GA Pet Food Partners has invested more the £80m into its Ingredients Kitchen as part of an ambitious expansion plan to develop a new dark store warehouse that will operate solely with robots.
According to GA, the investment will guarantee that partners can have complete confidence in the provenance and traceability of all recipes that are produced at the facility.
Three software companies have been involved in automating the entire plant, with a vision to exclude any human error from a “very complex system” that currently sees GA work with more than 700 ingredients and more than 800 different formulas.
In an area of the facility known as the larder, which is capable of holding between 9.8 to 12 million kilograms of pet food, a shuttle transfer vehicle system has been installed to move blue finished containers (BFCs) to storage.
These vehicles move on tracks in a continuous loop, collecting BFCs from the another area of the plant, the parlour, and delivering them to the larder.
The larder can hold 14,864 boxes, each containing 650-800kg of pet food ready for packing. According to GA, the “highly responsive and controlled environment” can handle around 78 box movements per hour.
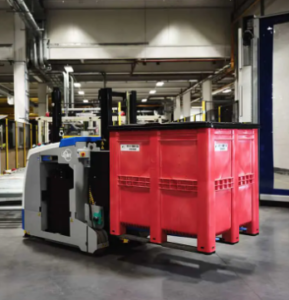
The company has also deployed two types of automated guided vehicles (AGVs), nicknamed Henry and Arthur, to assist in moving ingredients and foods on site.
Supplied by US machinery firm JBT, the AGVs are guided by laser strips installed to navigate them along their route and are fully monitored by a control room via Genesis, GA’s own proprietary IT software that monitors, manages and controls every part of the Ingredients Kitchen.
Henry travels at 2m/s and weighs 1.5 tonnes, transferring containers to and from the pantry. Arthur, at 2.5 tonnes, covers 1.8 m/s moving containers between the cellar and the station in preparation for extrusion.
For battery recharging, the AGVs move into a ‘keep-alive’ zone that enables them to maintain power whilst another vehicle replaces their battery with a fully charged one.
Elsewhere, GA has installed Europe’s first outdoor AGVs designed to travel on a specially-built road.
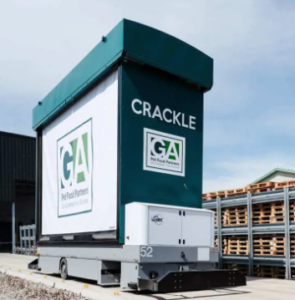
The road features barriers and traffic lights to enable two-way traffic and has three crossing paths for other site traffic.
It also has heat pads to ensure the road is kept frost-, ice- and snow-free, and has been designed to ensure a non-slip environment all year round.
Designed and built in the USA, the ‘camel and mule’ outdoor AGVs are the size of a small van and can carry between three and four batch containers, using magnetic gyro systems for navigation.
After Arthur has followed its dedicated pathway around the far side of the pantry and completes its journey at a conveyor in the station area, batch containers are loaded onto the camel, which can transport up to three batch containers to a pre-extrusion zone in one journey.
When a recipe has been manufactured, it is placed into a BFC and sent via an AGV shuttle mule to the parlour area in the Ingredients Kitchen building. The mule can transfer four BFCs in one journey.
Roger Bracewell, chairman of GA Pet Food Partners, said: “We are thrilled to present this fantastic investment from GA, brought together by the ingenuity, desire and dedication of various skilled organisations from around the world.
“The whole process allows us to track and trace every ingredient into each bag sold to the end consumer, and to be able to guarantee it is safe, having monitored every step.”