UK electric vehicle start-up Arrival is not only changing zero-emission mobility solutions but also the very factories in which these revolutionary vehicles are manufactured. Katie Searles takes a tour of one of these trailblazing facilities…
Whist, the Bicester, Oxfordshire home of innovative electric vehicle company, Arrival, may look like a traditional warehouse what is going on inside is far from conventional.
When designing its new fully electric van, the start-up aimed to simplify the design process and rewrite the traditional automotive assembly line format.
“How do we design a vehicle and a new assembly process together – at the same time – in a microfactory?” says Jeremy Offer, chief design officer, describing Arrival’s strategy.
To create this new assembly process, the Arrival team had to change the conveyer belt set up of the 1950s. Currently, a serial system is in place with robotic solutions responsible for each stage of the vehicle production process. Such a system is unable to produce multiple products simultaneously, as it has been designed for one product, one vehicle.
Breaking the mould
Arrival wants to do things differently, “We are revolutionising all of this – the microfactory fixes all these problems,” suggests Giuseppe ‘Napo’ Montano, chief of mobile robotics.
Furthermore, as a typical vehicle production plant would cover millions of square feet, the initial investment is often staggering and can lead to the over-production of thousands of vehicles in order to justify itself.
Arrival Automotive’s CEO, Mike Ableson, wants to step away from this traditional approach and look at vehicle production in a new light. “We aren’t really a vehicle manufacturing company,” he explains, “and I say that because, if you look at the people in the company, half of them are software engineers.
“We are, at our heart, a tech company,” he continues. “That is dramatically different when compared to a traditional vehicle manufacturer.
“One of the great enablers of the microfactory approach is keeping the capital – the investment in the microfactory – relatively low, because that is what allows us to build any of them.”
Arrival’s approach is to only produce what is required, to meet demand without leading to vast amounts of waste, and to use technology successfully to get the most out of a factory footprint.
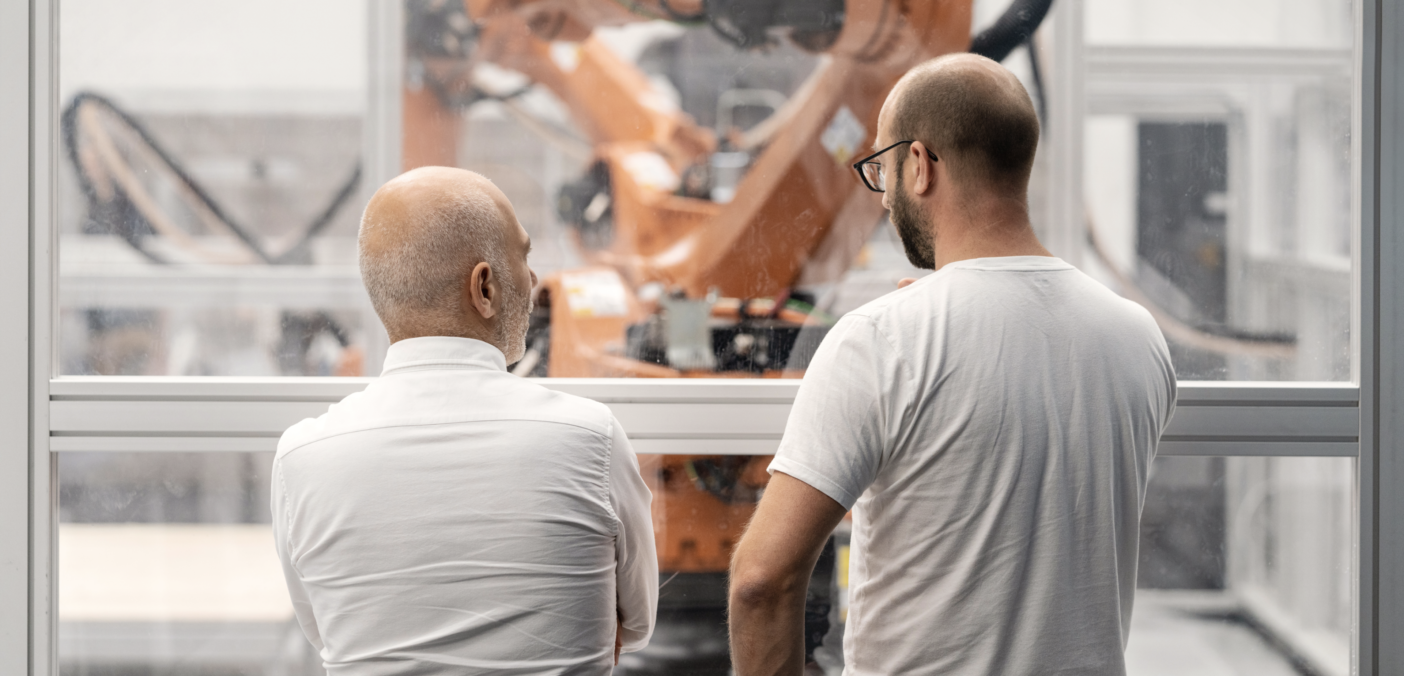
Cellular approach
This is achieved through robotic cells. “These microfactory cells – which average 20m x 20m in dimension – enable us to build a huge number of different products,” adds Raj Vyas, lead process engineer.
“They give us scalability, modularity and automation. The cell architecture is really, really exciting and it is really unique.”
Within these cells, every single stage of vehicle production is handled – from the cutting of raw material, kitting, moulding and trimming.
“We have developed solutions for the materials, the moulding process and the mechanisms of moulding to achieve a low CapEx, light-footprint-manufacturing concept in a warehouse,” explains Rob Thompson, chief of materials division.
“How these steps come together without having to invest in heavy presses, heavy machinery and all of the associated CapEx implications and complications is a really fundamental part of the process.”
The robotic cells are essentially factories within a factory. Featuring a range of robotic arms from several different companies, the systems are driven by computer vision and AI-based control solutions to complete a range of tasks without the need for any tool changes.
The software teams are working to further develop the vision system with the goal of integrating them into the robotic cells, the ultimate ambition to enable the robots to identify specific parts that are required for a particular process, move them and place them into position.
Adopting AMRs
And this doesn’t just apply to the cells either. The team is working on what Montano refers to as the “glue connecting all the elements inside the factory” – the autonomous mobile robots (AMRs).
Currently, the moulds are worked on static tables, but it is only a matter of time before these are replaced by AMRs, according to Thompson.
“AMRs are fundamental to the microfactory story because they allow us to configure cells how we see fit, and the AMRs provide that linkage.
“They will bring the kit from the kitting cell into the moulding cell, the moulding cell will carry out the consolidation cycle and from there we will take the moulded part into the trimming step.”
The robots travel through each stage of the building cells to manufacture the composite panels for the assembly line.
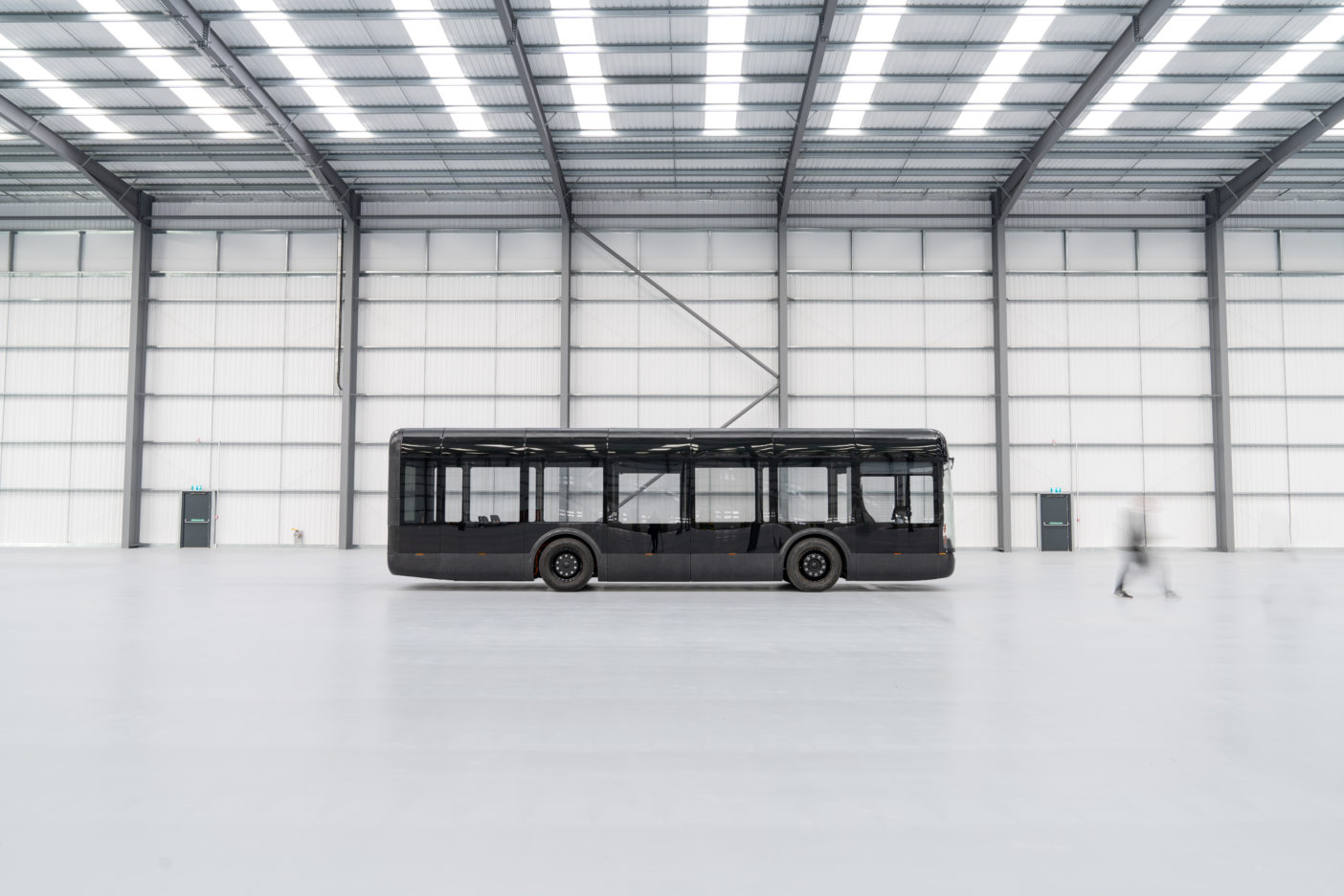
This starts with the raw material, which is cut to shape from the roll with factory software indicating exactly what is needed.
“The machines are incredibly responsive because they are being driven by our software,” reveals Thompson. “We can make different components almost instantaneously, and the factory reconfigures according to need.”
Once cut, the fabric is collected by the end effector and deposits it in a stack, something that Arrival refers to as a ‘kit’. The kit forms the foundation of the moulding process.
As Thompson explains, not a scrap of this fabric is wasted: “Everything that runs through this production line has to be utilised. All of the waste material that comes off here is collected and is reprocessed back into a material that we can use in our body panels.”
After kitting, it’s onto the moulding process. The moulding cell carries out the consolidation cycle and from there it is taken to the trimming stage, before finally proceeding to the assembly with composite panels attached to other panels, metallic parts or other structures. In this last stage of composite part production, one robot works with tool changes to allow it to go from single panels to complex multi-part assemblies that are ready for assembly onto the vehicle.
“The composite parts come off a production line finished,” says Thompson. “This is a really important part because it is about how we are able to distribute manufacturing.
“We don’t have to install the big baths that you would expect with paint lines, with conventional metal body stamp systems.
“We can move into a warehouse and have a factory up and running in a matter of months or even weeks. And it gives us that agility that is so important to our engineering and design approach.”
Cutting costs
Within each of these stages, Arrival has tried to ensure that tooling costs are kept to a minimum while remaining as dynamic as possible. The system also enables them to learn, adapt and evolve to improve the process.
“With the way we are now approaching all of our tooling, jigs, fixtures and processes, it allows us to make changes very fast and without significant cost.
“The technology cells and the factory itself has to keep up with that process – it has to be able to adapt and change.”
Built on a grid-based architecture featuring common robotics, common systems within the platforms and common software ensures Arrival can drive an extremely agile approach.
The team has tried to get as much utilisation out of the footprint of the cell as possible and avoid tool change overs.
Jigs and fixtures are mounted on A-frames, which are rotating so that the robot is in full utilisation. This modular approach allows the parts, robots and processes to work in harmony.
Arrival is also looking to standardise these robotic processes, as well as the way they interact with the robotic elements and the software within the cell.
This simplification of the assembly process feeds into the vehicle itself and according to Offer can be seen particularly on the exterior design of the vehicle.
“The achievements that have been made through this collaborative approach of engineering, design, assembly and build has given us this amazing vehicle,” he says.
This microfactory model has been such a success for the start-up that it aims to repeat the process multiple times across the world, and across varying sectors.
“It is not a question about are there even more opportunities – it is, which opportunities do we want to explore first?” concludes Abelson.
“We are using microfactories – and using the microfactory approach – to produce vehicles but I don’t see why this same idea cannot be applied to other manufactured goods.
“The most profound technologies are the ones that become inner woven into the way that you live your life, and the way that society operates. Eventually they become such an integral part of the way things are done that you forget they are there.”
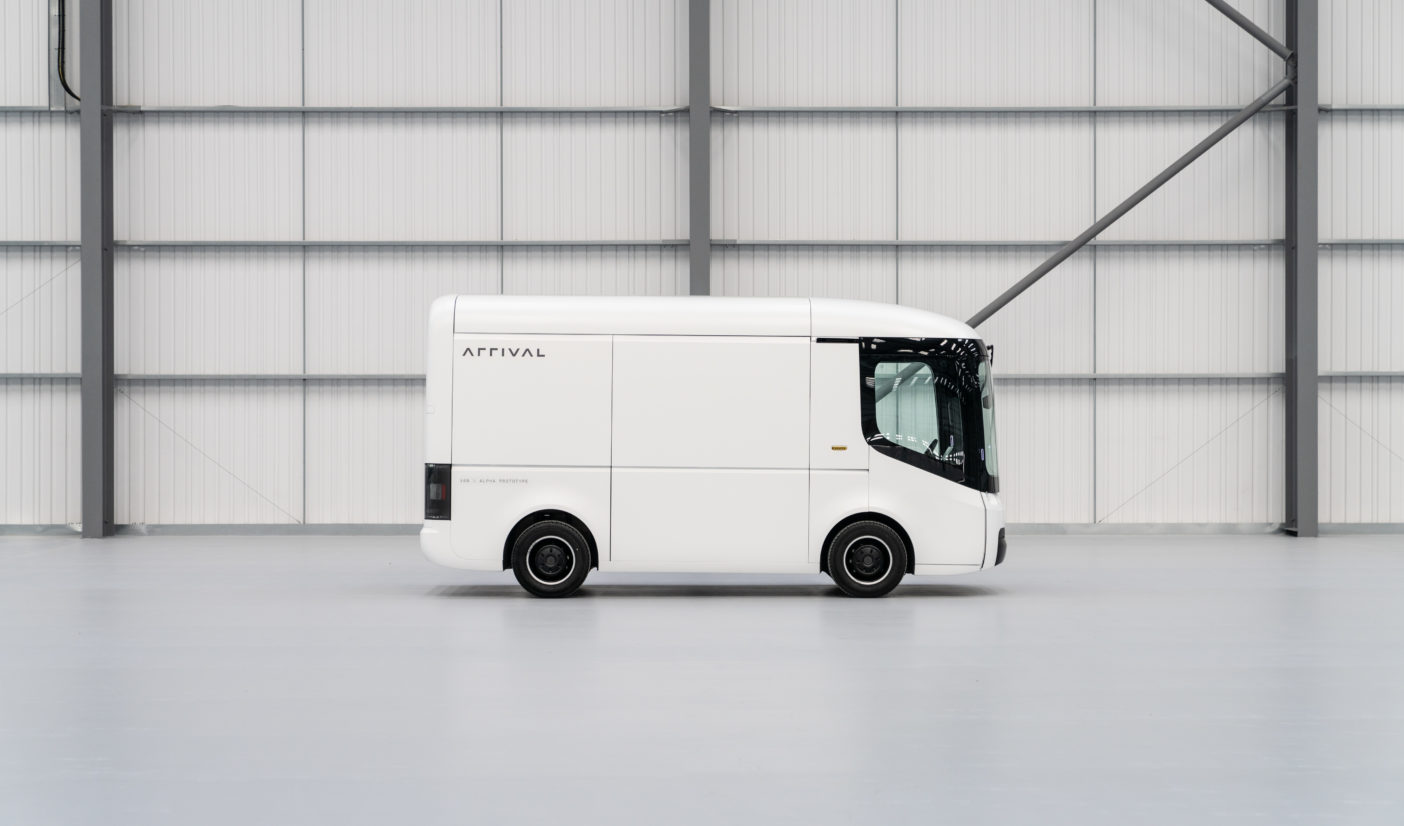
Arrival – at a glance
- 1,200+ employees across Europe and US
- US$5.4bn (£3.82bn) enterprise value with approximately US$660m (£466m) cash in gross cash proceeds to fund growth
- Signed contracts with a total order value of up to US$1.2bn (£845m) including 10,000 vans from UPS
- Microfactories in UK and US expected to start operations in 2021
- Four vehicles expected to market by 2023, first vehicle expected to start production in Q4 2021
- Profitability expected by 2023
- Microfactories lower costs: OpEx of US$120m (£84m) – 100,000 units/year vs. US$240m + (£169m) per traditional OME Low CapEx
- Highly scalable: 20km2 factories vs. 2,000km2 + for traditional OEMs