With the effects of Brexit and Covid-19 being increasingly felt, a new light is being cast on the role automation plays within the manufacturing environment and the technology behind it. Maria Highland investigates…
Automation has been ever present within retail with Amazon paving the way since 2012. However, retail warehouses are not the only sector that has seen a take-off in automation, manufacturers have been busy kitting out their warehouses with the latest tech. But it’s never one size fits all, and the needs of manufacturing operations are different to that of retail, therefore a different approach is needed.
“Where the retail sector has been quick to adopt automated technology, the manufacturing sector has lagged behind; quite possibly as manufacturing applications are ever more complex and diverse,” says Steve Penney, key account manager, goplasticpallets.com.
Joe Daft, head of robotics at OW Robotics, agrees. “Manufacturing and hi-tech warehouses are usually quite complex areas,” he says. “Manufacturing has a lot of emphasis on components being available at the right time in the right place. A lot of these components usually vary in size for some manufacturing elements.”
Flip over to retail, and operations entail picking cases or pallets for order distribution to retail stores. This makes them less complex as there is not much variety in the processes, which is usually limited to receiving, storing, picking and shipping. Arguably, the complexity comes from the sheer volume of products going through the warehouse.
But “in manufacturing, we may typically see a few hundred to a few thousand products being produced,” says Michiel Veenma, vice president, industry solutions and design, Körber Supply Chain – Automation. “However, these often require many parts or components.”
It doesn’t end there, “there are different aspects to manufacturing, and the inbound operation will have different handling needs to the outbound,” says Claire Umney, managing director, Breathe Technologies. “If we’re considering an assembly and manufacturing operation, for example, component parts enter the warehouse, and complete assembled units go out.”
But have no fear, although “different manufacturing operations may face varying challenges according to their function, whether mass manufacturing or customised, they can create assemblies from diverse manufactured components, each with different tack times,” says Alexey Tabolki, chief executive, Eiratech Robotics.
Online shift
“Many manufacturers saw normal outlets for their goods close during lockdown,” says Edward Hutchison, managing director, BITO. “Some were able to pivot to their existing online channel while others were forced to establish D2C operations for the first time.”
This shift to the online sphere has been a major game-changer for many OEMs and has greatly changed the way the warehouse operates. The on-going nature of Brexit and Covid-19 mean that these trends show no signs of yielding.
“The impact of e-commerce on B2B is a trajectory that will be felt in many sectors for a long time to come,” says Malcolm Wilson, CEO – Europe, XPO Logistics.
As a result, “logistics requirements in the industrial space are becoming more complex,” he continues. “Manufacturers are increasingly exploring D2C channels as they seek to enhance customer satisfaction and reduce costs.”
In line with this, Lewis Marston, chief executive at Rocket Consulting, points out that “we are now seeing a reshaping of supply networks and convergence of supply chain functions, with manufacturing facilities taking on greater logistics capabilities”.
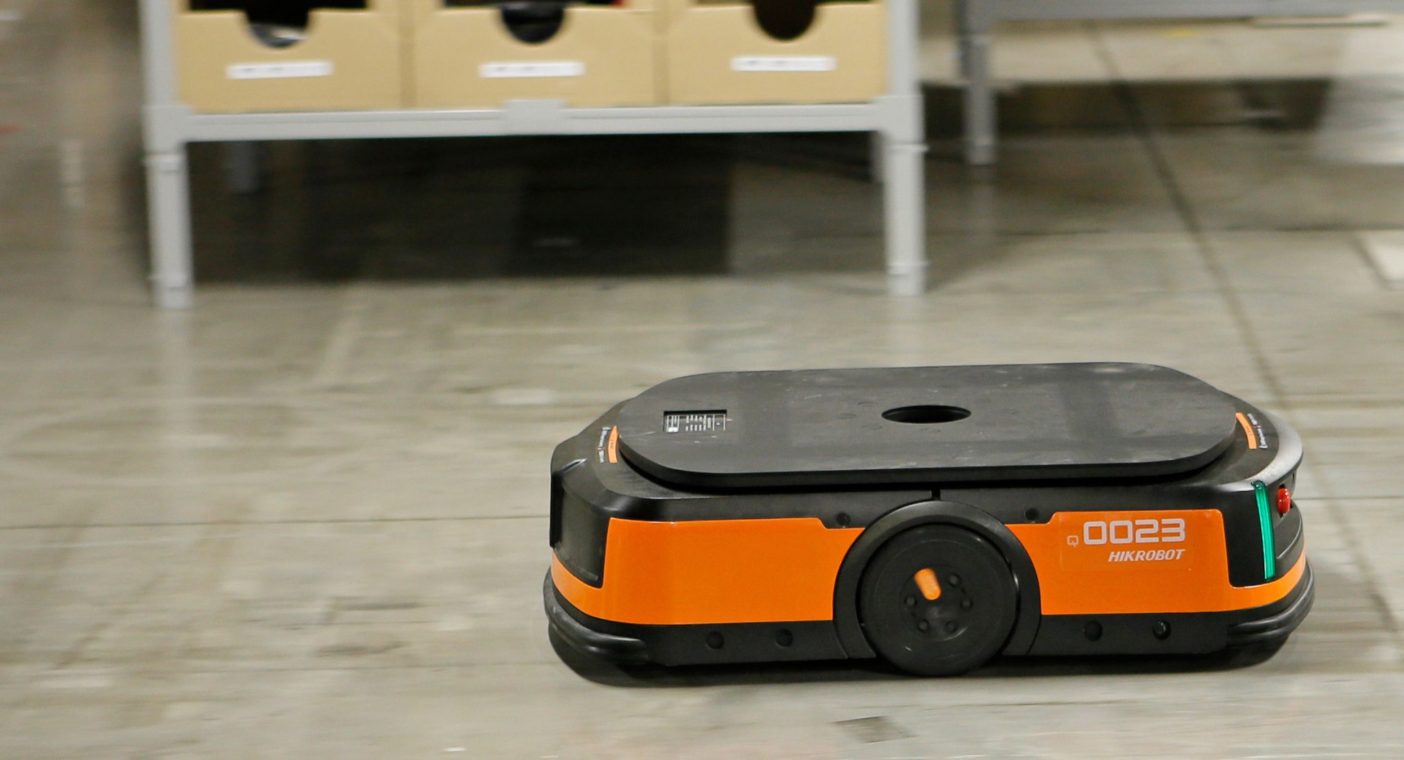
Spotlight on robotics
To accommodate the changing role of the warehouse and address external pressures of Covid-19 and Brexit, many manufacturing logistics operations are turning to automation. However, with the convergence of supply-chain functions, we are seeing also “crossover of processes and operational technology such as automation and robots from one area to the other,” says Marston.
Therefore, it increasingly difficult to have a conversation about automation without shining a spotlight on robotics. “Robotics are being deployed within the warehouse or multiple supply-chain points… [and] production lines and warehouse operations are being reconfigured “on the fly” to maximise growing capacity and throughput,” says Tabolkin.
Marston adds: “The last five years have been exciting in the space of supply-chain automation, seeing a proliferation in new entrants to the market with many more small-scale robot-based automation solutions available.”
More flexible solutions mean that “robot-based automation can be quickly adapted to process and layout changes resulting from shifting supply-chain needs, which, if you are an investor making a significant CAPEX investment, is nice to know that what you put in on day one can evolve as your business evolves,” adds Marston.
“What’s more, retrofitting enables robot solutions to be easily applied to and incorporated into existing facilities. Likewise, scalability signifies a lower entry point, meaning smaller companies starting with a small number of robots can scale almost tenfold as throughput is increased,” he concludes.
Bridging the gap
As manufacturing and warehouses converge with production and manufacturing hubs, and with large scale distribution operations, “autonomous robots are playing a very important role in bridging that production and distribution function,” says Marston.
Indeed, as the role of manufacturing and warehouses become more greatly intertwined, the use of robotics and automation has become more versatile and transferable. “Up to now, AGVs and AMRs have been used in goods-to-person deployments,” says Tabolkin, “but with their autonomy, they are increasingly used in kitting and reconfigured or customised production lines.”
When it comes to scalability and flexibility, a good entry-level robotic solution is autonomous mobile robots (AMRs). “The major use for AMRs in a manufacturing warehouse is the movement of pallets, either goods-in or goods-out, or they find application-moving non-conveyable items,” says Andrew Mason, sales manager, RARUK Automation.
Indeed, AMRs “offer the flexibility, speed and performance needed for efficient goods-to- person automation,” adds Tim Wright, managing director, Invar Systems.
Automation can also act as a leveller in situations that demand greater throughput and labour, and “can often be a more palatable solution than throwing people at a challenge,” adds Hutchison. “For many, however, the capital expenditure required, and lack of flexibility, is often a barrier to taking this step.”
To overcome this, companies require a flexible, affordable, simple, yet productive solution: “An internal driverless transport system or mobile robots that can transport parts between a warehouse and the production line is a good example of a solution that does not require complex infrastructure and software, but does offer flexible, future- proof and productive intralogistics for manufacturers,” says Hutchison.
Likewise, “while conveyor and fixed track systems are expensive to decommission and move, AMR solutions can be rapidly scaled up, configured, and reconfigured, allowing companies to implement systems quicker than ever before,” adds Umney.
AMRs also “have the flexibility to use several navigation methods depending on the complexity of the use case, for example, SLAM or QR codes,” adds Tabolkin. “What’s more, a vast range of safety sensors and lidars increase their safety capabilities, making them ideal ‘partners’ to navigate safely around humans and other dynamic objects and warehouse traffic. When required, robots can operate at high speeds within confined areas to rapidly speed up operations, such as goods to person systems,” says Tabolkin.
Intelligent data
AMRs are on the rise, tackling issues of labour shortages, health and safety, including social distancing. But what else is pushing manufacturing operations further?
“There are lots of new technologies available in the market. Mobile robots are definitely one of these and they have been very popular in recent years,” says Jarno Honkanen, director, solution management, Cimcorp. “However, there is no single technology that fulfils all requirements and that’s why there will continue to be a variety of technologies in the future.”
Therefore, it is not just about the technological developments, but “the whole process and taking a holistic view of things,” says Honkanen. “This means ensuring accuracy and reliability, without losing flexibility and adaptability.” In order “to achieve a demand-driven approach with flexibility and speed, you have to be smart – so, in the end, everything comes down to intelligence, or IoT,” he says.
Both sides of the coin
This is where data, intelligence and robotics join forces. Automation and robotics are only one side of the coin and a lot more rides on the intelligent software and data powering them than people think. “In the end, the pure mechanics, as well as the sensors, are not rocket science. The differentiator is often in the software that operates them. There are big differences in maturity, but also in the type of processes they support,” says Veenman.
In an era where SKU proliferation is set to continue, “manufacturers are constantly striving not only to achieve high levels of productivity but also agility, traceability and availability,” says Honkanen. “This is where automation – powered by intelligent software – secures huge benefits.”
“Data is at the core of supply-chain’s digital transformation: connectivity, collection, sortation and interpretation of data into actionable insights. Using this data to drive operations enables better and more effective strategic decision-making,” agrees Tabolkin.
Therefore, the key to 2021 rests with the digital transformation of the warehouse. “We can expect further innovation in the application of robotics technology as warehouses and workplaces reconfigure to create more networked and connected ways of working with intelligent devices and advanced software,” says Tabolkin.
“Warehouses and fulfilment centres will become more integrated, more intelligent and more connected. Digital transformation of the warehouse will continue apace in 2021,” says Wright. He predicts that “smart business will be developing smart warehouses where robots, pickers, packaging machines and sorters are seamlessly integrated to produce, not only optimum performance, but data that is shared in real-time with wider systems to deliver a competitive advantage.”
This article originally appeared in the March 2021 issue of Logistics Manager