ABB has announced the launch a compact interior paint solution that’s designed to help automotive OEMs save on the space and cost of paint booths, as well as reduce their environmental impact.
The solution has been designed to enable carmakers to reduce the size of interior painting stations by one-third via a 3.8m workspace that offers a choice of floor, wall or inverted mounting options. It combines a total of 12 robots that can paint a range of vehicles, including SUVs and large MPVs, with four IRB 5350 door-opening robots and two IRB 5500-22 robots that open the bonnet and boot.
Furthermore, the enhanced working angle of six new IRB 5500-27 7-axis robots reduces the number of robots needed to carry out a particular task and eliminates the need for a linear track. Paint wastage is also reduced by optimising the angle of the atomiser relative to the surface, minimising overspray.
According to ABB, the compact interior painting station reduces the need for ventilation and illumination on the factory floor, thereby helping to make paint operations more sustainable and cost-effective.
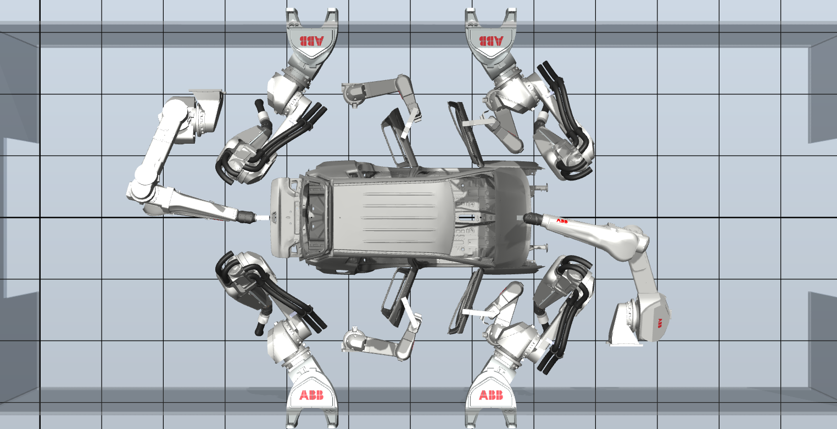
Jörg Reger, managing director, automotive OEM for ABB Robotics, said: “By removing the need for ancillary equipment such as the linear track and additional ventilators, the compact interior painting station can help to significantly reduce the time and cost of setting up a paint booth.
“With its ability to fit into different booth configurations, and with fewer items that need to be installed and maintained, it presents an ideal solution for retrofitting existing paint shops.”
Another benefit of the solution is the ability of the robot to be able to compensate for the one next to it to maintain productivity. In the event of a failure, the remaining working robot will enter degrade mode, either increasing speed to cover the work of both robots or increasing cycle time to cover for the failed robot until it can be brought back online.
Furthermore, use of ABB’s SafeMove software is said to ensure that the robots can work in close proximity to each other. By setting each robot’s working envelope as a safety zone and using it to control their speed and movement, the risk of a collision or triggering of an emergency stop is removed. Use of SafeMove also helps to prevent injury to workers who may have to enter the booth, with the robots brought to an automatic stop as soon as a person is detected.