Researchers at the Fraunhofer Institute for Communication, Information Processing, and Ergonomics (FKIE) have developed a new robotic system designed to help emergency services quickly assess dangerous or hard-to-reach environments, such as disaster sites or chemical plant incidents.
The project, known as 3D-InAus, integrates cutting-edge LiDAR (light detection and ranging) technology to create highly accurate 3D models of terrain and structures.
In scenarios like flooding or industrial accidents, emergency responders often cannot safely enter dangerous areas. The 3D-InAus system addresses this issue by deploying a mobile robot equipped with a LiDAR laser that scans and measures distances by emitting pulses of light. The robot generates a 3D point cloud—an array of data points representing the environment—which allows operators to virtually explore the area without physical presence.
READ MORE: Element Logic installs Slovenia’s first AutoStore systemÂ
The LiDAR system works by rotating a laser module mounted on a turntable, emitting 1.3 million pulses per second. The laser pulses bounce off surrounding objects, with the time taken for them to return helping to determine precise distances. The data from these measurements is processed and transformed into a geometrically accurate 3D environment, displaying buildings, rooms, open spaces, and objects with centimeter-level precision.
The robot, which can be operated remotely via joystick and tablet, also integrates a camera system to colourise the 3D model, enhancing the visual detail of the environment. In challenging conditions, such as navigating a building where GPS signals are unavailable, the system uses pre-mapped terrain data to simulate an internal virtual GPS, allowing the robot to move autonomously within structures.
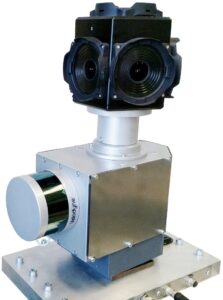
One of the key advantages of the system is its ability to provide a quick yet precise overview of a hazardous area. While detailed mapping takes around three hours for a 400×400 metre area, accelerated operation can produce initial visualisations in as little as one hour. In certain cases, multiple robot systems can be deployed simultaneously to speed up data collection.
The 3D mapping technology also offers significant value for the Bundeswehr (German armed forces), which commissioned the project. The system can integrate additional sensor data, such as measurements of toxic gases or radiation, into the 3D models, providing crucial situational awareness in risky environments.
Timo Röhling, a technical project manager from the Cognitive Mobile Systems department, said: “Compared to robot systems that use cameras to explore a danger zone, our project goes a big step farther. The laser pulses supply measurements for precision 3D cartography of an area of terrain or building. Distances and dimensions are not estimated but instead determined with accuracy down to just a few centimetres.
“You might think of us melding the camera images and point cloud together. This gives us a vivid, detailed and also geometrically accurate 3D environment showing buildings, open space and objects.”
Join more than 11,000 industry leaders at Robotics and Automation Exhibition on 25-26 March 2025. Explore cutting edge technologies, connect with peers and discover the latest innovations shaping the future of manufacturing, engineering, and logistics. Register now to secure your place at this premier event!