AMRs have revolutionised intralogistics, and AGVs were a key starting point in the road to autonomous working. But is there still a place for AGVs in today’s warehouse? Maria Highland reports…
Automated guided vehicles (AGVs) used to be what we called any unmanned device moving around the warehouse. Originally these would have been mainly forklift trucks moving along embedded tracks in the floor, with relatively simple programming including sensors for safety. However, as technology has developed to allow more independent movement, the term ‘autonomous mobile robot’ (AMR) has become more apt. AGVs are still here although perhaps their role in the warehouse has changed.
You may ask, aren’t AGVs and AMRs pretty much the same thing by different names? “No,” says Rose Power, head of operations at Scurri. “Due to the rigidity of how AGVs work compared with the flexibility of AMRs, I don’t believe it’s just semantics.”
That rigidity is not necessarily a drawback. Without the autonomy of their rivals, AGVs work particularly well for repetitive processes or for businesses whose product profile is finite, such as raw materials. Typically, they supply manufacturing lines, accessing racking, and transport finished goods to staging or storage areas.
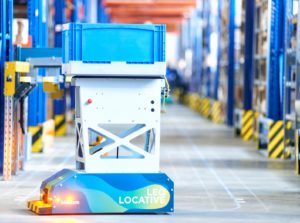
Bridging the gap
AGVs are often used to bridge a gap in a production line, to travel where there’s insufficient access for heavy-duty machinery such as embedded conveyors. Part of the appeal is that they are a standalone technology that can fit within an established operation on a modular basis, as an alternative to renovating the entire warehouse with full-scale automation.
“They provide adaptability to material flow,” says Edward Hutchison, managing director of BITO Storage Systems. “This kind of ‘partial automation’ can be a company’s first step on the automation path that, for many, will represent a more viable manual labour alternative than going directly for a complex, fully automated warehouse system.”
Labour shortages are a part of seasonal peaks, and as the problem gets worse than ever, the value of alternatives is rising. Many operators will find a place in the warehouse that an AGV could reap huge rewards, especially if they don’t have the scale to take on larger scale automation. As a starting point, anywhere that uses a forklift should consider whether it needs to be driven by a human or not.
Paul Freeman, head of logistics solutions at Toyota Material Handling, believes several factors are driving the market for AGVs. “Firstly, there is a shortage of skilled people to operate forklifts. Secondly, the operational cost of automation is usually lower than manually operated processes. And thirdly, in this era of e-commerce, there is a need for streamlined delivery, which forces logistics providers to plan and predict their logistics f lows more consistently to achieve next-day or even same-day delivery.”
Optimal material flow
Digmesa makes precision flow sensors for fluids, used in almost every coffee machine in the world. To keep up with demand, the firm has chosen to automated its Swiss factory with AMRs from KNAPP.The Open Shuttle AMRs from KNAPP transport empty containers to injection-moulding machines and take finished products to a flow rack system. This serves as a buffer area, with FIFO storage controlled by a KNAPP PLC application – without connection to a host system. Light curtains on the racks are used to keep track of how full the 60 channels across four levels are. The containers are equipped with RFID tags to ensure traceability of the goods.
“Our injection-moulding machines run continuously, with 24/7 operation of our assembly machines, so optimal material flow is important, as is having no standstills,” explains Stefan Schneider, CEO of Digmesa. “This was the critical factor for investing in an autonomous system that – without a driver – puts things in the right place.”
The Open Shuttle AMRs are intelligent robots, undertaking smart path planning and independent management of orders. As a result of swarm intelligence, tasks are evenly distributed and transport routes are optimised. Each Open Shuttle features integrated intelligence, which enables it to autonomously plan its route to the target, detect obstacles and avoid them intuitively. This free navigation is based on the calculations of on-board laser scanners and software.
Another critical factor for Digmesa was the AMR’s lifting facility. “In comparison with other systems, with the Open Shuttle we can pick up and deliver at various heights.” The integrated lifter on a KNAPP Open Shuttle enables it to pick up and deliver small load carriers at heights of 550-1,500mm. The lifter moves up or down automatically, while the Open Shuttle is on the move, to suit the next collection.
The autonomous nature of the AMRs means they require no physical infrastructure and so the entire Open Shuttle system was installed and implemented in four months.
Baby steps
AGVs are one of the cheapest steps into automation. But Power points out the costs beyond unit price. “Although AGVs typically cost less per robot than AMRs, you must also consider the costs you will incur to set up, deploy, reconfigure and operate them. AGVs usually require the installation of physical guides, under-floor wiring, or surface tape to allow the AGV to navigate and locate itself in its surroundings. And if you need to install sensors beneath the floor, that means lost hours to renovation, plus the cost of the actual work.”
This will put off some prospective investors who may prefer AMRs that figure out the layout of the workspace themselves. But if the business case is there, there are enough offerings on the market to sidestep many of these hurdles. BITO’s LEO Locative, for example, does not require a costly control system or laborious installation procedure. “Users need only lay out a visible track on the floor for the AGV to follow,” says Hutchison. “Additional special markings ensure the system always knows where it is and therefore guides it reliably to all targets. The visual tracks and markings are easy to change or even completely remove so that new tasks can be set up in no time.”
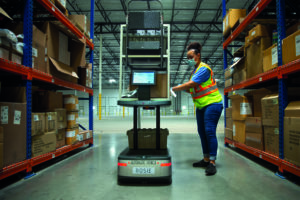
For operations where AGVs will work, the value they can deliver is not to be sniffed at. Power points out that AGVs can improve health, safety and workplace ergonomics while also helping with the recruiting and retention of workers. “The end result is lower cycle times, more picking and less walking, eliminating the wasteful and unproductive walking time and making the workflow easier and much faster. AGVs can dramatically improve worker productivity by two to three times, which leads to lower labour costs, higher pick rates and exceptionally faster cycle times,” she says.
Freeman agrees that safe working is a key for efficiency that AGVs can help to deliver. “Because AGVs follow the route around the warehouse that they have been programmed to follow – unlike most operator-controlled forklifts where there is temptation to take a potentially dangerous ‘quick cut’, which it seems is omnipresent among some drivers – the likelihood of an automated truck damaging either the warehouse building, the storage system within it or the load being carried is virtually zero. “This built-in safety functionality also means that the risk of the equipment causing injury to warehouse personnel working in the same area as an automated machine is minimal.”
Freeman also points out that AGVs use less energy and can be expected to have a longer working life than a manually operated forklift. AGVs can offer exceptional value, but it will be for specific tasks or for certain areas of any operation. On the other hand, AMRs present a more versatile option.
Measures of distinction
Although the distinction between AGVs and AMRs has blurred a little in the past few years, there remains a few general differences in the way they operate and how they are used. “AGVs enable fast material transport from A to B,” says Simon Jones, head of UK & Ireland at 6 River Systems. “Routes are mostly predetermined by wires, tape or barcodes stuck to the floor and the tasks AGVs are asked to do are clearly defined and repetitive such as pallet movement.”By contrast, AMRs use cameras and sensors to see what is around them and hold in their memory a digital map of the area they operate in. “AMRs constantly verify their location and use ‘intelligence’ to work out the best route to their next destination, or an alternative route if the first choice is blocked,” Jones explains. “AMRs are ideal for assisting employees with complex tasks such as ‘each’ picking in a warehouse.”
AMRs are orchestrated by sophisticated software that takes the raw orders to be picked from the WMS and provides all the intelligence to sequence the picking operation in the most efficient manner, taking into account delivery times, congestion, size of the products to be picked, number of staff available, as well as many other configurable factors. The AMRs then guide the staff through the process as directed by the software as well as carrying the picked products to where they are needed.
Go compare
Power sums up the benefits of both ’bots. “A great AMR requires no alterations to your current facility and can autonomously navigate through manufacturing and warehouse spaces. It learns its environment, remembers its location and dynamically plans its own path from one destination to another. If its path is blocked, an AMR can reroute itself with no assistance. The sensors an AMR uses to navigate ensure that it can operate safely in a dynamic environment alongside humans and material handling equipment.”
Flexibility is an important differentiator, according to Power. “Because an AMR is not a permanent structure in the facility, it can be moved and redeployed with minimal cost as your business grows and changes over time. In fact, an AMR can work in one part of the facility in the morning and be deployed for a completely different task later in the day.”
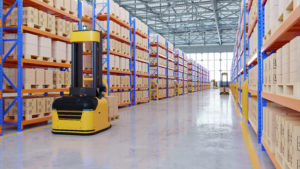
This versatility will be crucial for many businesses, especially SMEs going up against the big players. “AMRs offer tremendous flexibility and, importantly, scalability in conventional labour-intensive tasks such as order picking and put-away,” says Craig Whitehouse, managing director of Invar Integration. In fact, Whitehouse believes AMRs represent a potential advantage for smaller operators. “SMEs have a great opportunity to steal a march on larger retailers that may have committed to inflexible, fixed automated systems. By adopting intelligent software and advanced mobile robot technology, SMEs can leverage the flexibility, speed and performance of goods-to-person automation as a low-CapEx project.”
AMRs certainly offer a greater potential for smarter and dynamic automation. Power is categorical in her preference. “AMRs are superior to AGVs in terms of flexibility, cost-effectiveness, ROI, and productivity optimisation. At some point, all companies must ask themselves, can we afford not to use AMRs?”
It’s a good question but there will undoubtedly be many businesses for which the answer is ‘yes’ – at least in certain areas. Manufacturing and warehousing will always involve processes that AGVs can optimise just as well as AMRs, and with a smaller price tag. They may be less flashy than AMRs, but what AGVs do, they do well. Their role may be particular and distinct but there is still a decided and valuable place for AGVs in today’s warehouses.
Different paths
With increasing demand for fast deliveries, more economic, lower carbon footprint infrastructures, and the increasing adoption of Industry 4.0 in warehouses, facility owners are turning their attention to use of AGVs and AMRs.“There are many benefits that can be achieved by using these technologies,” says Nick Darrall, managing director of Iconsys. “Increased throughput/productivity, improved safety, data monitoring and the ability to make better informed decisions using the information gathered from these devices probably top the list of the most common advantages.”
Many companies are taking their first steps with this innovation and so Darrall believes it’s important to make sure that both design and layout allows for further expansion, creating agile solutions for future requirements.
“AGVs and AMRs essentially do the same task, however the latter can move around obstacles and make autonomous decisions,” he says. “This gives greater flexibility within the working environment and paves the way for better collaboration with the existing workforce.
There are other differences, states Darrall. “AGVs follow a pre-set path, which means there is additional mechanical work required to add new routes to the system, whereas any map changes for AMRs can be made offline, simply uploaded and you are ready to go.
“Both systems have their part to play in creating the solution and it is important for the integrator to look at the complete picture before making the decision on which system is the most viable and cost effective for the end user.”
This article originally appeared in the January 2022 issue of Robotics & Innovation Magazine