Ursula O’Sullivan-Dale explores how inspection robots are being deployed to reduce risks, cut costs and explore hard-to-reach places…
Headlines about ever-advancing robot dogs and drones may make many businesses think a dystopian future is nigh but the reality is that, with these technologies advancing all the time, robots are becoming more and more normal in the modern workplace. One thing all businesses rely on to function is quality control and data collection and, just as other workplace processes have seen a dramatic digital transformation over the past few decades, routine inspections of a company’s assets are no different.
In fact, the continual advancement of robotics, artificial intelligence (AI) and sensor systems means human involvement in monotonous or dangerous inspections is becoming not just avoidable, but actively beneficial for businesses. This is because robotic or automated systems can often complete tasks traditionally assigned to humans more efficiently and effectively, as well as possessing a whole host of other capabilities that mean they can perform jobs people cannot. This is especially true for hard-to-reach places or hazardous environments, the inspection of which is being revolutionised by solutions such as robotic quadrupeds or autonomous drones.
In such instances, thorough inspections ensure risk of incidents is minimised, helping safeguard employees and even preventing fatalities in some workplaces. In others, these bots can ensure the protection of expensive assets and infrastructure, representing an important cost factor for some organisations that rely on high-quality maintenance of expensive parts of machinery. With the capabilities of inspection robots constantly expanding, more and more companies are turning to technology to perform and transform their routine inspection work.
Safety first
One of the principal benefits of introducing automation into a potentially hazardous environment is minimising human exposure to dangerous machinery or situations. As Xavier Orr, CEO of Advanced Navigation, a provider of inertial navigation systems and robotics technologies for sea, land and air, explains, removing “unnecessary risk… for example with mines and industrial plants, [means] companies often require an alternative to human inspection, to ensure employees are not at risk”.
“In this context, autonomous robots are able to inspect the situation or site and confirm whether a human is required,” continues Orr. “The company can then have operators in a remote control centre, reviewing the live sensor data and camera stream provided by the robot.” Operators are thus removed from risk and can make more efficient use of their time, which reduces risk and, often, improves productivity through more streamlined inspection processes.
Another opportunity presented by robotic inspection solutions is heightened accuracy. As technologies become more sophisticated, companies can deploy solutions with a growing number of capabilities to perform a single application. This means inspection robots, which can now come equipped with cameras, sensors, data insight functions and more, can collect a far broader sample of data and enable inspections that monitor a more diverse pool of factors.
On the varied potential of robotic-enabled data collection, Dr Shaun Passley, CEO and co-founder of intelligent unmanned aerial vehicle (UAV) developer Zenadrone, explains that inspection robots can use various sensors, cameras and other technology that offers new and more detailed insights.
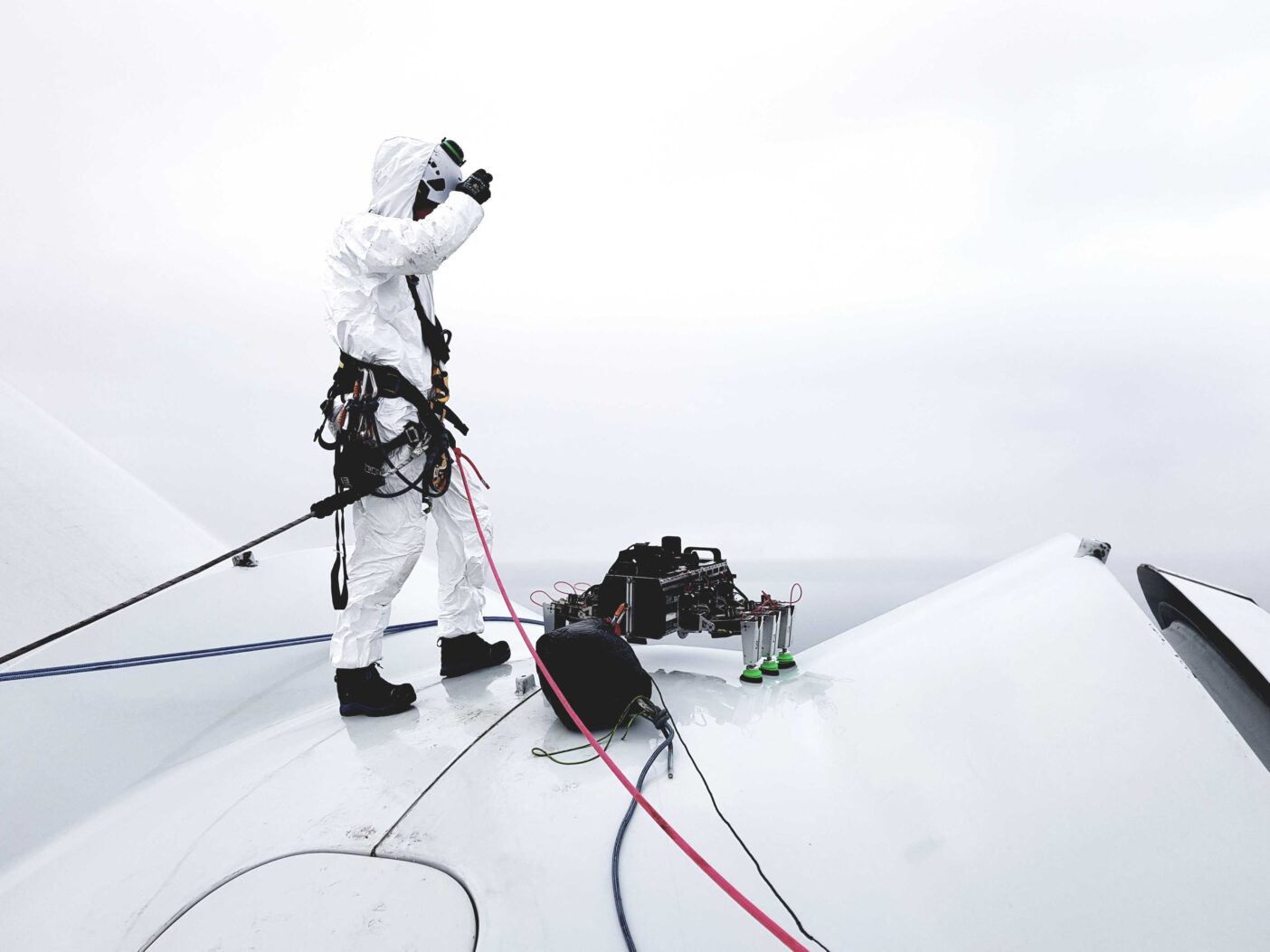
“Robots fitted with cameras can capture high-resolution images and measurements to accomplish inspections faster than manual non-destructive testing methods, while sensors and software can quickly capture and
analyse data.” According to Passley, this means organisations can deploy inspection robots, monitor their progress and ensure consistent inspections to a high degree of accuracy, all while reducing human errors or biases.
Adding to this, Ariel Avitan, co-founder and CCO of autonomous drone developer Percepto, says the post-inspection data analysis process can benefit from automation. “When AI is used to analyse the captured data, employees gain valuable insights that would be otherwise impossible with humans reviewing the data themselves.”
Thus, by improving not just the quality and quantity of data collected, but also companies’ abilities to understand and analyse it to streamline operations, means the use of advanced inspection technologies can have knock-on benefits throughout a business, outside of its initial application.
However, the benefits of more accurate data collection are not reserved exclusively for commercial applications, as Dr Yvan Petillot, academic co-lead at Edinburgh-based centre for AI and robotics the National Robotarium, comments: “Improved data collection can greatly enhance every sector within the UK. Inspection robots can provide the necessary data that allows for immediate assessment and, where needed, correction, that can deliver worldwide economic and environmental impact that will benefit communities around the world.
“We are a single generation away from reaching 2050 net zero goal deadlines, and so organisations can’t afford to let current challenges slow down the construction and operation of essential, green energy assets.”
People power
Despite the number of benefits created by performing inspections remotely or using autonomous machines, sometimes a human touch is still needed. “Inspection robots are still limited in tasks that they can perform,” Dave Walsha, sales manager at EMS, explains. “In an emergency, where a robot may be sent first, it may be possible for it to identify the risk or problem, such as something blocking a pipe or a large crack, but the robot itself may not be equipped to actually deal with the problem. So, while this does give more information to human operators, it’s still unlikely that the system will be able to work entirely autonomously, with no human involvement.”
This lack of contextual understanding can, in some instances, lead to delays in response times, which could, in turn, undo efficiency gains made in other areas. Despite technological advancements meaning inspection robots can collect large quantities of data and process these sets quickly and accurately, they continue to lack the ability to respond accordingly to unknown occurrences.
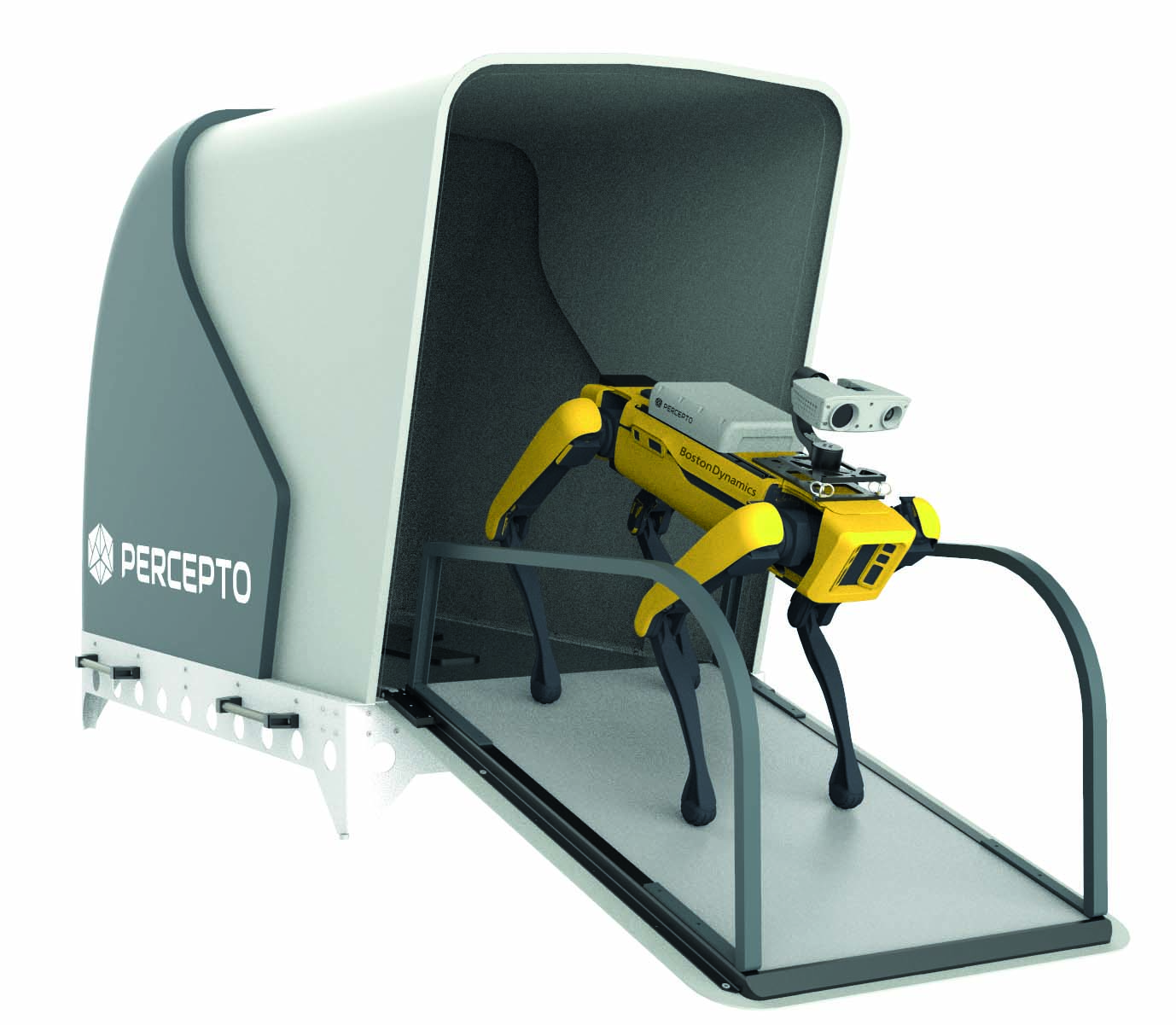
Building on this, Orr adds that robots can be disadvantageous when deployed without the support of human operators. “Robots are excellent at doing what they are designed to do, which is to execute tasks with highly repetitive patterns, but they struggle outside of set patterns.” Thus, in emergency situations, the delay between a problem occurring and a human operator being made aware and having to step in could be critical.
At what cost?
All businesses need to consider the cost of deploying expensive solutions that require significant capital expenditure before introducing them into facilities. These costs can likewise extend beyond initial expense and potentially include facility downtime during installation, the operation of machinery and additional training for employees. Chris Nielsen, founder and CEO of automated inspection solutions provider Levatas, points out that operational costs can be significantly reduced through the deployment of robotics, despite the significant upfront investment.
“Customers are realising reductions in operating costs and increased production efficiency thanks to automated inspection solutions. While upfront costs for these autonomous systems can represent a significant investment, mobile robots and autonomous drones that are enabled with AI can carry out inspections with a high degree of consistency and accuracy when compared to inspections conducted by human workers.”
According to Nielsen, this is because, unlike human workers, robots and autonomous systems can be scheduled to operate 24/7, 365 days a year. What’s more, they can be configured to only alert humans when anomalous readings or potentially dangerous conditions are detected.
In the instance that conditions can be considered safe and without abnormalities, human workers can work on higher value tasks. Neilsen cites the example of one customer who, by eliminating the need to notify human workers, saw a reduced requirement for human maintenance technicians to perform manual inspections across different sites, meaning they were able to tackle a backlog of high value repair work that had accumulated.
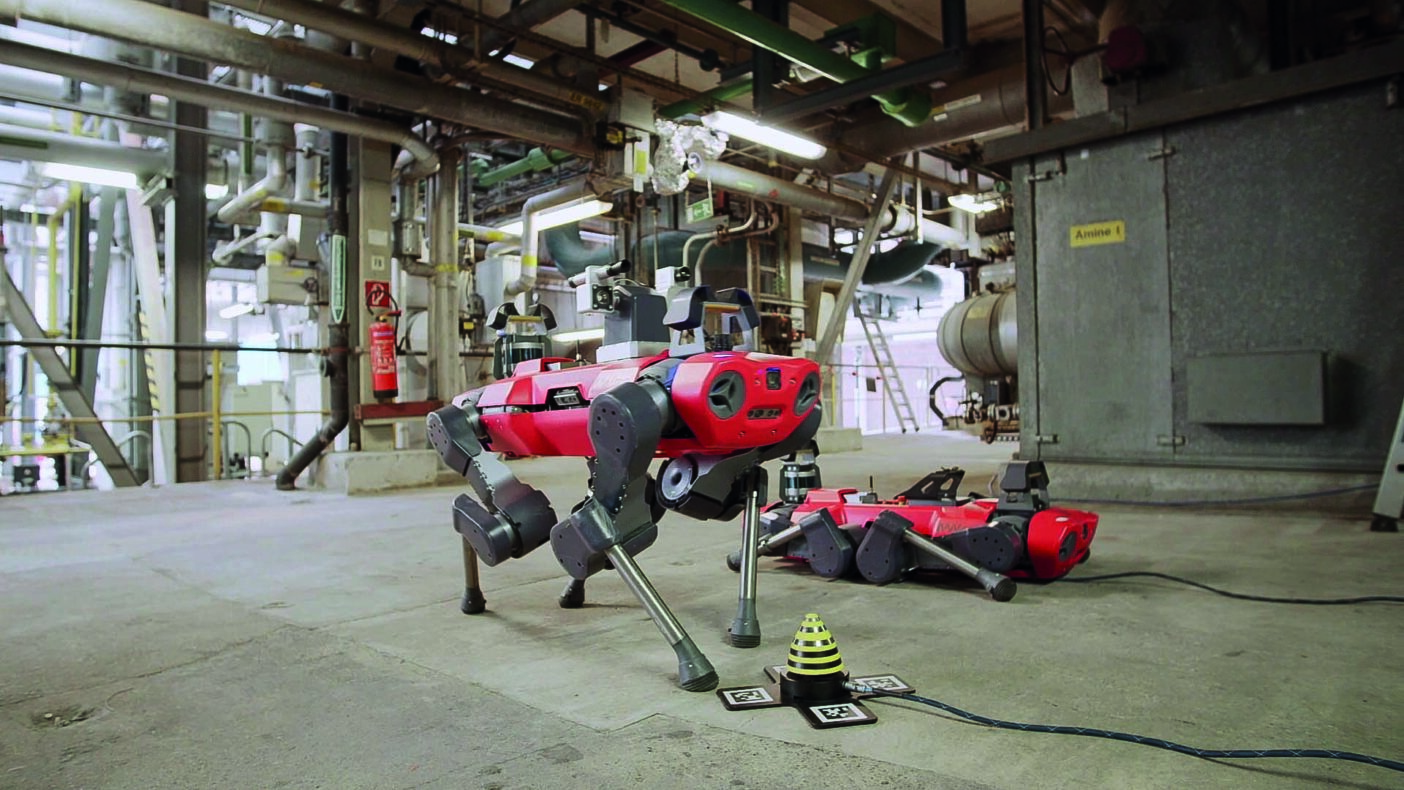
Cutting people out of the equation, at least in the majority of cases, also means that organisations see savings by eliminating or reducing the need for scaffolding, boom lifts, or other equipment needed to ensure worker safety, and can therefore limit downtime spent during installation, Passley adds.
Inspection robotics can be used to cover a growing range of individual inspection tasks, be they mundane, dirty or dangerous, or act as an end-to-end solution to optimise entire workflows. This increased level of reliability is especially critical in industries that are important for both the private consumer or the public, such as energy production, or to companies whose production forms a critical part of a large global supply chain.
Avitan believes that these critical infrastructure sites can increase both the frequency and quality of inspections by automating the entire visual inspection workflow, from data collection to AI-powered analysis and insights, through robotic or automated solutions.
Fundamentally, the protection of valuable assets is key to keeping companies up and running and allowing them to stay competitive. As Avitan concludes, inspection robots can thus be an essential tool that enables productivity while minimising the risk of environmental and safety incidents, enabling companies to achieve key environmental, social and corporate governance goals.
Busy as a bee
Inspection robots don’t only examine man-made environments and equipment; many are used by environmental conservation organisations and wildlife monitoring groups to collect valuable data on species in a non-invasive manner. Some important use cases include gathering biological samples, tracking endangered species and observing plant life.
For example, Ocean Alliance’s SnotBot is a drone modified to collect biological samples such as DNA, stress and pregnancy hormones by flying through a whale’s blow and collecting exhaled snot. This method is both less invasive and cheaper than conventional sample collection methods and helps provide crucial information to monitor how threats such as overfishing and plastic pollution are affecting whales.
Another example of this is Georgia Tech’s SlothBot, which the university describes as ‘a slow-moving and energy-efficient robot’ that hangs from trees to monitor animals, plants and the environment below, which has been tested at Atlanta’s Botanical Garden. With the only required infrastructure being a cable network, along which the bot can move and switch between lines, the SlothBot runs on solar power and can recharge independently by seeking out sunlight.
This article was first published in the July 2023 issue of Robotics & Automation Magazine. Read the original article.