Could collaborative robots keep Covid-19 in check? Italy’s Politecnico di Milano has partially automated the protocol for serological testing using ABB’s YuMi robot, saving time and boosting capacity, reports Anthony James…
The experts are clear – rapid, mass testing is the fastest route back to ‘normal’, identifying Covid-19 infection hot-spots before they spread further and ensuring teachers, doctors and other essential personnel can return to work with absolute confidence and without unnecessary delay.
Unfortunately, demand for coronavirus testing continues to outstrip capacity, with many European test and trace schemes under intense pressure as winter approaches and fears increase over the inevitable arrival of the dreaded ‘second wave’.
Official testing websites continue to crash or freeze, with appointments being offered at test centres many miles away, while many of those who manage to secure a slot report lengthy delays in receiving their actual results due to a backlog of laboratory work.
However, help may be at hand – although the ‘hand’ in question is not human, but instead belongs to YuMi, a two-armed, seven-axis collaborative robot (cobot) first introduced by ABB in 2015 – after the intervention of Dr Andrea Zanchettin, associate professor at the Department of Electronics, Information and Bioengineering of the Politecnico di Milano, Italy.
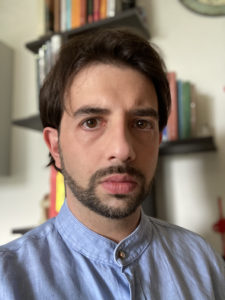
An expert in the field of collaborative robotics, Zanchettin, in partnership with the European Institute of Oncolog y (IEO) in Milan, has adapted a serological testing protocol first created at Mount Sinai Hospital in New York. The Italian professor has devised an application (see How does it work?) that uses YuMi to partially automate the process, boosting capacity.
“At the start of the crisis back in March, I was wondering how my team could help, when I remembered the work we did using a collaborative robot to manipulate pharmaceutical instruments such as syringes and pipettes back in 2012,” explains Zanchettin. “I remembered it as this was quite a departure from our usual work in industrial robotics, at that time.”
Following a televised appeal from the IEO for help in setting up a trial to improve the serological analysis of Covid-19, Zanchettin got in touch to offer his support. “We began by analysing the time taken and the amount of pipetting action required during the whole procedure, and we then figured out that one particular phase – the washing part [well plate ‘pipetting’] – is more or less two thirds of the total task. It was the obvious place to look to save time and improve ergonomics.”
Undeterred by a lack of public funding, Zanchettin began exploring if it would be possible to programme a robot to automate the well plate pipetting, which otherwise requires a laboratory technician to operate the piston of the micropipette eight times for each serological test performed on a single patient.
This procedure can put a human thumb under considerable strain, travelling around 2cm and applying a force of 1.5kg with each press. With thousands of tests currently required on a daily basis, such repetitive procedure places operators at risk of specific clinical disorders, such as the inf lammation of the tendon that keeps the thumb in a raised position.
Robots, of course, have no such concerns, and the results from trials of the new procedure using YuMi are impressive. In nominal conditions, the robot can automate up to 77% of the testing actions and ensure the analysis of up to 450 samples/hour.
“If you have two more arms, ideally you want to double the amount of task you do per hour, assuming that the robot is no faster than the human, which is usually not possible,” explains Zanchettin.
“But you need a task that splits neatly into two parts, one for the robot and one for the human. The serological trial was not so perfectly balanced, so we were only able to speed it up by 65%. Using a robot allows a good increase in the number of tests you can do per hour.”
Why YuMi?
In terms of what robot to use to reduce human workload, Zanchettin did not have to look very far. Supplied free of charge by Robotics and Automation 2020 exhibitor ABB as part of a long-term strategic partnership with the Politecnico di Milano, YuMi was freely available, while also being ISO-5 certified for use in clean rooms, making it ideal for the task in hand.
“I have a lot of experience with this robot, which was already here in the lab,” adds Zanchettin. “It’s not possible to do this application without human interaction, so the only choice was to use a cobot to ensure safety. And, because of the clinical nature of the work, it could not emit particles or dust, to avoid contamination.”
Zanchettin’s team could also call upon RobotStudio, ABB’s off line programming tool, to begin work straight away, despite the university being off limits to students and staff at the height of the pandemic.
“It allows you to work with a virtual robot in a simulation,” he says. “It’s a very efficient tool that helped us save a lot of time by being able to work from home when we couldn’t come into the lab.”
However, simulation can only go so far, according to the professor: “There are drawbacks,” he says. “You cannot really simulate physics – pipetting is actually a very physical task because you have to press the piston down, and within the piston there’s a return spring – it’s hard to accurately simulate the action of the spring, the friction involved and the force on the piston from your thumb.”
Once he was able to return to campus, Zanchettin realised he needed to adjust the application to work in the real world. “The original idea was to have one of the robotic arms holding the pipette, and the other pressing down the piston – but it turned out this was not possible without the use of a pneumatic actuator mounted directly on the pipette.”
Other challenges were of a more mundane, logistical nature: “Purchasing the necessary hardware and material required for the test itself was difficult and very slow,” says Zanchettin, who had to source some of the components from a 3D printing specialist in Belgium, while others came from Japan. “Under normal circumstances, it would take just a few days, but we had to wait up to three weeks as everything was so crazy and uncertain due to the pandemic.”
What next?
To really make an impact on testing will require the adoption of similar procedures using cobots on a much wider scale. However, Zanchettin suggests efforts should be focused on smaller regional or suburban hospitals: “The application is based on an open source protocol, without any proprietary materials or reagents, so anyone can implement it without restriction. By allowing the human to do something else, it is of most benefit to hospitals that may only have two lab technicians, and cannot currently do any Covid-19 testing because they are needed for other activities,” he continues.
“But if you have two technicians plus one robot, suddenly these smaller hospitals are eligible for implementing this procedure. That’s the real value – it’s an intermediate solution that allows partial automation for a relatively small investment compared to what would be required for full automation, and that’s ideal for hospitals with no space or budget for large automation structures.
“The largest hospital in Milan already has full automated liquid handling but most smaller hospitals are still manual. This is where I believe collaborative robotics can really help to scale up testing.”
Unfortunately, progress remains slow: “They’re not prepared for automation – they don’t see the benefit. It’s the same in the wider business world. If you talk to a medium-sized company, they will say, ‘There are lots of nice people here, already doing the task manually and they can do it even better’. That may be true, but this isn’t just about doing it better, it’s also about allowing you to do more.”
On a final note, Zanchettin laments the tendency to view robotics in healthcare as an alternative to highly trained doctors and nurses. “A lot of what is discussed is science fiction,” he says, “with visions of humanoids taking care of people in hospital. Far simpler interventions offer most value. This particular application is not that cutting edge – it’s a response to a demand, which is to increase testing. Simple automation is where we have to push.”
How does it work?
ABB’s YuMi has two arms: the micropipette is attached to the left one, whilst the right has a ‘hand’ of sorts, with two fingers that are used to handle the plates. The technician inserts the patient’s serum into a well plate, which has been previously prepared to host the protein component of the virus. If antibodies are present in the serum, they bind to the protein.After a certain incubation period, the excess must then be cleaned out of the plate – this is precisely where YuMi comes in. The technician positions the plates to be washed above a tray with a weight sensor, which notifies YuMi when it is required to activate and pipette the cleaning liquid into the wells.
The robot collects the plate and moves it into position, then draws the cleaning solution from a reservoir and fills the plate. It then draws the solution back out of each well and discards it, repeating this operation three times.
Overall, the entire process takes around three minutes to complete. At the end, YuMi retrieves the plate and places it on the tray for washed plates.
This article originally appeared in the October 2020 issue of Robotics & Innovation Magazine