Dr Paul Rivers, CEO, Guidance Automation, explores what increased robot collaboration means for businesses, and how increased deployment of technology means that we’ll soon need a tea room for the robots too.
Robotics is being used in a variety of industries and applications, with new use cases being defined almost daily. For example, the rapid growth of e-commerce over the years is showing no signs of slowing, with online sales due to account for over 50% of retail sales over the next decade. Within the UK, online spend is predicted to increase 29.6% by 2024, with more than 50% of UK consumers now choosing to shop online over the high street. As e-commerce continues to expand, the demand for warehouse workers is growing at a rapid rate, creating an even greater need for automation.
In order to keep up with rising demand, industries are turning to solutions that can supplement the existing workforce with robotics, paving the way for the collaborative robot, or cobot. By augmenting human labour with cobots that can take on the repetitive or even dangerous tasks, the human workforce can be freed up to perform the skilled tasks out of reach of machines. But as robotic technology is becoming increasingly more sophisticated, enabling robots to perform roles with accuracy, consistency and safety front of mind, this has also advanced the ability of robot to robot communication around the facility.
The future of collaborative businesses
The more we try to replicate human activity through robotics, the more sensors are required to replace the things we take for granted as humans. While it is possible to replace a human in virtually all picking and manufacturing aspects, there are still intricacies which can only be handled by a human worker. This is where cobots win over.
Tasks that can be automated cost effectively will be transitioned, not only helping to reduce time costs, but also through error rate reduction and saving on resources required in error correction. Above all, the real gain from cobots is from identifying the tasks in your facility that can be automated or improved with automation, but still keeping the human worker doing the tasks which are currently too expensive or intricate to do via a robot.
Often, the process has to be changed to adapt for automation or part automation, so the human might be doing part of a task, in a different way to how they were doing so before.
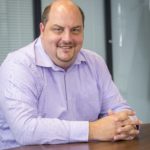
As technology costs reduce, the capability of the robot increases. Collaboration will switch completely over the next decade; from humans doing all or some of the work, through more and more task sharing and then eventually transitioning to the robot doing virtually all of the work needed in a repetitive process.
Importance of communication
For this collaboration to work well, communication is key. Both humans and robots need to know and understand what is needed by the other for a good partnership to work. For example:
- Conveyor systems: Intelligent collaboration between a static and mobile conveyor would allow transfers to take place without the need for the mobile conveyor to stop. The main benefit being maximised throughput – i.e. more items transferred. For a baggage handling system, the higher the transfer rate, the better. To achieve that, one vehicle has to collect as quickly as possible and move away to allow the next vehicle to interact. For this to work effective inter-system communication is critical.
- Independent pick wall application. An integrated collaborative solution allows for pick technology to direct the operative according to optimal pick sequence and placement based on the location of the operative and autonomous vehicle. Intelligent pick planning also allows multiple picks to be allocated to a vehicle. Increasing vehicle speeds between pick points and optimising transport routes to pick to drop points, by knowledge of all other movements in the working area, also reduces the overall process time, maximising throughput.
- All transport collaboration: Currently, there are various vehicle types in operation, a mix of manual drive and autonomous. Often different vehicles have no means to communicate. This leads to transport inefficiencies; vehicles interfering with other vehicles’ pathways, vehicles arriving at points at the wrong times etc. If all vehicles communicate and are consequently aware of each other, intelligent routing will optimise transport to avoid congestion and wait times.
Communication will remain a key factor for human-robot collaboration. If we frequently arrange to meet at a specific time and have no means of communication, it is highly likely that at some point, one or both parties will end up waiting or being delayed. Alternatively, if you communicate via email, text or call, both parties will remain updated and could spend their time more productively. For human-robot collaboration, tablets, touch screens, buttons, barcode scans and voice systems can all be used to enable humans to instruct AMRs in regard for tasks to be performed.
Tea room for robots
Robots still have a need for time out. After spending hours constantly moving around, they will need ‘break time’ to recharge. Most facilities will have a place to charge if there is a regular waiting point, but in many cases, the mobile vehicle does need to move to a charging area where others will be gathered. If the robots are moving around for an eight-hour shift, they are likely to be parked in the charging area for 2-8 hours. If the robots don’t need to use the charging room, they certainly will need to use the maintenance room. Like we service our cars at fixed intervals, robots need preventative maintenance. The parts that need the most inspection and care take some time to understand, and so the maintenance programmes are usually based on years of statistics and performance results. This should prevent them from spending too much time in the robot tea room of the future.