Nissan has unveiled a robotic production line at its Tochigi plant featuring the Japanese automotive OEM’s Intelligent Factory initiative.
The initiative is designed to enable the use robotics to support the manufacture of next-generation vehicles using innovative technologies and to help achieve carbon neutrality via zero-emission production systems.
At Tochigi, the robots are used to automate production processes such as tightening and alignment of suspension links, for paint inspection and installation of vehicle components and subsystems such as headliners and cockpit modules.
What’s more, robots conduct inspections of specifications and identify flaws, while quality inspections have been automated using IoT-based technologies to prevent human error and enhance traceability.
Nissan said it has deployed its Intelligent Factory concept in response to major changes in Japan’s business environment surrounding manufacturing, which include a need to break away from conventional labour-intensive manufacturing to cope with an ageing society and serious labor shortage.
In addition, unforeseen situations, such as climate change and pandemics, also need to be managed, while industry trends in electrification, vehicle intelligence and connected technologies are making vehicle structure and functionality more advanced and complex.
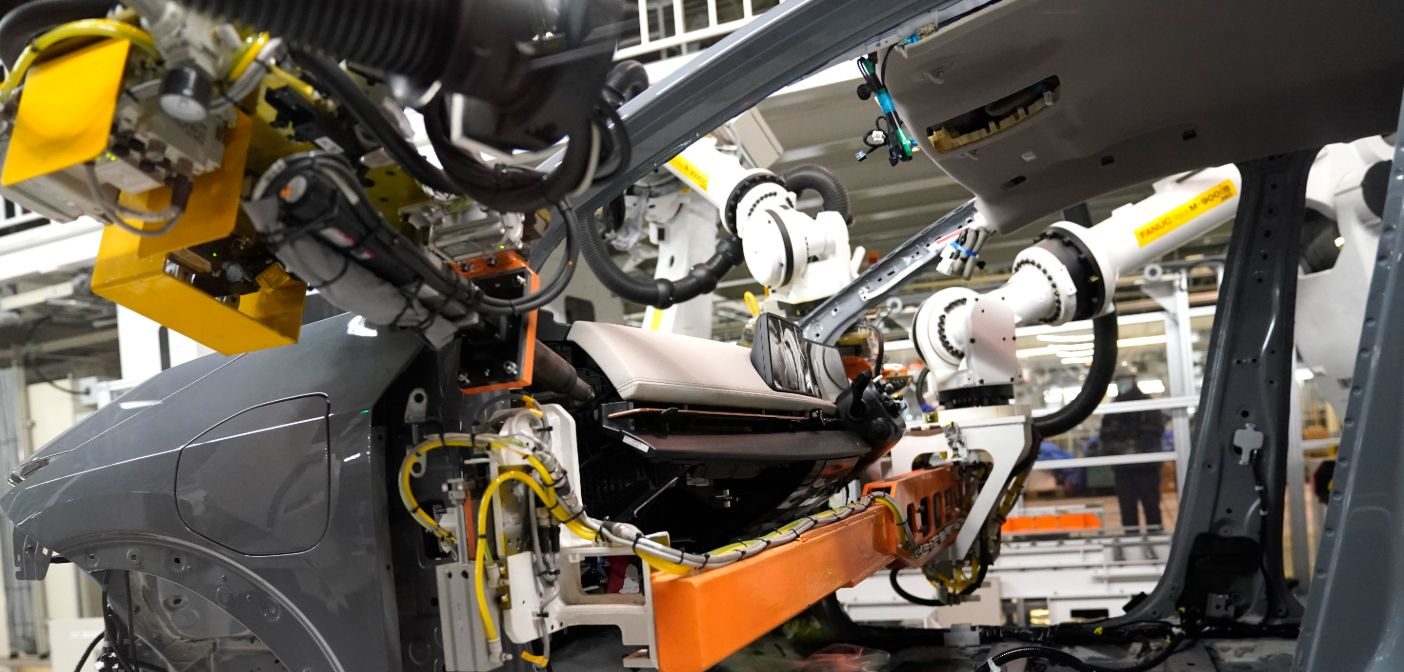
Hideyuki Sakamoto, Nissan’s executive vice president for manufacturing and supply chain management, said: “The automotive industry is in a period of great change, and solving the global challenge of climate change is urgent.
“We see this as an opportunity to build the strength of monozukuri (manufacturing), a part of our DNA, to develop and apply innovative technologies to overcome the challenges we face.”
Nissan’s Tochigi plant is scheduled to start production of the all-new Nissan Ariya crossover EV this fiscal year.
Nissan Intelligent Factory B-Roll: Body and paint shop
- 11 robots inspect the body and bumper, achieving 100% detection of dust and debris (up to 0.3mm in diameter)
- Inspection results are transferred to and stored in a centralised management system, resulting in enhanced traceability
- Inspectors can check the inspection results with a smartphone