Chemical manufacturer BASF has deployed ANYbotic autonomous four-legged robot at its chemical plant in Ludwigshafen, showcasing the scalability of robotic inspection solutions and its data-collection ability in industrial environments.
The trial reportedly identified the robot’s potential to solve human mobility and data-collection challenges at a large scale, based on ANYmal’s customisable environmental data-collection capabilities.
BASF automation manager Peter Welter said: “We have here a highly heterogeneous environment that has been continuously growing for the past 150 years.
“A walking robot such as ANYmal fulfils one of the main requirements to navigate these complex environments with many steps and steep stairs.”
ANYbotics used BASF’s environment map to simulate an autonomous inspection mission to verify the mobility through critical areas, as well as the visibility of points of interest from the robot’s viewpoint.
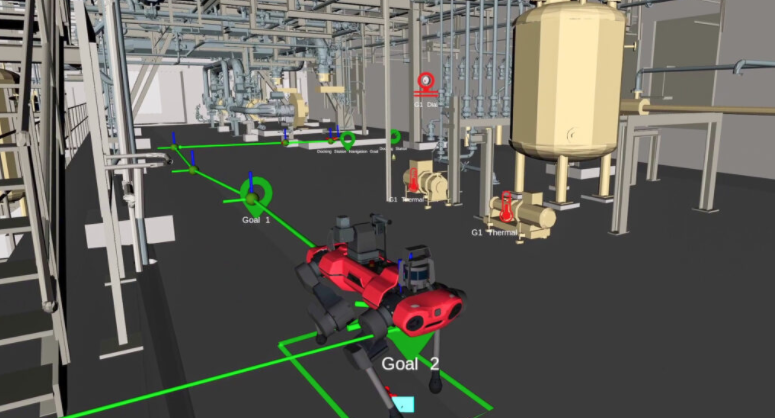
Furthermore, use of ANYbotics’ physics simulator enabled the project to perform preparation works associated with mapping an environment, determining paths, and optimising the position of docking stations.
By validating ANYmal in a simulated environment, the team behind the trial was able to accelerate the on-site commissioning process. ANYmal was able to localise BASF’s real facility using digital-twin data, enabling the system to be deployed efficiently across hundreds of BASF plants.
Once ANYmal was on site at BASF’s facility, the autonomous robot was able to perform typical inspection tasks such as reading gauges, taking acoustic measurements of pumps and compressors, and checking the environment for hotspots using its integrated thermal camera.
Felix Volkman, asset manager at BASF’s Ludwigshafen plant, added: “With automation and robotics, we can increase the quality of the documentation of our assets by having clearly documented and easily accessible test reports via thermal imaging and sound recording, which can be collected daily so we can precisely track the history.”
BASF said it will further evaluate the possibilities of leveraging ANYmal for plant inspections. Welder concluded: “With this proof-of-concept, we show that the idea of a more digitalised plant can be further enhanced by robotics.”