Robotic engineering solutions provider Forth has developed a remotely operated rescue robot for disaster recovery in hazardous environments.
The Cumbria-based company has designed the rescue robot for Sellafield nuclear site, it would be autonomously controlled from a command-and-control centre in the event of an incident, enabling the system to be operated at a safe distance.
Mark Telford, managing director of Forth, said: “This is a first for Sellafield to have this type of remotely-operated rescue robot.
“It is important for operators like Sellafield to plan for different scenarios and we are proud to have come up with such an innovative solution.
“We can adapt this technology for any industry or any organisation which would benefit from a rescue robot helping keep humans safe.”
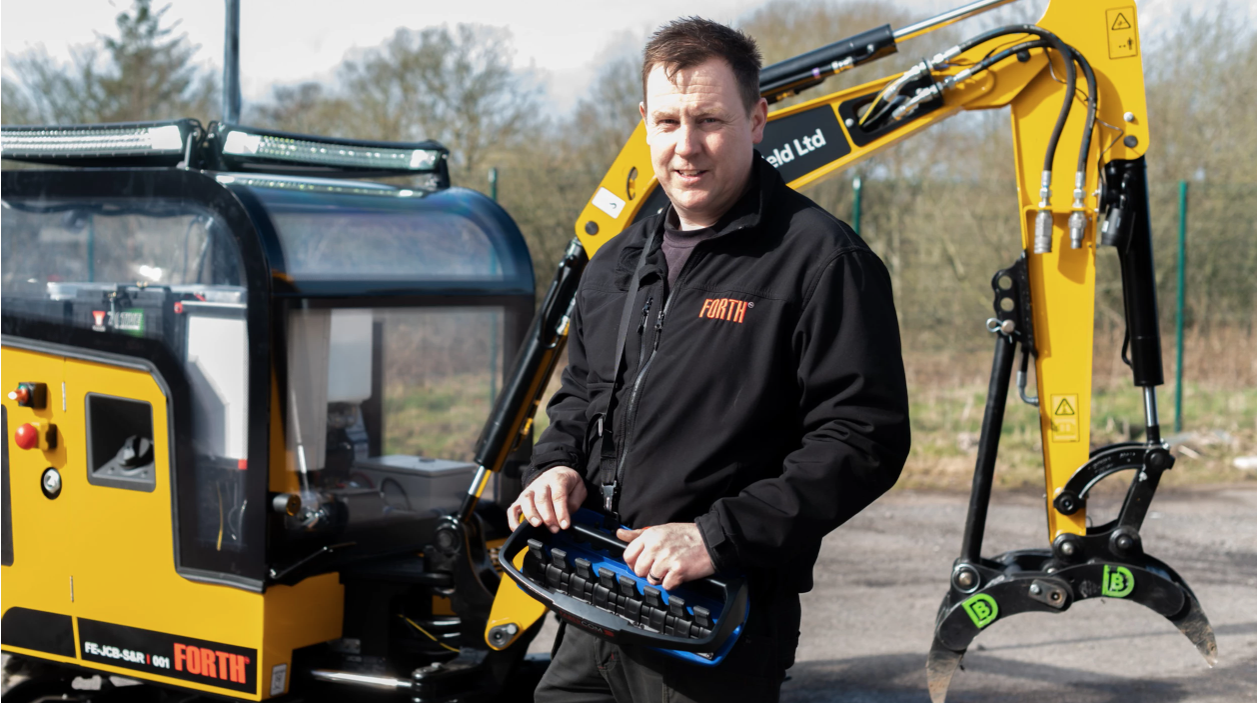
Adapting a 1.6 tonne JCB compact excavator platform, Forth has created a system featuring a range of specialist cameras, lights, and sensors. It has been built to be untethered and able to withstand hazardous environments.
Furthermore, it can also tow a trailer with a fitted hopper that can disperse sand to curb spillages. There is also an affixative spraying system that is used to assist in the containment of a nuclear spillage.
A large grapple hook will enable the rescue robot to move obstructions and a 700bar rescue tool can cut through any hazards in its way, like the system used by the UK Fire and Rescue Service.
Telford added: “We have developed this 1.6-tonne robot because it was what was required for this particular task. But we could develop a product of any size – it could be 10-tonnes, for example, if that was what was needed – and fitted with any type of tools for a range of tasks.
“It’s the ability to remotely operate it which makes it so versatile in a range of hazardous environments.”
Read more: Forth Engineering demonstrates underwater autonomous survey robot