Remote engineering solutions provider Forth Engineering has showcased an intelligent underwater autonomous survey robot for use on nuclear sites, at its Cumbria testing facility.
The Autonomous Aquatic Inspection and Intervention (A2I2) solution completed a live demonstration at Forth’s wet test facility at Maryport, proving it can be used near critical infrastructure.
During a two-hour presentation, the autonomous underwater vehicle (AUV) demonstrated its ability to avoid collisions and locate items on the pond floor.
Furthermore, it showcased the system’s capacity to relay images, which were able to be viewed, analysed and interpreted in real-time on screens nearby on dry land.
Developed by a number of companies from across the UK, including Forth, Rovco, D-RisQ, the National Oceanography Centre (NOC), Thales UK and The University of Manchester, the project received funding from Innovate UK under the Industrial Strategy Research Fund.
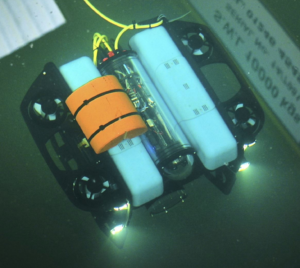
Rovco has supported the project with its artificial perception technologies, including 3D computer vision, simultaneous location and mapping, autonomous path planning, as well as scene understanding using machine learning.
The intelligent data collection system can be integrated onto any subsea vehicle to enhance its capability, according to Rovco.
Gary Cross, senior robotics engineer at Rovco, said: “The whole challenge of this particular project was removing people from hazardous and dangerous environments.
“One of the key things is increasing the distance between the operators and the environment they’re working in. And the easiest way to do that is to make the vehicle remote, remotely controlled and remotely operated.
“Some of the challenges you have, of course, is that as you increase the distance between the operator and the tools which they’re using, you have increased latency and other challenges which generally make it very difficult to operate.
“So, technology such as the advanced perception system and mapping capabilities enables us to use the autonomy to provide the appropriate systems to the pilots who can still be controlled in a safe and meaningful way within the pond.”
The project’s goal is to develop AUVs that improve safety and reduce the challenges of operating in hazardous environments, such as in storage ponds on nuclear sites.
Representatives from Sellafield Ltd attended the demonstration. Steven Martin, business change manager, said: “What we have seen demonstrated is exciting. I’ve been involved in this programme for two years now, and one of the things I wanted to see from this demonstration, which we did see, was that this capability can define a point of interest.
“For instance, in our legacy ponds we have to decommission and remove inventory. So, it’ll be really useful for us to be able to define a data set and then for us to actually survey and prove accountability that we’ve got those items retrieved from the pond.”