How robotics are taking e-commerce to the next level. Words by Michelle Mooney…
In the last decade or so, automation has been one of the biggest buzzwords in the warehouse. But what was once a far-off, futuristic goal – specifically robot deployment – is now the standard for most modern, large-scale operations. Part of the reason why automation has seen such a huge scaling up in activity is because of e-commerce.
“The modern warehouse is experiencing a huge shift with UK online sales expected to rise by up to £67bn over the next five years, and e-commerce driving an additional requirement of 92 million square-feet of warehouse space,” says Kerrin Arens, managing director at REPL Group, part of Accenture. “At the same time, consumers are demanding their deliveries are quicker and more convenient.”
In a time when demand is at its highest, Arens believes that “warehouse management software and technology such as robotics, automation and warehouse devices will be key to ensuring the supply chain and warehouses are as efficient as possible”.

One might be mistaken to think that putting as many items as possible through a warehouse to go on to be delivered to customers is the most important ambition in an operative’s mind. Yet, automation provides much more value to a warehouse than this. “It is more important to think about the end-to-end process as that is what will make the whole system more efficient, says Erik Gaarder, senior AI business consultant at Digital Workforce Services’ business and service development unit.
“It is important that resources are not poured into making each silo world-class – it is better to step back and think about making the whole organisation an end-to-end process and allowing automation to provide interpretations, predictions and, ultimately, decisions, as well as performing mundane tasks, that maximize the business value for a company,” continues Gaarder.
Indeed, as Gaarder suggests, automation should be considered throughout every part of the process, and not just as a means for increasing overall delivery speed. This is how modern automation can create meaningful impact in the supply chain. For example, automation can provide warehouse operatives with more security over their processes, which, in turn, can streamline operations and reduce cost by maximising the return per square foot “on the capital investments companies make in distribution facilities”, according to Ronald Binkofski, vice president and general manager of Honeywell’s warehouse automation business for Europe.
Binkofski says: “Automated systems stabilise these variables because they’re designed to precisely handle inventory replenishment, picking and order consolidation with minimal human involvement or direct interaction.” Likewise, Dr Paul Rivers, managing director at Guidance Automation, believes automation increases the efficiency of a warehouse. According to Rivers, the most efficient systems “have the fewest humans”. And with efficiency and consistency at the heart of the operation, “waste can be eliminated, and errors reduced, leaving optimisation and lower operational costs to become the focus”.
Feel the power
Innovation, it would appear, is transforming the modern warehouse into an automation powerhouse with all kinds of technologies working in unison to create more efficient supply chains. One such technology comes from the labelling industry. Denis Brett, managing director at Industrial Labelling Systems, explains that digitisation is used as a tool to improve safety and drive efficiencies.
“Taking people out of challenging environments and avoiding the need for people to get manually involved in processes helps make factories safer”, he explains, before adding that the company’s ‘FlexWipe’ pallet labelling system can automatically stop and pivot itself away from foreign objects, including employees. “This removes the need for cumbersome cages and safety coverings, thus allowing for easy access when changing label rolls and inks and minimising the production floorspace needed.”
However, despite the obvious benefits, SMEs are among some of the most reluctant businesses to adopt automation and digitisation, according to Rivers. This, he says, is because SMEs often lack the confidence to adopt such technologies. However, with the right sort of automation in place, workforces can take on more “advanced, value-added jobs to better manage process changes as they arise”.
For example, “taking a collaborative and cost-effective approach, one or two robots can be added to any size manufacturing business without disruption, while delivering business improvements such as reallocating staff to more profitable areas and allowing the robot to undertake the repetitive labour,” says Rivers. By adopting automation, even small companies can improve overall productivity and job satisfaction, leading to better labour retention.
Importantly, Rivers suggests, there is no need to rush the adoption of automation. “SMEs can realise the benefits of automation with a gradual or flexible approach,” he says. “To begin this process, SMEs should partner with an automation expert to undertake an assessment of their current warehouse or production facility to assess and advise on the viability of the project. An expert will be able to identify possibilities of where automation can be added, and the benefits and efficiencies that can be gained.”
Winning combination
Although the aim of automation is to increase efficiency by reducing the need for employees to complete otherwise mundane or repetitive tasks, a combination of humans and machines are needed for the perfect automation model, according to Dionne Redpath, CEO and warehouse division director at Europa. She says: “Artificial intelligence is needed across the warehousing sector to minimise the over reliance on humans and to counteract future economic shocks. However, at the same time, both people power and technological transformation provide the perfect blend.”
Hand in hand
Collaborative robots (cobots) are one of the more exciting aspects of warehouse automation, and they are becoming way more popular, too. From robotic arms to AMRs and AGVs, the modern warehouse has seen an in-flux of futuristic technology only previously imagined in dystopian sci-fi films. Today, however, these technologies, which include solutions for picking, moving, sorting, and storage, serve the purpose of increasing efficiency, reducing employee fatigue, and saving on costs.
According to Simon Houghton, head of sales and marketing for the UK and Ireland at Geek+, the reason for investment in such robotic technologies such as AMRs is because they “operate at speeds and heights not safely possible for human workers”. He gives an example of the company’s RoboShuttle solution, which can reach heights of up to 8m, allowing for the utilisation of space and improvement in employee safety.
Additionally, AMRs provide value during peak periods because they can be redeployed from one area to another, explains Neil Shelton, chief strategy officer at GXO Logistics. He says the company has, over the last 18 months, accelerated its deployment of modular technologies, which has helped its customers manage the “ongoing shift toward e-commerce in consumer buying behaviour”. Because AMRs boost productivity “by up to 60%”, Shelton says these machines can improve the end-to-end consumer experience by reducing the time it takes to process an order.
However, the versatility of robotics does not stop at its physical properties; a good robot will work collaboratively with digital technologies such as warehouse management systems (WMS). According to Arens, “warehouse management systems can work hand-in-hand with robotics and automation to enable a more efficient warehouse, which is crucial as we see supply chains stretched to new levels”.
Arens continues: “WMS provide central visibility that facilitate continuous improvement, the capacity to scale as the business grows, and a level of standardisation that ensures operational efficiency. Although a WMS is a sizeable investment, without one many warehouses simply cannot operate efficiently enough to keep up with today’s consumer demand.”
AGVs and AMRs significantly reduce issues surrounding labour shortage and the waste of other valuable resources, according to Padraig Regan, chief product officer at StayLinked. He believes that the “automation of manual tasks leads to streamlined warehouse operations with increased levels of productivity and efficiency, which, in turn, help to drive up the bottom line”. What’s more, Regan states automation also “significantly enhances employees’ workplace environment helping them to derive more job satisfaction, crucial for staff retention and recruitment”.
Indeed, the array of tasks an AMR can complete is plentiful and mobile robotics have already proven their value in a variety of warehouse-related jobs. According to Binkofski, AMRs can be loaded or unloaded directly with a forklift or work independently via pick-up and delivery stands. Additionally, AMRs have a greater range of movement than conveyors, which move goods on a set course. “An AMR has the ability to provide a flexible bridge between different conveyor systems in a facility,” explains Binkofski. “Continued innovation supporting the control software for AMR planning, routing and managing the flow of a fleet of mobile robots has been critical to further enabling AMRs in warehouse automation solutions.”
Great expectations
The constant demand from the modern consumer looks set to continue for the next couple of decades and will rise exponentially as the population grows. If humanity does not realise the need to slow down for the sake of the planet, orders will simply continue. And on a small scale, individual warehouses and retailers will need to figure out a way to keep up with these demands. According to Binkofski, today, it is not uncommon for customers to request delivery within hours on the same day. “These market expectations are game changers and is the main driver in adopting automation for 40% of businesses.”
The two principles retailers are attempting to adopt, according to Honeywell, include shipping orders as quickly as possible and supporting an omnichannel delivery system to support e-commerce orders, while also supporting brick-and-mortar stores. This is a world away from the conventional delivery model, says Binkofski; “We’re seeing a big shift from traditional retail-oriented fulfilment, which used to mean a large distribution centre where you may have more than 1,000 people working. This has transformed into the new two-principal model.”
Additionally, e-commerce orders are essentially at their peak during particular seasons of the year. If a warehouse has adopted automation technology in the form of AMRs, AGVs, robotic arms or more, it is much better able to cope with such demands, even during high tides such as Christmas, suggests Rivers, who adds that robotic arms are sweeping the modern warehouse like wildfire as they can perform a range of tasks to ease to flow of goods and speed up general process.
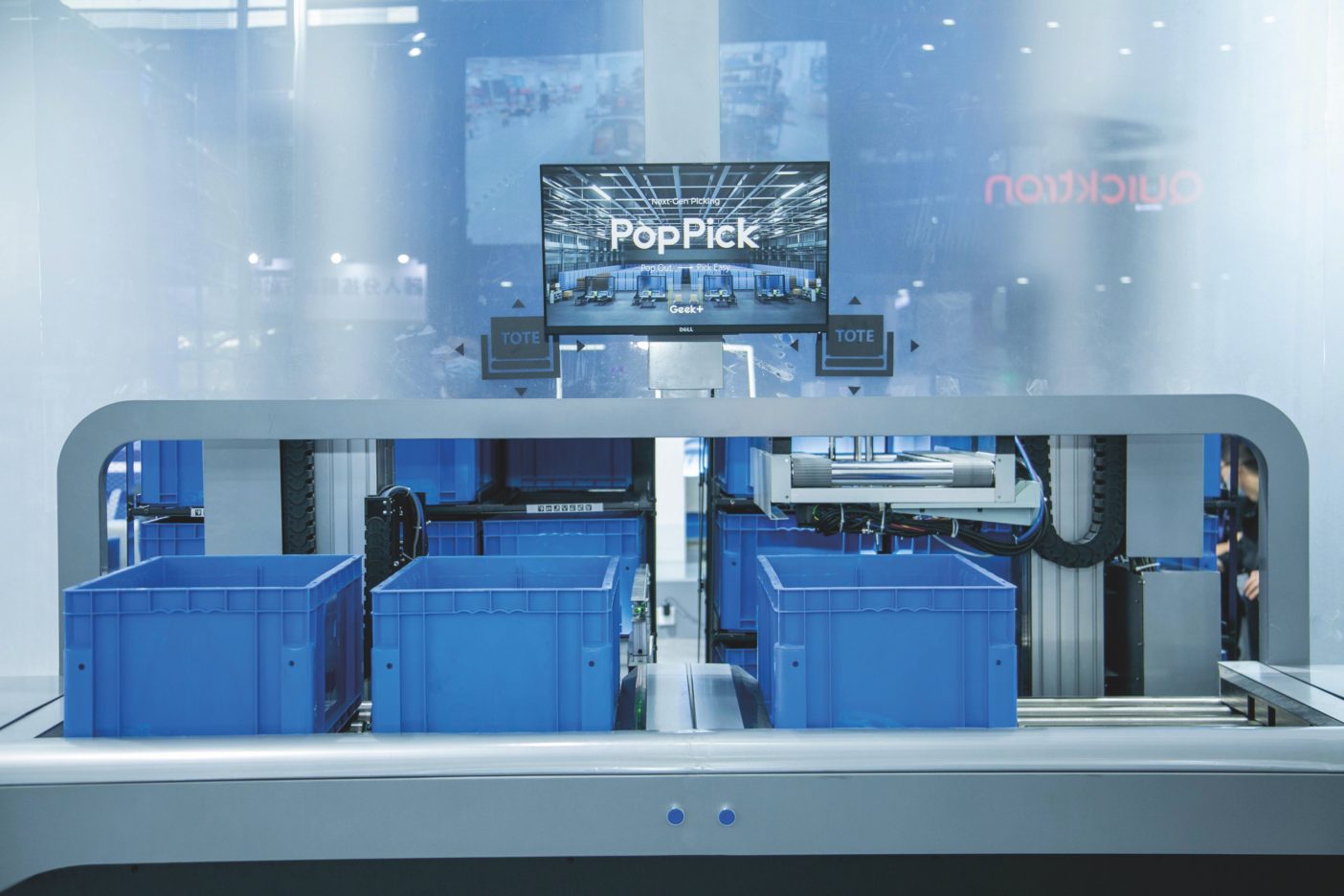
However, Rivers admits that robotic arms are still “learning on the job” as they haven’t yet acquired the skills needed to pick optimally. For one, they do not have the same dexterity as a human. And yet, he still believes we are not far from reaching this sort of transition. “With robotics and sensor technology advancing at such a pace, the fully-equipped robot picker and packer will one day become a reality, making robot ‘hands’ viable.”
And once the technology reaches this level of sophistication, where a robot can pick completely by itself, Rivers adds that it will have “evolved” in its capabilities, thus becoming more affordable, and capable of unlocking other advantages. Ultimately, the real test for all these robotic technologies is whether they can keep up with modern demand.
Planning ahead
Digital technologies working with physical automation include Python API, which, according to Visual Components, is an interface designed to control robots during a simulation. With Python API, manufacturers can create subroutines for tasks dynamically and automate the motions of robots using scripts and helper libraries. Mapping out tasks in this way helps to improve efficiency and highlights any possible issues down the road. What’s more, connecting robots to simulation software enables businesses to verify the accuracy of programmes, check proof of process or remotely monitor them.