For the UK to realise its ambition of becoming the ‘Saudi Arabia of offshore wind’, Yvan Petillot, joint academic lead for the National Robotarium, explains why it is essential for industry to incorporate robotics technology into working practice…
The UK is currently the biggest producer of offshore wind energy globally, creating 10GW a year. However, this is a fast-growing sector and annual production in the UK is forecast to increase to 40GW by 2030.
The zero-carbon target is having a significant impact on the energy sector and, as companies slowly depart from oil and gas, we are seeing a major push toward clean energy. The UK is particularly well placed to exploit offshore wind energy and the UK government is very supportive of this, having recently announced its target of becoming the ‘Saudi Arabia of offshore wind’.
Major energy companies have invested in technology that has driven down the cost of production and installation of wind turbines dramatically, at the same time as reliability has increased.
Furthermore, the energy production capabilities of turbines has almost tripled in the last 10 years: latest-generation wind turbines produce 12MW per turbine, and the biggest farms might have 120 turbines or more, producing the energy equivalent to a nuclear power station for around half the cost.
Overcoming challenges
The advantage of offshore wind conditions is precisely what makes it a difficult environment in which to monitor and maintain turbines, and this results in three key concerns for the industry: cost, safety and operational logistics.
The vision for the future of offshore wind farms is that turbines will be fitted with multiple sensors gathering data about its state and health whilst robots will be deployed to carry out repeat inspections and maintenance tasks. Surface vehicles, such as autonomous boats, might deploy underwater robots to inspect the substructure and the cables that take power out of the turbine; aerial vehicles might inspect and repair the blades; crawling robots could turn their attention to the infrastructure and electric components inside the turbines.
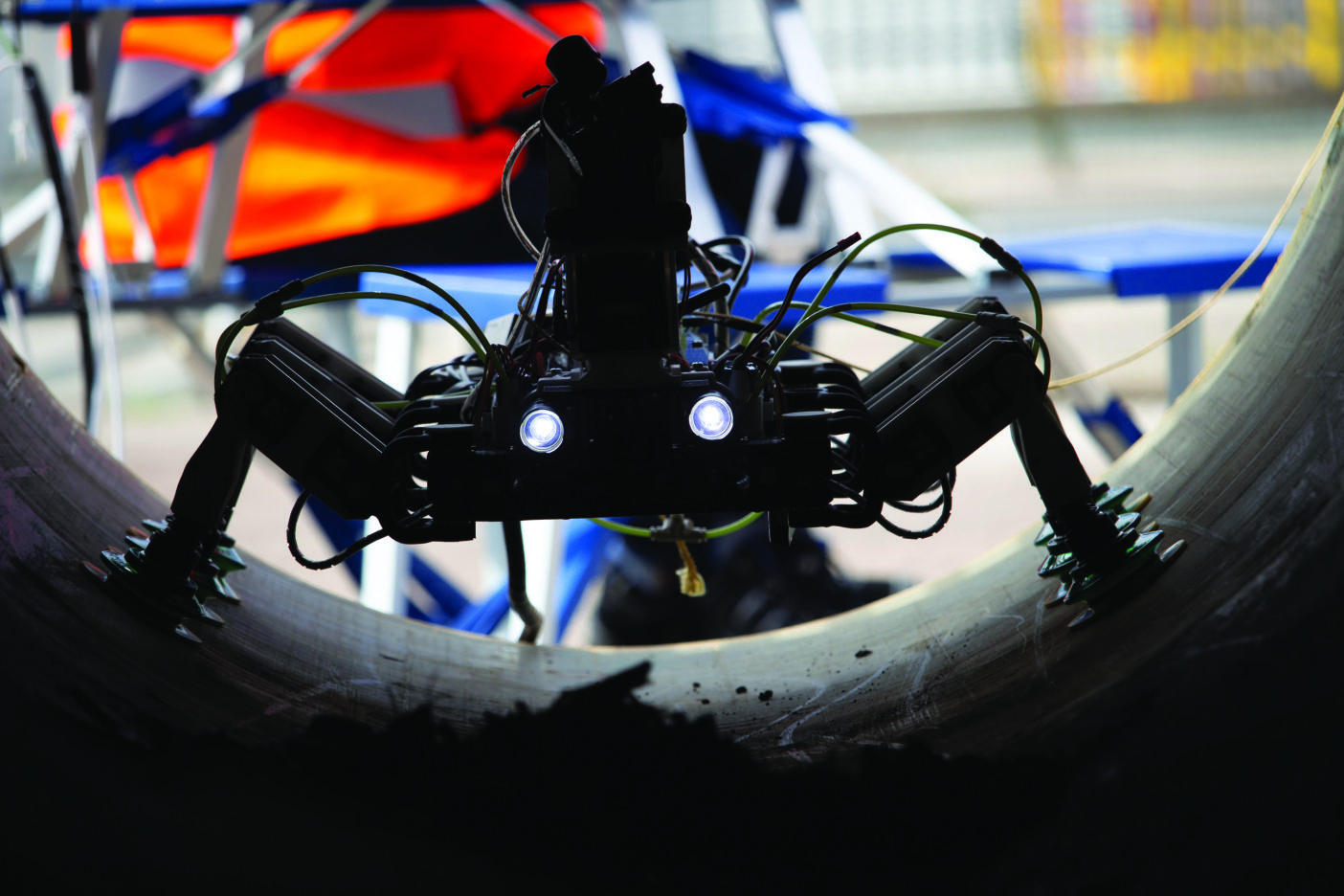
These technologies are already in development at the National Robotarium, a centre for robotics and artificial intelligence research based at Heriot-Watt University in Scotland. Through the Offshore Robotics for Certification of Assets (ORCA) Hub, a consortium of five universities and more than 35 industry and innovation partners, the National Robotarium has become a leader in this area of research, with investment of over £30m.
Over the next decade, together with our industrial and academic partners, we will demonstrate the benefits of robotics to the offshore renewable sector, giving operators confidence that a wind farm is operating properly, information to support decision-making when faced with operational problems, and data to aid the planning process for complex maintenance.
Autonomous robotic systems
In the next 10 years, we can expect to see autonomous systems, image analysis and control applied to the subsea domain in a way that allows systems of robots to coordinate actions to complete tasks. By equipping robots with sensors, including cameras and lidars, we can obtain an extremely accurate 3D image of the environment. From there, a combination of machine learning, artificial intelligence and sensor processing will enable the human supervisors to understand what the autonomous system is seeing and doing and work collaboratively with the remote robot teams deployed in the field.
Advanced control technologies will be used to move the vehicles around the structures, manipulate robotic arms, and deploy sensors or tools to undertake repairs. The final piece of the system is the brain that drives the collaborative mission via three functions: evaluating success; adapting to the environment to perform the task better; and requesting help when failing.
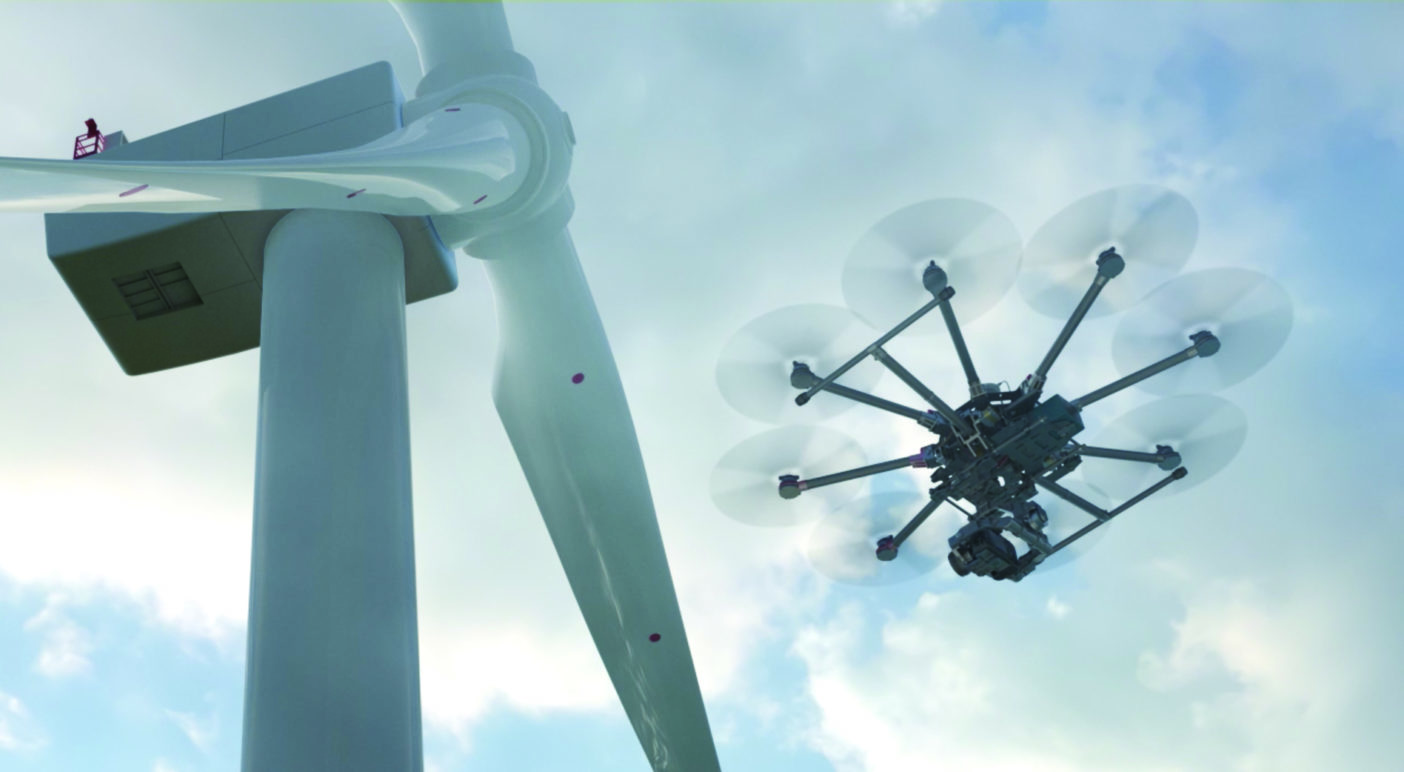
The system described will start semi-autonomously and will move gradually to being fully autonomous in time. There is an opportunity to transition offshore workers to onshore – particularly into roles that analyse, interpret and model data. In order to build trust between humans and robots, it will be necessary to maintain a dialogue between the operator and the robotics technology, and for this reason we will always need human insight. A human operator needs to be able to understand and explain why a robotic system is making the decisions it is.
Some 20-to-30 years from now, technology will allow all inspection and repair work to be done remotely from shore. The technical barriers to communication are reducing with 5G connectivity. Beyond cost, safety and logistics, there is the added advantage of being able to deploy precisely the right engineer, working remotely, to carry out a task.
Retaining a competitive advantage
In order for the UK to retain its world-leading position in offshore renewable energy, it is essential for industry to incorporate robotics technology into working practice. Currently, the sector is defining the robotics capabilities it needs to push down cost and improve safety.
The UK’s success in offshore is mirrored in robotics R&D. And to continue to take advantage of advances in robotics and autonomous systems, it will be necessary to train the workforce at all levels to fully understand what robots are capable of.
Critically, we need to support the emergence of the SMEs that will drive innovation in the field of robotics, and this will be a focus for the National Robotarium. It will enable the vast research that is underway in our academic institutions to be translated into the viable products that are sought after by offshore wind farm operators.
This article originally appeared in the January 2021 issue of Robotics & Innovation Magazine