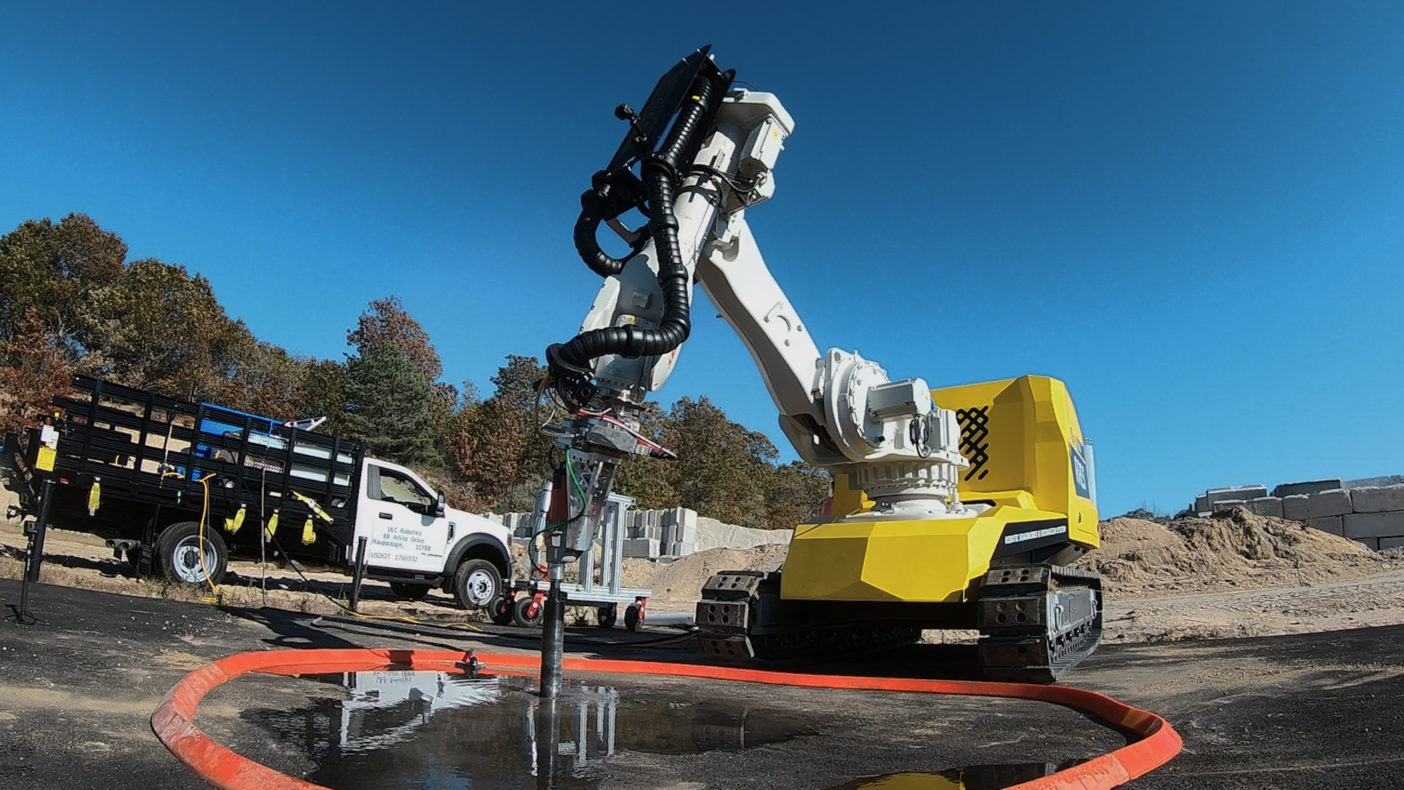
When developing the solution, both companies said they wanted to reduce CO2 emissions by limiting the RRES’s carbon footprint. Thus, the product is fully electric, battery operated and works tetherlessly.
Some 16 independent lithium iron phosphate batteries provide 35kWh of power to provide eight hours of operation time, which could see two keyhole procedures completed back-to-back.
In designing the chassis, the team wanted to make the platform as light as possible while providing enough space for the technology needed for aggressive operation. It also needed be weatherproof.
Additionally, a robotic arm provides six degrees of freedom, extends up to 3m from its centre and can raise 2m above or below the platform.
The concept has been tested and validated in field trials using mock roadways built by the team, providing simulated real-life scenarios to develop the prototype.
The project next aims to complete live trials in southern England, London and Scotland. John Richardson, head of innovation at SGN, said that such field tests and the RRES would lead to an “increase of autonomous operations within intrinsically hazardous environments”.
According to Asmari, the partnership aims to challenge current utility operations by proving the platform can be used in multi-utility and cross-industry applications.
“Through our partnership with SGN, we’ve developed a revolutionary system which will not only provide benefits across the gas sector, but to many other industries around the world,” said Asmari.
“This robot can provide an end-to-end excavation process, with applications that can be adapted to provide a range of solutions for specific problems in the industry.”