How robotics and automation can improve storage efficiency, ease labour shortage pressures and drive down energy consumption. Malory Davies reports…
That warehouse that you built 20 years ago might have been cutting edge then, but supply chains have moved on – it might be in the wrong location, it might not be optimised for today’s operational needs, and it might not meet the latest energy standards – an increasingly important factor given the enormous increases in fuel costs in recent months.
Professor Richard Wilding, an expert in logistics and supply-chain management, highlights the fact that companies are increasingly focused on procuring for resilience rather than simply for costs. There is the well-recognised move to on-shoring or near-shoring. And many organisations are looking at multi-shoring, he says, pointing out that there is no point in multi-sourcing if all the suppliers are in one place.
But these are not the only factors, says Wilding, pointing to the development of warehouses from being simply storage locations to value-adding operations offering some final manufacturing and product configuration. He sees this process continuing with the warehouse of the future increasingly being used for a combination of manufacturing and configuration centre. The warehouse is also a good location for servicing and repair of certain products, he points out. And he sees a growing role for warehouse-based 3D printing for certain products pointing out that several different industries could use this to reduce stockholdings of items that are ordered only infrequently.
Tall stories
Not only are operational changes having an impact, rising energy prices have focused people’s minds of what kind of warehouse real estate they occupy, says Kevin Mofid, head of EMEA industrial and logistics research at Savills. Companies are looking at onsite power generation such as solar panels. “If you have onsite power generation, warehouses are going to be cheaper to run.”
As well as power generation, companies are looking at energy saving technology. Mofid points out the energy performance of warehouses is increasingly under scrutiny. Some 90% of warehouses under 100,000ft2 have energy performance certificates of C or lower. “Older, smaller buildings can be very challenging in terms of energy efficiency.” As a result, occupiers are looking for better quality buildings. “We are definitely seeing occupiers being mindful of the cost to run a building.”
Changing landscape
Third-party logistics providers (3PLs) have been seeing a noticeable increase in demand for warehousing in recent years. Traditionally, 3PLs have been unwilling to invest in automation because of the risk that they will never see a return on the investment, but that could be changing.Rhenus is opening a multi-user logistics centre in Bönen, Germany that will be highly automated. Manufacturer Spax will be the first customer at the 106,000m2 site, which will combine very narrow-aisle trucks, pallet stackers and AMRs. Complete automation is used to transport the goods to a wide variety of work areas, store them and make them available for subsequent processes in line with needs.
The company says automation met the challenges posed by a shortage of specialist personnel in the logistics sector. “We regard this site as a beacon project,” says Andreas Mayer, a member of the Rhenus management team.
Demand is increasing, says Mofid, who highlights the expansion of online retail. “The trend is here to stay.” Not only that, trading issues with European Union countries mean that many businesses are increasing inventory levels to improve the resilience of their supply chains. As a result, companies are increasingly needing more warehousing.
Mofid sees multi-storey warehouses becoming more popular in the future. There is a limited amount of land for warehouses and rents are rising. Supply is at its lowest point ever, while demand is higher than ever. “We are predicting rent rises,” says Mofid. What’s more, growing use of robotics and automation means there is more emphasis on using the full cube of the building, says Mofid. As a result, warehouse heights are increasing from the conventional 12.5m to 20m and over. “Height is going to be a differentiator.”
Andrew Weyer, chief information officer at DHL Supply Chain, agrees that scarcity of land “means we need to be smart about how we design and operate warehouses. Robotics and automation solutions are big enablers when it comes to using space wisely. New technologies allow for higher density storage supported by goods-to-person delivery on autonomously guided vehicles (AGVs), creating highly efficient environments.”
Supply chain is controlling everything currently, according to Eric Carter, solutions architect at Indigo Software. “We’ve still got these massive peaks and troughs to deal with. It means businesses are having to flex their warehousing capacity to cater for ever changing supply issues and the changing needs of customers. One way to do it is to have smaller, micro warehouse sites that serve orders for a particular region. Alternatively, they may be taking up much bigger space and consolidating their warehousing into a single, purpose-built space – if they have the money to do it.
“Rising warehousing costs are potentially devastating for smaller businesses especially. They will have to pass on many additional costs to the consumer, which is just going to compound the inflationary pressures that we’re seeing in the UK right now. Having a warehouse management system can help ease some of the pressures of coping with a smaller warehouse space because it enables up to 30% more stock to be stored in a given area,” says Carter.
Must-have technologies
The past few years have seen growing interest in robotics. Wilding highlights the fact that full automation is not appropriate for all types of products, so many operations can benefit from collaborative robotics using relatively low-cost robots. He points out that the investment can be as recouped in as little as nine months.
Nick Hughes, sales manager at Invar Integration, takes up the point saying that with the cost of labour rising and availability falling, businesses will have little option but to adopt higher levels of automation, and in many instances that means robotics. “Their low-cost, excellent flexibility and great scalability makes them the ‘must have’ warehouse technology of today,” he says.
Automation alternatives
Automation will become more important, but it is still expensive – and there are other technologies that might be worth looking at.Indigo’s Eric Carter sees many SMEs investing in elements of automation instead, like a robotic packing arm to speed up processes, without having to fully automate. “At the moment, the cost of implementing a WMS versus full automation for companies that are using manual paper-based systems is very favourable.”
Invar’s Nick Hughes reckons that augmented reality (AR) is likely to start appearing in warehouses soon. Trials are in progress now for AR glasses that can be used to guide an individual to picking locations. “In a way, it’s like a SatNav for the warehouse, but offering a head-up display with information, so no need for a hand-held terminal. The issue at present is cost, but hopefully, prices will come down as the technology takes off.”
Meanwhile, Fergal Glynn of 6 River Systems believes that automation-as-a-service is a growing business model “where automation technologies can be deployed on an as needed basis. Importantly this enables warehouse operations to expand or trial technologies like robotics without needing to undertake a demanding purchasing process”.
Key technologies going forward will be those that improve efficiency, ease the pressure of the labour shortage, and drive down energy consumption, says Weyer. “The Internet of Things (IoT) has huge potential across supply chains and in the warehouse. Condition monitoring will help us reduce energy consumption, create a comfortable and healthy environment for colleagues, reconfigure the operational set-up to maximise productivity, provide predictive maintenance data based on usage and inform how future buildings are designed.
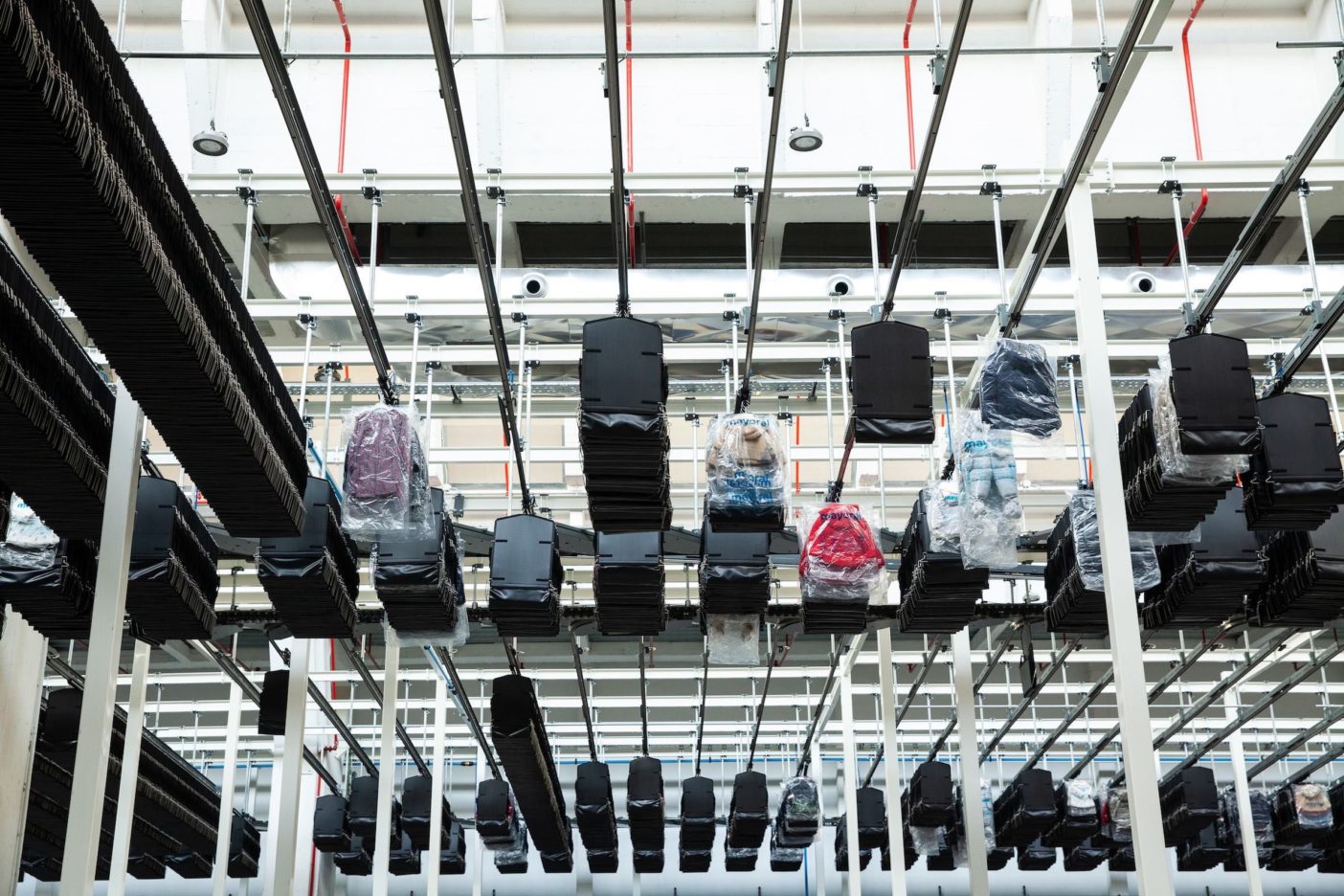
“Because this technology has such major potential to optimise the way our buildings cater for our needs, all DHL new builds in the UK will be specified to include IoT analytics as default. One key example is linking IoT monitoring directly to air conditioning to optimise and maintain correct temperatures so to minimise energy used but also to ensure the integrity of products that need to be temperature controlled.”
DHL is ramping up the roll-out of AGVs and assisted-picking robots, along with goods-to-person robotics. This, combined with automated storage and retrieval solutions, is orchestrated through a single digital platform. “Digitalising repetitive processes through the adoption of robotic process automation tools has also been an area of focus and the key has been fully integrating these solutions with our HR to effectively manage all resources to maximise availability and output. Using algorithmic optimisation and identifying continuous improvement opportunities through advanced data analytics is also an increasingly important area,” says Weyer.
Lost in the shuffle?
It’s no secret that there is labour shortage, but can companies use technology instead of people?Fergal Glynn, vice president of marketing and enablement at AMR developer 6 River Systems, says: “With more warehouse vacancies available than people wanting to take them, the UK Warehousing Association revealed that its members had reported having to increase pay by between 20% and 30% to secure entry-level positions. Warehouse operations must work hard to present themselves as providing attractive career opportunities,” says Glynn.
Ivar Integration’s Nick Hughes says: “It’s not just shortage of labour, the key thing is there’s far more volume going through piece picking warehouses than before, so it’s the fact that the number of people required is not able to keep pace with the increased demand. It’s stretching the labour pool that is there. The requirement for increased capacity is a big driver for automation.”
However, Professor Richard Wilding points out that reduction in labour cost is often less than might be expected. He quotes one global retailer that compared labour costs at a conventional warehouse employing 250 people with labour costs at a highly automated site employing 10 people. The wage bill at the automated site was only 5% less, because of the highly skilled nature of the work.
Conal McGuirk, chief operating officer at Conker, a British producer of rugged, barcode scanner enabled, handheld and wearable devices for mobile workforces, says: “In spite of the increased adoption of technology I firmly believe that there will always be humans in warehouses. It’s just a case of ensuring that the technology is fit for purpose and relevant for the human operatives within the warehouse environment.”
Padraig Regan, chief product officer of StayLinked, which produces terminal emulation solutions, points that the autonomous mobile robot (AMR) market size was valued at US$1.61bn (£1.35bn) in 2021 and is predicted to reach US$22.15bn (18.5bn) by 2030, according to a recent report, Autonomous Mobile Robot Market by Type, by Application, by End-User – Global Opportunity Analysis and Industry Forecast 2022-2030.
“However, future warehouse operation leaders will face the same barrage of information, hype, and noise around robotics, just as those of today face. Ultimately it will come down to affordability; businesses will always seek to increase uptime and efficiency in their warehouse operations, but it will come at a cost,” says Regan.
This article was originally published in the October 2022 issue of Robotics & Innovation. Read the original article.