Chinese electric vehicle manufacturer Xpeng Motors has revealed details about its highly automated factory in Zhaoqing, Guangdong Province.
Spanning 3,000 acres, the Zhaoqing Xpeng Motors Intelligent Industrial Park houses 264 intelligent industrial robots across five stamping, welding, painting, final assembly and battery pack production workshops.
While the factory, built over a period of 15 months, is run by a 600-person team, the stamping workshop is fully automated.
Steel plates are stamped and formed on a 6,600-tonne large CNC automatic stamping production line, delivering as many as 12 pieces per minute, higher than the 10% industry average, with a precision range as narrow as 0.1mm.
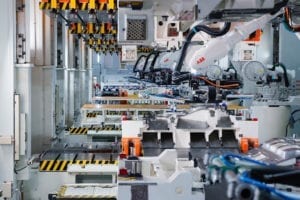
Reportedly equipped with an industry-leading information system, the production process is said to be “highly open and transparent”, with real-time monitoring of processing parameters “to ensure high quality consistency”.
The welding workshop is equipped with 210 ABB industrial robots, performing multiple processes including gluing, welding and aluminium plate riveting.
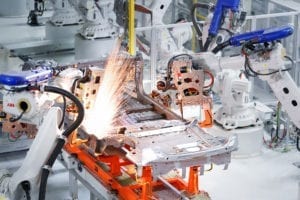
Tier-1 and Tier-2 final assemblies reach a 100% automation rate, with the capability to manufacture steel-aluminium hybrid vehicle bodies.
According to Xpeng Motors, the factory’s self-adaptive medium frequency welding machine achieves a 30% energy saving, while an advanced visual gluing system yields a gluing accuracy of 0.5mm .
The automated painting workshop adopts BASF high-throwing-power coating material, with B1B2+2K water-based varnish double-layer painting technology.
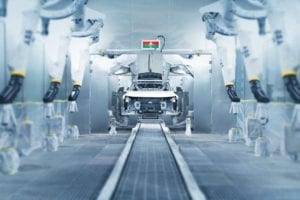
All vehicle components are efficiently assembled in the Zhaoqing factory by an automatic material supply and distribution system, AGV technology, automatic gluing robots and assembly technology.
Furthermore, the pack workshop utilises an AGV flexible production line, combining high-precision visual systems and robots to execute intelligent operations.
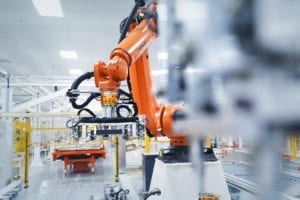
An intelligent end-of-line testing system conducts comprehensive testing – including 198 offline tests and 89 battery performance tests – for every battery pack, including insulation, SOC performance and BMS function to ensure that every battery pack meets IP68 sealing protection requirements.
On May 19, 2020 the factory received an official production license from China’s Ministry of Industry and Information Technology.
“We are deeply proud of our achievement as a young company, in building our own wholly-owned smart manufacture base at Zhaoqing,” said He Xiaopeng, chairman and CEO of Xpeng Motors.
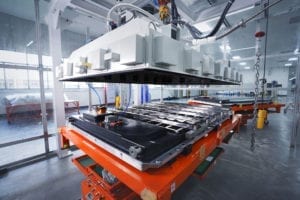
“We are a firm believer that manufacturing is the foundation of smart cars.
“Only when you build solid powertrain and vehicle hardware, can you differentiate with data operation, autonomous driving and connectivity software.
“This not only gives us optimal insight into and control over our production process, it also demonstrates our capabilities in successfully managing our supply chain and executing major projects.
“This is a great base for future development in intelligent vehicle design and manufacture.
Read more from Robotics & Innovation
https://www.roboticsandautomationmagazine.co.uk/hyundai-robotics-receives-major-order-for-industrial-robots/
https://www.roboticsandautomationmagazine.co.uk/kuka-to-supply-production-line-robots-for-e-mobility-provider/
https://www.roboticsandautomationmagazine.co.uk/bmw-places-huge-industrial-robot-order/