Suscom Industries, UK manufacturer of components for office furniture and equipment, has recently expanded its fleet of Kawasaki robots.
The addition of another Kawasaki RS20N robot takes the number of Kawasaki units in use at its plant to a total of eight, with the company explaining it uses the brand exclusively.
There are seven Kawasaki’s RS20Ns with a single, larger, RS50N robot, each working 24 hours a day, five days a week as the Wigan facility. The robots are deployed during the moulding and post-moulding processes of many components and are engaged in a variety of tasks across the shop floor.
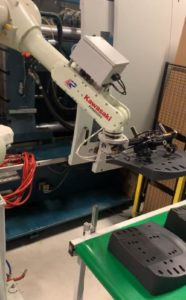
Tasks include the removal of seat bases from a moulding machine before positioning them onto an adjacent workstation, using vacuum grippers.
A further task is removing the five-armed star shaped bases of office chairs from the moulding machine and holding them in place, almost upside down, with a three fingered gripper whilst a laser cutter profiles a section of the base to allow the fitting of the gas strut.
In order to do this, the RS-20N robot must describe a perfect 100mm diameter circular motion as the fixed head of the laser cutter sets about creating the required profile.
Other tasks undertaken by the robots are varied and include upholstering the mesh onto freshly moulded chair backs and installing the five castors into position on the star shaped chair bases.
Suscom technical director Matthew Kennedy, said: “Each of the many tasks we use robots for involves a combination of speed, agility and accurate, repeatable precision. In all the years we have operated our Kawasaki robots, we have never had a single problem, nor a moment of unscheduled stoppage time with them.”