A researcher at a Swiss university is developing an electronically controlled robot gripper that can manipulate small and fragile objects without touching them.
Created by Marcel Schuck as part of his ETH Pioneer Fellowship at ETH Zurich, the current prototype system comprises two semi-spheres that resemble a pair of headphones connected to a circuit board carrying microchips.
The former ETH doctoral student is using the assembly to demonstrate a phenomenon known as acoustic levitation, whereby a small sphere hovers between the two semi-spheres, held up by ultrasound waves.
Based on an effect first used in space exploration, ultrasound waves generate a pressure field that humans cannot see or hear.
Pressure points are created as the acoustic waves overlay each other, and small objects can be trapped within these points.
As a result, these objects appear to float freely in the air – in an acoustic trap.
As well as making it possible to lift and manipulate small objects without them, Schuck’s method reportedly offers better positioning accuracy than conventional robotic grippers and presents lower risk of contamination.
As such, Schuck believes the innovation could be of interest to the watchmaking industry, where highly precise micro-mechanics is essential for handling expensive minute components.
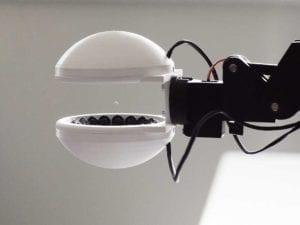
“Toothed gearwheels, for example, are first coated with lubricant, and then the thickness of this lubricant layer is measured,” said Schuck.
“Even the faintest touch could damage the thin film of lubricant.”
Schuck also believes his ‘No-Touch Robotics’ project could also have an economic benefit.
“When working with a conventional robot, a different gripper is required for almost every new shape,” said Schuck.
“However, the acoustic gripper eliminates the need for an extensive set of expensive high-precision grippers.
“It is not even necessary for the robot arm itself to be extremely precise; the exact positioning is determined by the acoustic waves controlled by the software.”
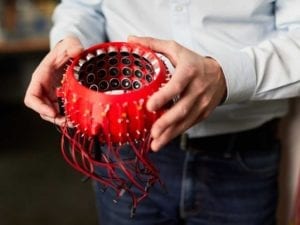
For the current prototype system, Schuck has fitted numerous small loudspeakers into the two semi-spheres, created using a 3D printer.
The associated software allows the 31-year-old scientist to control the loudspeakers in such a way that the pressure points can be moved around.
Using the existing technology, the software adjusts the gripper to the shape of the object to be lifted, and a robot arm then transports the object to the target destination.
However, the main goal of the project is to change the position of the pressure points in real time without the suspended object falling to the ground.
Schuck said he is now using some of the CHF150,000 (£118,000) funding from his ETH Pioneer Fellowship to determine how robot grippers are deployed in practice and to create a type of ‘development kit’ – containing a robot gripper, control software, and instructions –for potential clients.
Should Schuck attract further funding from interest third parties, he said he plans to establish a start-up based on his business idea by spring 2021.
Want to learn more about the latest technological advances in robotics and automation? Robotics and Automation – the UK’s largest dedicated robotics and automation exhibition – takes place on the 3rd and 4th November 2020 at the Ricoh Arena, Coventry. Register your interest now at www.roboticsandautomation.co.uk