Robotics and Automation 2022 exhibitor Lucas Systems is drawing crowds to Stand 106 this morning with its AI-powered solutions designed to improve warehouse processes.
Speaking exclusively to Robotics & Innovation, James Hart, Lucas Systems business development manager, EMEA, explained how, in modern warehouses, workers following a manual picking process will typically spend as much time walking or driving between pick locations than they do pulling products from bins, slots or racking locations.
Thus, Lucas Systems aims to take a different approach to reducing travel by building on lean process engineering and applying AI-based optimisation technologies to increase selection density and reduce travel in selection and other travel-intensive DC activities.
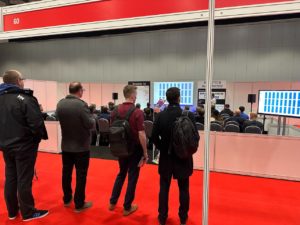
This emphasis on reducing travel times and harmonising the relationship between human and robots will be discussed in greater depth by Hart at 11.15am at the Robotics and Automation Conference theatre. During his session, which Hart also delivered yesterday, the business development manager will outline how AI tools can optimise and orchestrate people and robots to support distribution centre objectives.
Having enjoyed steady footfall to Stand 106, and speaking to a packed-out conference theatre yesterday, Hart said Lucas Systems had enjoyed an excellent exhibition so far.
“A wide range of people from a wide range of industries have come to the stand looking for various different types of solutions, which is excellent. There seems to be a real, broad interest in different solutions.
“We also had a seminar session on the five myths of getting robots to work with people, which was very well-attended; it was really good to see so many people turn out for that, especially first thing.
“Overall, there’s been a really good number of attendees,” enthused Hart.
At Stand 106, visitors can play a game of optimisation against Jennifer, which Lucas Systems describes as the brain of its robotic operations. Attendees can use an interactive screen to try and beat the AI to achieve an optimum picking path. As Hart explained, “it shows how AI can be used to work better.”
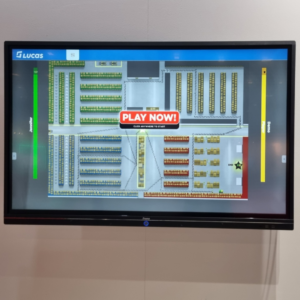
Also on display is an array of pallet-matching and path optimisation solutions that use AI to optimise distribution centre processes for foodservice distribution, particularly in pick-to-pallet operations.
As visitors are learning, Lucas Systems’ intelligent pallet-matching solutions use algorithms to create optimised assignments, with order priority, selection location, travel cost, product attributes and other factors being evaluated.
The stand’s technical team uses a series of videos to demonstrate how Lucas Systems uses path optimisation algorithms and a virtual map of a facility to compute a travel path that does not follow a strict location sequence. The algorithms also take into account a user’s starting and end points, aisle travel restrictions (one-way aisles, for example) and other factors.
According to Lucas Systems, this can help improve on previous scan-based processes, with selectors able to pick two orders in a single trip by grabbing two strips of case labels. Previously, selectors had to manually manage the two strips of labels to be sure they were using the right ones, thereby adding time to every pick.
Instead, the Lucas system on display shows how the server automatically merges the picks for more than one assignment into an optimal pick sequence. What’s more, the choice of solution on display emphasises “the orchestration of both robots and people”, according to Hart, before adding that “the industry is not up to scratch on AMR optimisation”.
To ask any questions about optimising warehouse travel or human-robotic relationships – or to see if you can beat Jennifer – visit Lucas Systems at Stand 106 today!