ABB Robotics has announced that a new solution, developed by Cyan Tec Systems, has been built around one of its ABB IRB 6700 industrial robots to produce highly accurate welding on production vessels used in the manufacture of chlorine.
The robot carries a Class 1 laser welder and was built for an end user to solve logistical challenges by bringing the welding of the product in house from a European sub-contractor.
ABB claims that using this solution to contribute to reshoring production would avoid the need to deliver raw materials to the sub-contractor and ship back the finished product.
Laser welding offers the high accuracy required in producing this type of process vessel and provides better quality welds, ensuring that the weld maintains high integrity and prevents any distortion that can result from the higher heat dispersion of other methods. It also offers faster throughput, according to ABB.
The process, however, can lead to eye injuries in human workers, meaning a fully enclosed automated solution was required.
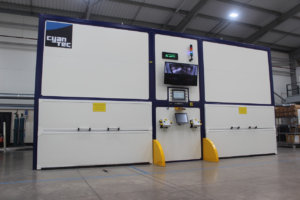
In addition to this, Cyan Tec designed a system that enables users to load one component for welding while unloading a finished component, which it claims will speed up the rate of production.
The system required a machine that could carry out the immediate task required but which also had the flexibility to handle different welding tasks in the future. For this reason, Cyan Tec chose a robot solution rather than a gantry design.
Richard Copson, sales manager at Cyan Tec says: “Over the last six to seven years, we have done a lot of laser applications for welding and cutting. Many of these have used ABB robots and we have built up a bank of experience and expertise, so familiarity with the solution was a big influencer in choosing a robot for the customer.
“The experience we have with ABB robots means we don’t always need their help to design and develop a solution, but they are always on hand if we need to use different features or do things we haven’t done before. As an ABB Value Provider, it’s good to know that their support is always available if we need it.”
As the customer already had an ABB robot on its shopfloor, so Cyan Tec looked at ABB robots that would work for the brief, which also meant the customer’s engineers could conduct basic programming without having to learn a new language.
With a reach of over three meters and running on the track, the ABB IRB 6700 robot can weld accurately along the two-meter length of the component. The robot has a higher payload than that required for the application, but this also gives the flexibility to carry a heavier welding head or other effectors if requirements should change in the future.
The solution also incorporated a vision system on the laser head, allowing it to compensate in the event of misaligned component elements.
What’s more, Cyan Tec also used ABB’s RobotStudio simulation software to support the development of the layout and operation of the solution. By simulating the application using a graphical animation of the robot’s operation and its interaction with the other solution elements, Cyan Tec was able to demonstrate the validity of is solution, including its choice of robot with the right reach.
As well as this, Cyan Tec was also able to show that it would not foul other objects or collide with any of the ancillary machinery.
This helps reduce risks during development by eliminating the need to re-engineer elements found during the commissioning stage.
Overall, the enclosure incorporates two sets of welding fixtures, one for welding together two flat sheets into one.
As well as the robot, track and enclosure, Cyan Tec also integrated the laser source and ancillary components such as the tooling, laser chiller, fume extraction system and assist gas control.