Construction robots can do everything from prepare land for building works to laying bricks, but David Smith asks is the industry ready?…
Robotics has revolutionised the automotive sector and there are claims it could transform construction. But a closer look reveals a complex picture. Construction robots tend to carry out specific tasks in safely controlled environments, such as digging trenches. Meanwhile, many new technologies – from bricklaying, surveying, welding and drywalling – are still a rare sight on commercial projects. There are a myriad of solutions, but how to make best use of them remains an open question.
One successful company using robotics on major projects is San Francisco start-up Built Robotics. Founded in 2016 by former scientists from NASA and Google, Built’s technology converts existing construction equipment, including excavators and bulldozers, into autonomous robots that dig trenches, excavate foundations and grade building pads. Built has US$100 million of committed contracts, mainly in mass excavation on wind and solar farms.
“We started with a broad focus, but we’ve narrowed it to trenching and earth excavation on greenbelt sites. Robotics is complex and it helps to focus,” says Gaurav Kikani, vice president. “Sites are geofenced and robots will step over obstacles. Self-driving cars always seem five years in the future because they’re navigating dynamic areas, whereas we’re operating now.”
Robotic equipment operators (REOs) set up Built’s robots, then monitor them. “They work in tandem and coordinate the symphony. This is the future for robotics. Humans are still good at lots of things and robots will carry out specific tasks. I don’t think we’ll ever see an all-in-one construction robot, but I expect robots to usher in a new era of rapid building that will change the landscapes of cities.”
Ready or not
Outside private enterprise, some experts sound a more pragmatic note. Mark Ireland is chief engineer for technology strategy at the Manufacturing Technology Centre (MTC) in Coventry, which operates some of the world’s most advanced manufacturing equipment, including robotics. For example, the MTC’s Fanuc M-2300i is the world’s biggest, commercially available, industrial robot capable of lifting 2.3 tonnes and assembling offsite building modules. “We have seen a lot of discussion around robotics and automation developments for the sector, but we haven’t seen much on building sites yet. That doesn’t mean it won’t happen, but we need to temper expectations,” says Ireland.
Ireland, however, sees a lot of value in the Built approach of operating robots in un-sensitive and controlled environments. But he contrasts them with projects on more complex sites such as those seen on HS2. “Over the duration of the project the team will have had to relocate tens of thousands of graves, for example. Robots aren’t sensitive to that sort of thing. If an autonomous digger hits an old Roman mosaic floor, there is a risk that without the appropriate control systems, it will plough through it. There are also major safety issues, as soon as people are involved working alongside heavy robots that could kill them if appropriate safety systems aren’t in place. So, there is much more investment and development needed than just the robot system itself”
Ireland uses NASA’s Technology Readiness Levels (TRLs) to evaluate progress. Categories 7, 8, and 9, are used to describe the development of technologies deployed in the real world on commercial projects. A new technology working day in and day out across multiple companies would be a Level 9, whereas the first commercial application on a first product or project would be Level 7. Meanwhile, the first three TRLs describe technologies in academic development, and the middle three – 4, 5, and 6 – are operating on real world applications, but only in safe environments, to make sure the business case stacks up, before being used on a commercial project.
Ireland positions most bricklaying robotics at about TRL 6. Although they are operating on real projects, there is often an element of highly skilled technical support in place and it could take a few years before the systems can be made to work day in and day out, without the level of expertise needed to allow the commercial world to embrace them. Another example of a TRL 6, he says, is the Spot robot developed by Boston Dynamics in partnership with laser scanner company Trimble. Spot has been fitted with Trimble’s GNSS laser sensors and field control software. Trimble says it will improve productivity, give seamless control of data collection and ensure worker safety.
“Before a robot is ready for the outside world, rigorous testing is essential in controlled environments. Unpredictable incidents happen even if they seem unlikely. How will the technology perform when being programmed and operated on real sites? How will it cope with very cold or hot weather, rain, snow and ice? Does it have sensors that detect hostile behaviour? For example what if you have a disgruntled employee who keeps kicking a robot down the stairs? Without data it could appear that this terrain is too complex for the robot to navigate,” he says.
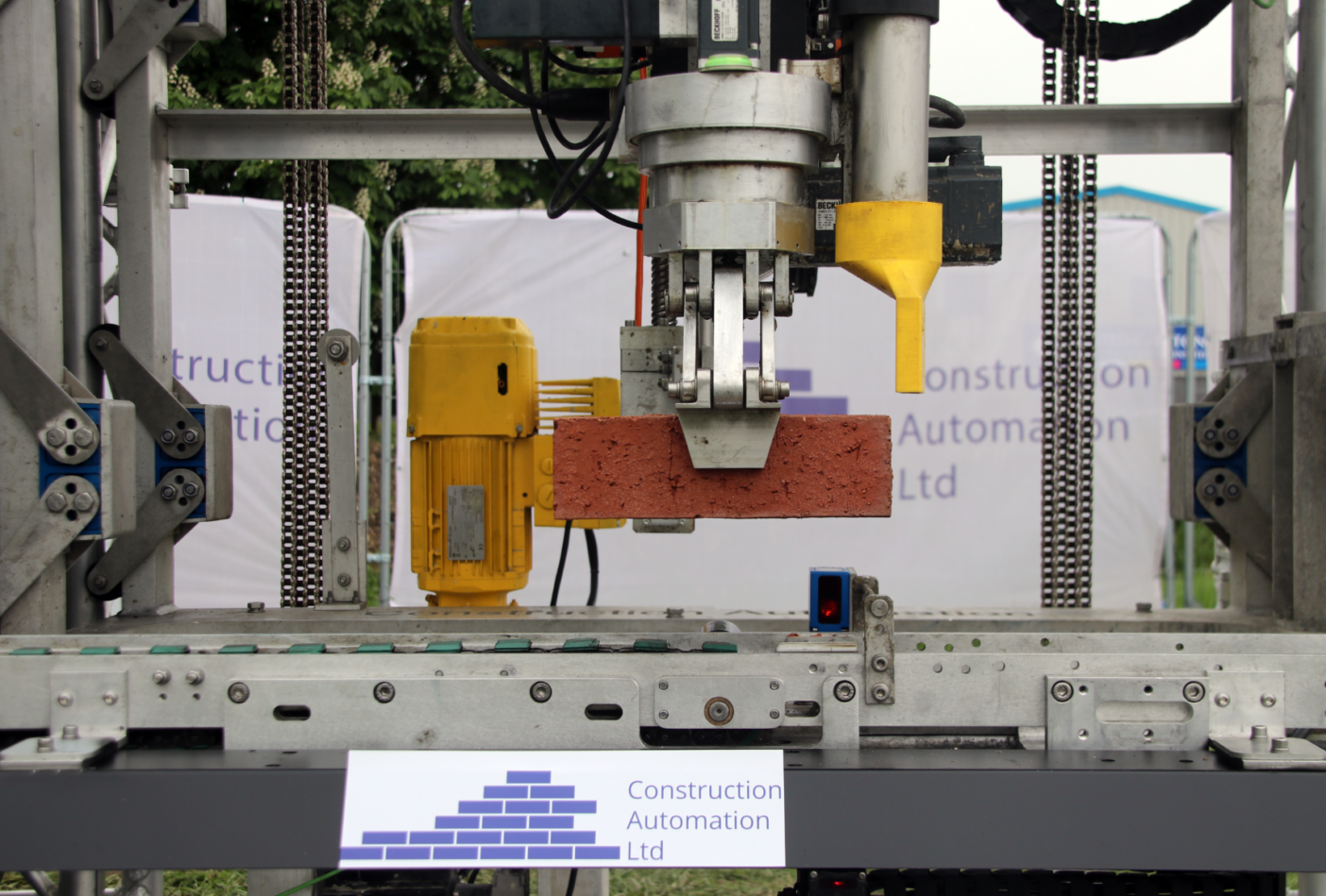
British start-up Construction Automation had an unexpected setback when they tasked their automated brick-laying robot (ABLR) with building a three-bedroom house in Everingham, Yorkshire, in September. Company director David Longbottom says there were problems with the track. “It was engineered to fine tolerances and started sinking, jamming and sticking. But we’ve learned lessons and built a new track and we’re ready to have another go,” he says.
Longbottom makes several strong arguments for the usefulness of the ABLR. Firstly, it improves safety. Most accidents involve falls from scaffolding and operatives work in scissor lifts fastened to the track. Second, the robot guarantees quality. It measures bricks and blocks with lasers and records every detail digitally. Meanwhile, it should be cheaper. “We eliminate scaffolding and there’s no wastage. We halve the build process from four weeks to two, saving fees on site managers.”
A further advantage is the ability to “build a house with a tablet rather than a trowel”. The robot requires two operatives. A skilled tradesman puts in complex elements like the insulation and lintels. A semi-skilled person places the bricks on a cassette. But there is no heavy lifting. “There’s a shortage of construction workers and the average brick layer is around 50. If you’re at school contemplating a career, seeing apprentice bricklayers on their hands and knees is unlikely to appeal. The robot helps deal with the death of skills and improves inclusivity,” he argues.
The government wants to build 300,000 homes a year, but there is a big shortfall. It’s pushing Modern Methods of Construction (MMC) as a way to address the problem. But Longbottom says the short lifespans of modular homes makes it hard to get mortgages. “We prefer to use robots to build brick and block houses that last at least 150 years,” he says.
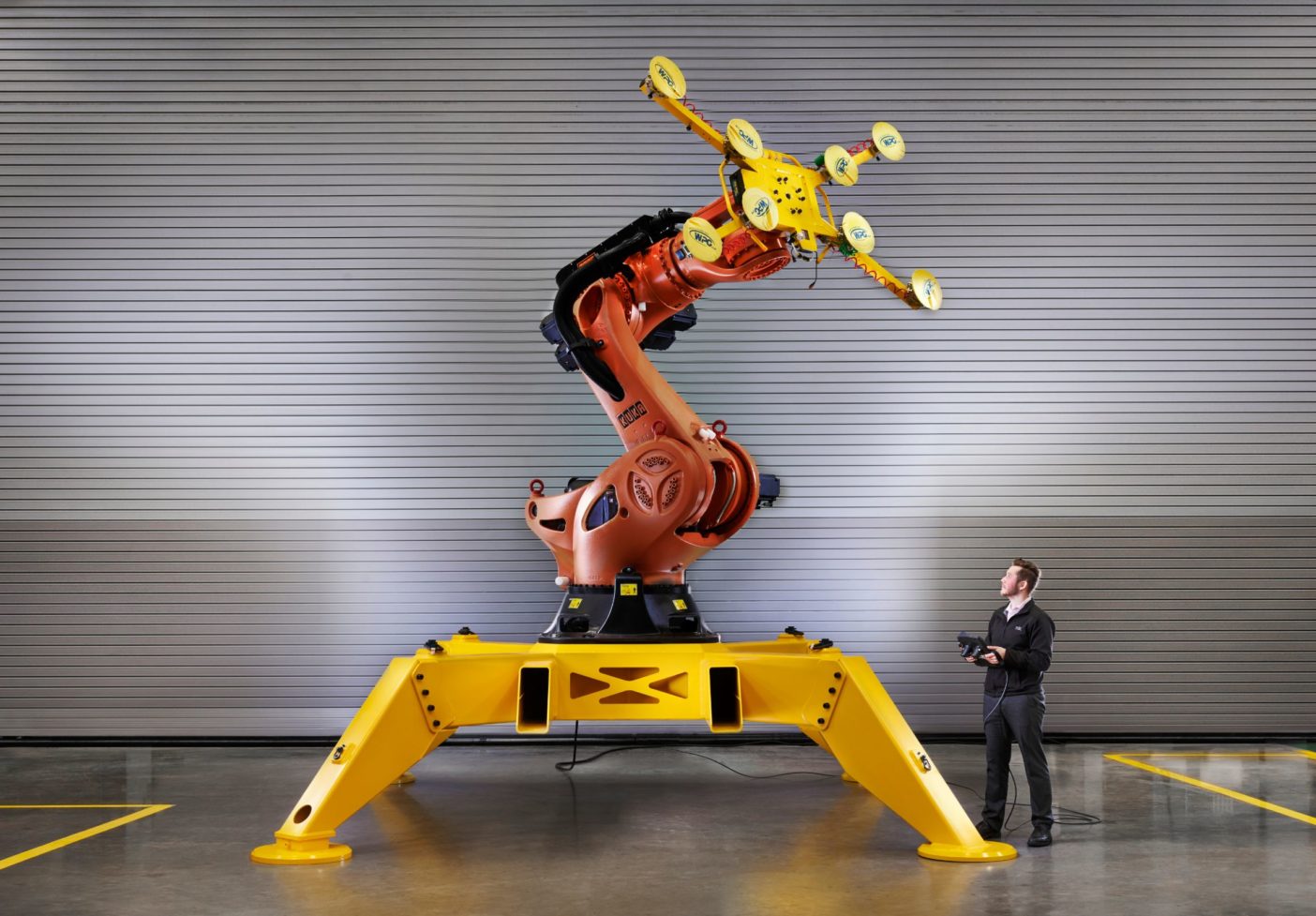
Rest of the world
Japan has emerged as a centre of construction robotics to address its chronic skills shortage. Contractor Shimizu has trialled three robots – a carrier of materials, a welder, and a multi-purpose “buddy” robot with two robotic arms. Meanwhile, Japan’s Advanced Industrial Science and Technology Institute (AIST) has designed the HRP-5P that can pick and drill in a drywall.
In the US, San Francisco-based Canvas has also created a robot for finishing drywall. It has already worked on projects, including the San Francisco International Airport and Chase Arena. Also operating in the US is Advanced Construction Robotics’ TyBot, which automates tying of steel reinforcement bars. Meanwhile, in Australia, Fastbrick Robotics has designed the Hadrian X robot that uses a 98-foot robotic arm mounted on a truck to place customised blocks 12 times the size of normal bricks. In June last year, Hadrian X laid more than 200 blocks an hour.
Ireland recognises the potential of these developments, but he believes the industry needs high-level thinking about how best to take advantage of robotics. “The problem with construction is every building and project is different and that drives the need for hugely flexible ways of working. Car companies invest hugely in a method of manufacture, then design based on that known process. It’d be great to see the large tier 1 construction companies investing in new methods of manufacture, then using proven industrial robotics in offsite factories, rather than trying to apply new technology to the existing construction processes. It seems less risky and more achievable,” he says.
Ireland offers a vision of house manufacture as a potential example. “Imagine if someone designed an amazing house which was mass manufactured, in a facility like a car factory. You could configure it digitally, choose the colour and features, know exactly how much it was going to cost and it would come with levels of performance which had been specified and tested as part of the development process. It would take a character like Elon Musk to say ‘you can have this amazing product but they’re all the same’, but you could get a standard product with features which you could never retrofit to an existing property or incorporate into standard construction, but they would all have to broadly be the same and made in the same way.” he says.
Changes of mentality among consumers would have to drive the changes, he says. “Rather than buying a house based on location, consumers would choose houses based on quality, performance and features. The industry will then respond and make the long-term capital investments to allow standardisation of design and manufacture. This would unlock the enormous potential of robotics in construction,” he concludes.
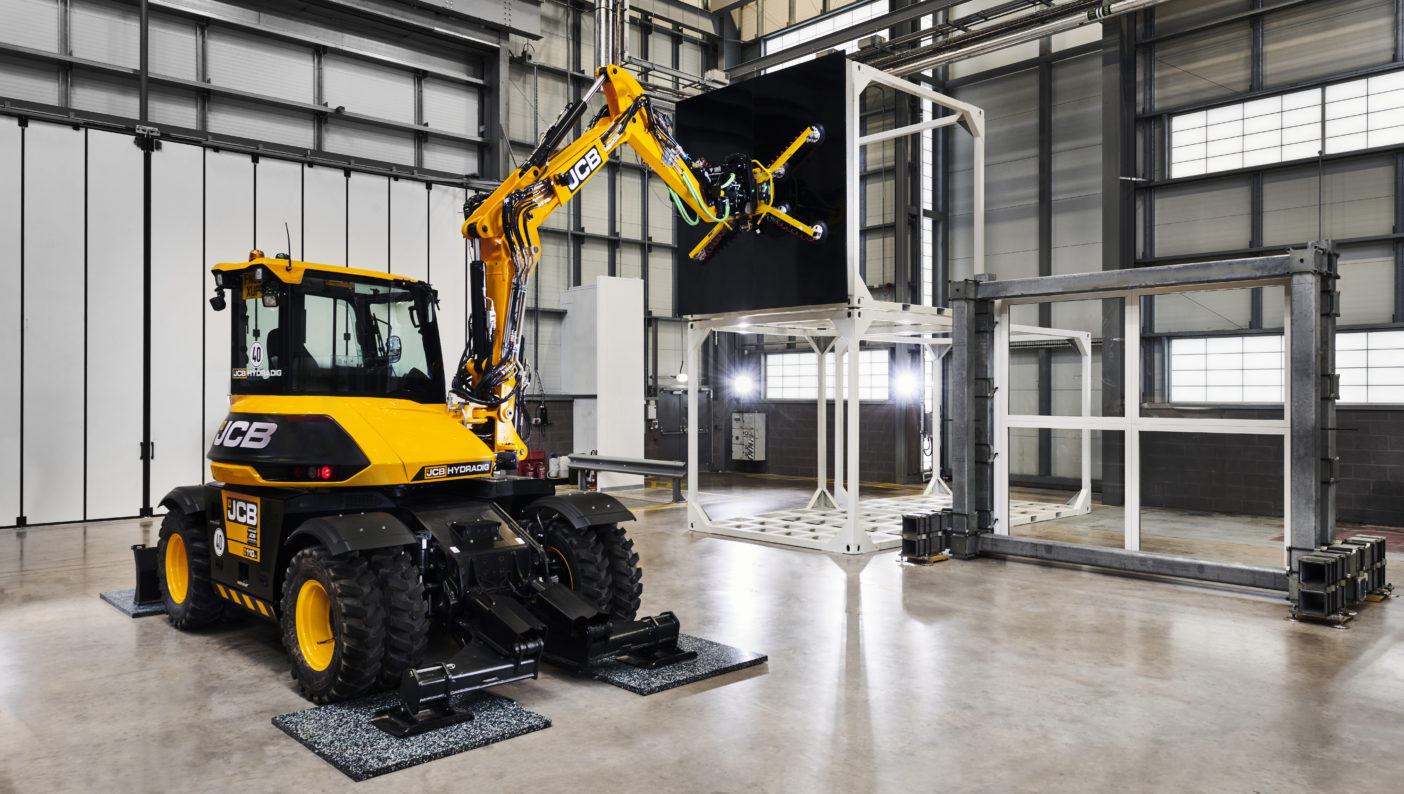
Automotive inspiration
Influenced by the use of robotics in automotive factories, UK contractor Laing O’Rourke is creating a highly automated construction factory. Laing O’Rourke has spent years thinking about how to adapt automotive strategies to the different demands of construction. The UK government is supportive and has provided a £22.1m grant.
“Laing O’Rourke is one of the few contractors investing a huge amount in automation and robotics,” says Mark Ireland, chief engineer for technology strategy at the Manufacturing Technology Centre. “Most of the industry is still operating on a model of sub-contracting. The sub-contractors then use machine hire companies. So, it’s hard to see where the investment would come in design and manufacturing with robotics.”
In developing their ideas, Laing O’Rourke visited several automotive plants, including Jaguar Land Rover. Laing O’Rourke will provide its own version of JLR’s Virtual Customer Experience which allows potential buyers to specify their vehicle and view a full-size projection on a screen. The company also visited the McLaren factory in Surrey, JCB’s high-tech factory in Staffordshire, and Ford’s Transit plant in Turkey.
To develop the technology, Laing O’Rourke is working with companies that have delivered automated manufacturing solutions for major car makers. The robotics will be designed by Comau, a subsidiary of Fiat Chrysler Automobiles; the computer-aided design and manufacturing tools will be supplied by Dassault Systèmes in France; the control systems by Siemens in Germany.