Technology company Continental has developed a sensor-based inspection service for conveyor belt systems. The solution can detect weak points preventing damage that would result in unscheduled downtime.
The technology was developed to the prototype stage in the incubator program of Co-pace, the company’s start-up organisation. It combines camera and acoustic signals enabling predictive maintenance by identifying idler defects before damage occurs.
Inspection of open sections and operations can be carried out from the air using a drone equipped with infrared and RGB cameras that monitors both sides of the belt conveyor.
Covered sections or underground conveyors can be monitored by using fixed microphones installed every 20 to 25m that capture frequency variations in the numerous idlers.
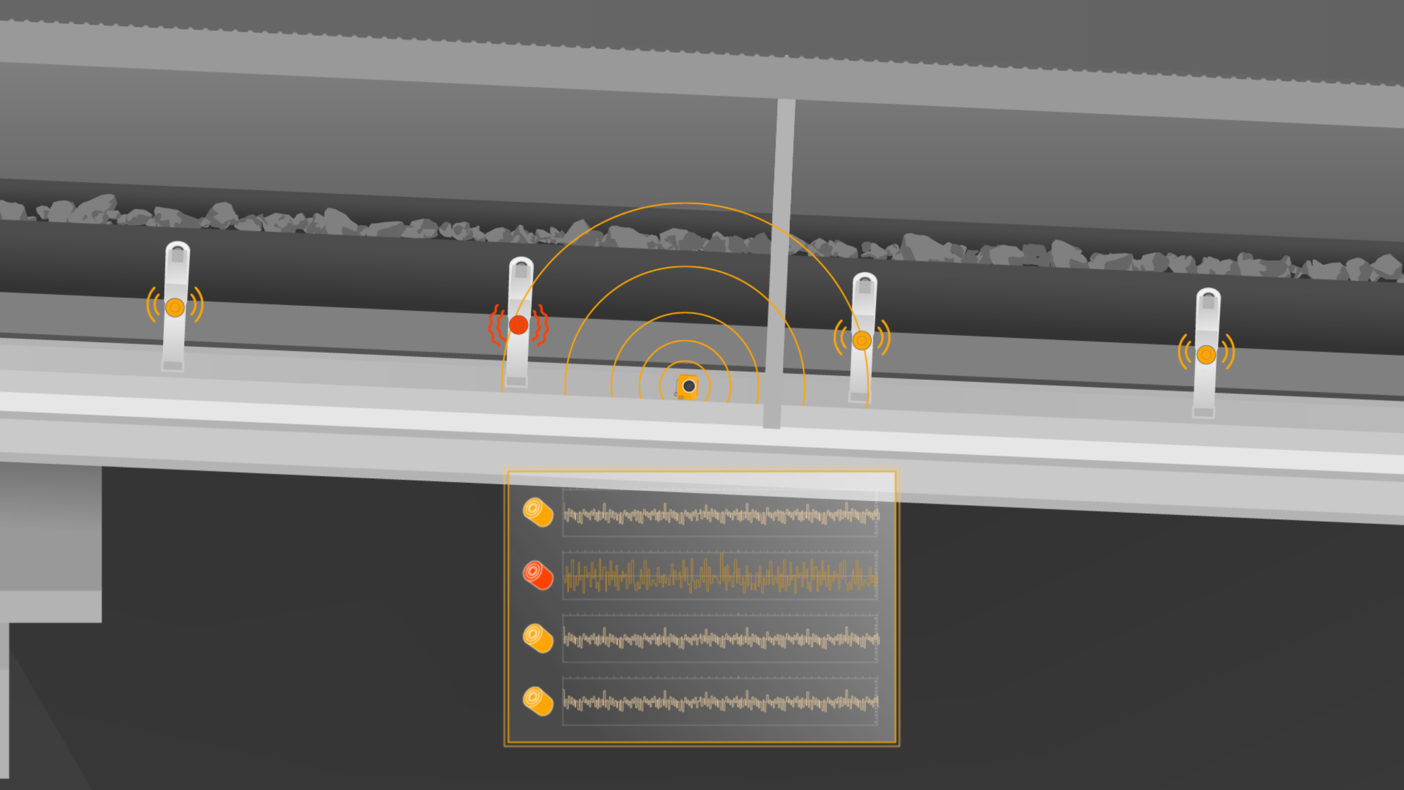
Any event that indicates a damaged idler is then investigated using an AI-based algorithm. Continental said the digital AI-based solution provides data-assisted remote monitoring.
According to Continental, the solution replaces conventional and laborious manual inspection processes. It said the sensor-based technology provides more precise inspection and reduces the verification input.
Clemens Panzer, product engineer of the incubator program at Co-pace, said: “Conventional and often manual inspection methods can be very time-consuming, imprecise or even dangerous for service technicians because of the belt length or local circumstances such as underground routing and enclosed sections.
“Documentation is also often performed manually, with reports having to be manually input subsequently into the relevant datasets. Maintenance intervals also frequently follow a fixed rotational principle, meaning that measures required on short notice to avoid or prevent conveyor failures cannot be carried out in a timely manner.”
Furthermore, the data collected will be automatically available via a user interface. Continental said this allows for demand-driven service planning. Historical data of any changes of the conveyor condition can also be analysed to predict the service life of components.
The solution has been tested in initial field trials, there are further pilot projects planned and Continental expected the system to be in operation in 2021.