A new first-of-its-kind fully connected factory is applying game-changing technologies to help advance the manufacture of the UK’s next-generation combat aircraft system, Tempest.
Located at the Warton facility of BAE Systems, the so-called ‘Factory of the Future’ has been designed specifically to provide a connected intelligent facility for military aircraft technologies.
However, it can also flex to manufacture different products within the same area, leveraging advantages provided by MiR autonomous mobile robots (AMRs) supplied by RARUK Automation and intelligent systems to accommodate changes quickly.
“The AMRs enable a fully autonomous logistics solution for material flow within the facility,” said Ismail Master, manufacturing development engineer, manufacturing technology, at BAE Systems – Air. “We are developing this capability and exploring how it integrates into existing and new production facilities.
The MiR AMRs are part of a wider logistics solution with a dedicated cell comprising a pick-and-place robot, vertical storage carousel and intelligent safety systems.
“This cell is dedicated to storing and maintaining assets from goods delivery into the facility as and when they are required,” said Master. “Full system integration facilitates the autonomous collection and distribution of assets to the wider factory and, conversely, doing the opposite in collecting and depositing assets back into the storage system.
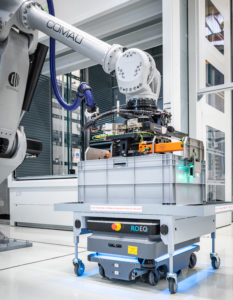
“We are also assessing the capability to connect with other machines and systems as part of our vision to create a fully connected factory.”
Robotics and Automation 2021 exhibitor RARUK Automation has provided BAE Systems with complementary products for the mobile robots, including a ROEQ top module, C300 cart and docking station. Together, these products enable a fully autonomous trolley docking/undocking process, removing elements of manual operator intervention.
In addition, the facility uses a WISE I/O module for the AMRs so they can communicate directly with cell safety systems. As a result, the mobile robots can autonomously ingress/egress into and out of cells without tripping the safety system, again removing any need for operator involvement.
“The main advantage of the MiRs is that operators can focus on high-value tasks, instead of non-value activities like manually distributing assets to the build locations via trolleys,” said Master, who added that having the MiRs satisfy this requirement improves the efficiency of the manufacturing environment.
Thus, it is possible to schedule the delivery of assets so they arrive just-in-time, reducing space requirements for storing assets in working areas and enabling optimised inventory and improved asset management capabilities.
Currently, the AMRs integrate with different cell systems to enable autonomous delivery directly from the working areas. However, BAE plans to integrate the robots to an overarching IOT platform for connectivity, data visualisation and mission orchestration.
“This will handshake directly with an MES to enable scheduling of asset delivery/collection based on the build operations,” said Master. “A future goal is to link the MES to a dynamic scheduling capability that will enable advanced, flexible scheduling of material flow based on the current state of the environment, mitigating any process disruptions via real-time decision making.”
RARUK Automation (stand 302) will be at Robotics and Automation 2021, which will take place on 02-03 November at the CBS Arena in Coventry. For more details, go to www.roboticsandautomation.co.uk