Helen Norman investigates how cobot technology is becoming more sophisticated to better serve and support users in a range of industries…
The global collaborative robot (cobot) market is set to grow from US$475m (£337m) in 2020 to approximately US$8bn (£5.7bn) in 2030, according to global tech market advisory firm ABI Research. Furthermore, 2019 research by Interact Analysis has predicted that sales of cobots by 2027 will account for around one-third of the total market for robotic solutions.
With such great growth potential, it is clear that cobots are set to revolutionise the way humans work. They offer a number of benefits to businesses of all size, including increased productivity, contributing to improved ergonomics, and flexibility, as they are often able to be redeployed for a number of different tasks.
Cobot sophistication is advancing fast and nowadays these robotics solutions are being used to serve and support end-users across many industries, such as health and beauty, logistics, food and beverage and even nuclear applications.
Chemical reaction
Researchers at the University of Liverpool have, for example, developed a first-of-its-kind 400kg intelligent cobot scientist, which can work around 22 hours a day with a two-hour recharge time, and carry out experiments by itself. The solution even makes its own decisions about which chemistry experiments to perform next and uses a combination of laser scanning coupled with touch feedback for positioning.
Professor Andy Cooper, director of the Materials Innovation Factory at the university, explains, “The robot scientist was originally developed as part of a PhD project led by Benjamin Burger from 2016 to 2020. It was built to search for new catalysts for solar fuels production, and we are still using it in that research area, although we are now broadening to other areas, too. We currently have two of these mobile robots, with two more to be installed soon.”
The robot is 1.75m tall, has humanoid dimensions and works in a standard laboratory, using instruments like a human researcher does. The robot’s brain uses a search algorithm to navigate a 10-dimensional space of more than 98 million candidate experiments, deciding the best experiment to do next based on the outcomes of the previous ones.
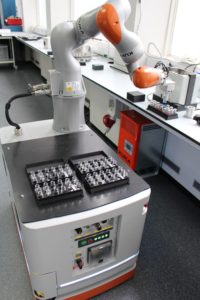
For its first project, the robot conducted 688 experiments over eight days, working for 172 out of 192 hours. It independently carried out experiment tasks, such as weighing out solids, dispensing liquids, removing air from the vessel, running the catalytic reaction, and quantifying the reaction products. During this project, the robot even discovered a new catalyst that is six times more active.
According to Cooper, the team is now looking at how this cobot can be used in different applications. “A more prosaic but still useful application might be to do routine analysis of chemical processes, exploiting the fact that the robot can work 24/7,” he explains. “These robots could also be used for small scale materials or chemical manufacturing, or biomanufacturing.
“A different use case is to perform particularly hazardous chemical processes where you would not want to expose a human researcher. There are a wide range of possible applications across multiple sectors, not only university research, and for this reason we set up a spin-out company, Mobotics Ltd, to develop this technology for industry use,” Cooper concludes.
Test the water
Outside of the chemistry lab, technology development company Createc, which specialises in applied imaging, sensors and robotics, is currently focusing on using cobots in force-feedback control applications, especially ones with real-time human interaction.
“These solutions are either much harder to develop or simply unsafe without cobots, and they cover a huge range of applications,” explains Matt Mellor, CEO of Createc. “Right now, we’re looking at applications that require contact with irregular and unknown objects; in-field weld inspection, manipulating hazardous objects, and applying force-sensitive cutting techniques are the main focus.”
One specific application the company is focusing on is nuclear decommissioning. For this, Createc teamed up with Fortis Remote Technology to develop the Underwater Cobot Decommissioning (UCODE) project, which will see Fortis design and develop a ‘waterproof jacket’ enabling Createc’s cobot to function effectively underwater. The UCODE trial aims to demonstrate that a cobot, protected for use in shallow water, can carry out underwater operations in the decommissioning of a nuclear reactor.
Mellor believes that software developments are making it easier to build adaptive, human oriented systems. “For example, there are some really interesting developments in force-based collaborative interactions with robots coming from R&D groups that we think are going to enable a lot of new commercial applications of cobots in the near future,” he adds. “We also believe that cobots will become more dextrous and delicate, while becoming more tolerant of externally imposed force – or to put it another way, their characteristics are going to get ever more human-like.”
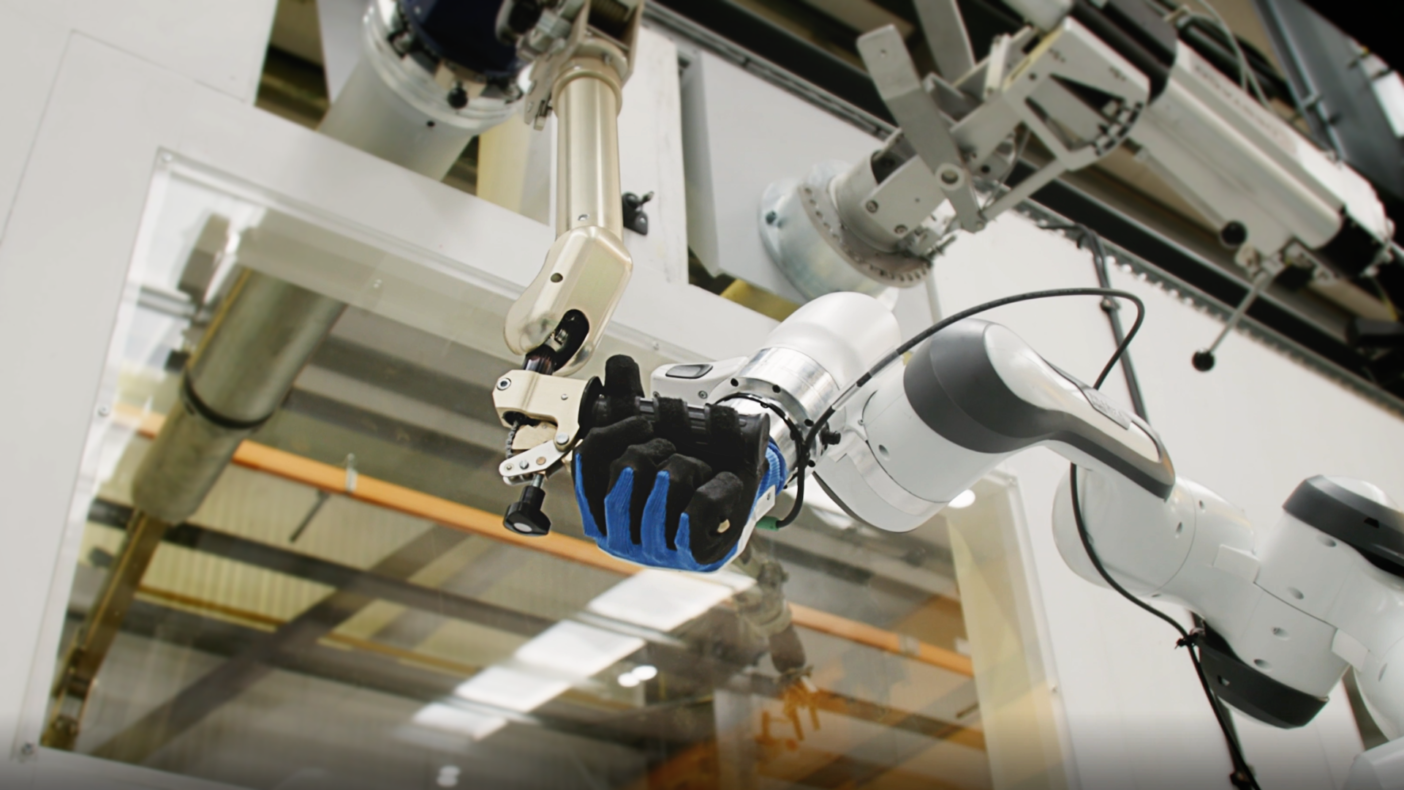
Industrial cobots
Robotics company ABB launched a range of new cobots in February 2021– the CRB 15000 GoFa and the CRB 1100 SWIFTI. GoFa, which recently won The Red Dot: Best of the Best award, has a reach of 950mm, a top speed of 2.2m/s, and the ability to handle payloads of up to 5kg, meanwhile SWIFTI has a reach of 580mm, a payload of up to 4kg and operates at over 5m/s. For maximum safety, GoFa also features intelligent sensors in every joint that stop the robot within milliseconds if contact is detected.
Both solutions have been specifically designed to assist workers with tasks including material handling, machine tending, component assembly and packaging. The new solutions are in addition to ABB’s YuMi dual- and single-arm robots, which were launched in 2015 and 2016, respectively.
According to ABB, AI and machine learning will play a huge role in the future for cobots, where they will be able to think for themselves and create solutions with minimal programming. They will learn from doing the task and solve problems resulting in greater efficiency.
Meanwhile Universal Robots, a manufacturer of flexible industrial collaborative robot arms, has recently launched an enhanced version of its UR10e cobot, which has an increased payload of 12.5kg and is suited for applications such as palletising, machine tending, and packaging.
According to Mark Gray, country manager, UK and Ireland, Universal Robots, the sophistication of cobot technology is exemplified by the versatility of applications. “We’re seeing every industry from automotive to plastics and medical implementing cobots to deliver efficiency and flexibility,” he says. “During the pandemic, we saw an increase in small business owners looking to automate in order to keep their product lines flexible. For example, a small company called Bloom-in-Box used our cobots to switch its production line from manufacturing flower boxes to making masks.”
Gray believes that cobots have the potential to accelerate growth and productivity in many sectors of the economy and reduce the impact of labour gaps from an aging population. He concludes, “Almost every industry can benefit from cobot technology. We’re seeing increased demand for cobots in Covid-19 testing centres, for example, where the process of picking and placing samples can be automated in order to provide rapid results. Cobots can also be used as servers to clean surfaces and even as baristas. Furthermore, advances in connectivity and machine learning means that ultimately robots will be even easier to set up and deploy.”
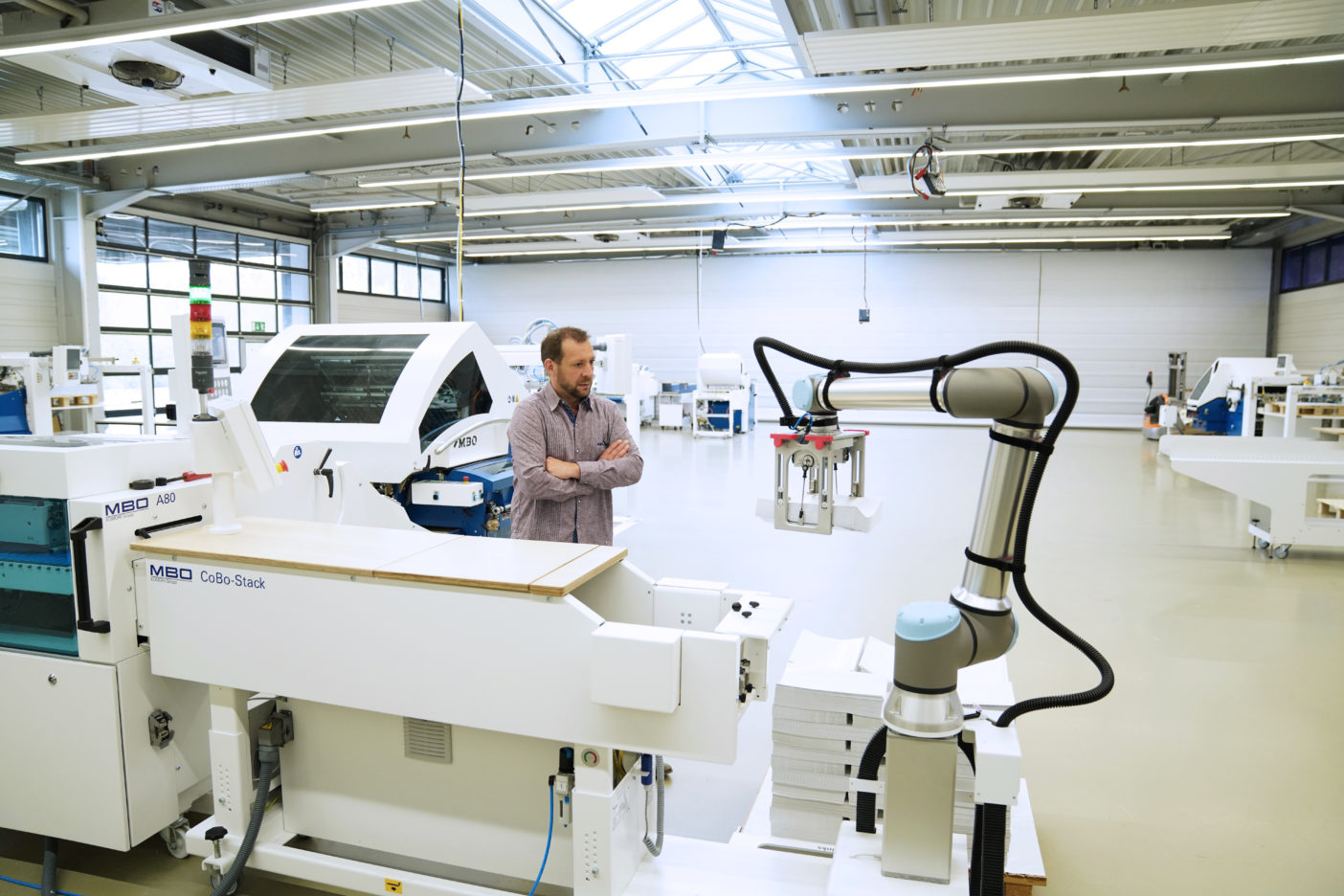
Has Covid-19 accelerated cobot deployment?
A survey carried out by ABB in December 2020 identified Covid-19 as a key factor influencing companies worldwide to consider an investment in robotic automation. Surveying 1,650 companies across multiple industries in the UK, USA, China, Italy, Sweden, Switzerland and Germany, the survey revealed that 85% of respondents said their business had been impacted by Covid-19. Asked how they felt that robotic automation could help to address the impact of the global pandemic, a majority identified factors including enabling social distancing and avoiding cross contamination (51%) and helping to cope with staff shortages or self-isolation (34%).
The survey also asked companies that weren’t currently using robots the reasons why. Of 636 companies that responded, lack of knowledge about how to use robots (24%), lack of experience and in-house technical expertise to operate robots (19%) and a belief that robots are difficult to use (12%) were cited as key reasons for having shied away from investing in robotic automation.
According to ABB, its new SWIFTI and GoFa cobots have been designed to diminish the need for customers to rely on in house programming specialists or programming knowledge. Customers can now unbox their cobots and have them operating within minutes of installing them, with no specialised training required. This lowers the barriers to entry for any industries looking at robotic automation.