Due to labour shortages and increased need to feed the global population agriculture robots are becoming common place for farmers.
Agriculture is quickly becoming an exciting high-tech industry, drawing new professionals, new companies and new investors. The technology is developing rapidly, not only advancing the production capabilities of farmers but also advancing robotics and automation technology as we know it.
At the heart of this phenomenon is the need for significantly increased production yields. The UN estimates the world population will rise from 7.8 billion today to 9.7 billion in 2050. Thus, the world will need a lot more food, and farmers will face serious pressure to keep up with demand.
Fortunately, agricultural robots are increasing production yields for farmers in various ways. From autonomous tractors to robotic arms, the technology is being deployed in creative and innovative applications, including harvesting and picking; weed control; autonomous mowing, pruning, seeding, spraying and thinning; phenotyping; and sorting and packaging.
British agritech start-up, Small Robot Company (SRC), is one such company developing a range of sustainable farming products to maximise food production while reducing its cost on the environment. Its so-called ‘farmbots’ Tom, Dick and Harry are designed to plant, monitor and treat arable crops autonomously, with minimal waste, while reducing chemicals by up to 95%, preventing soil erosion and run off, and reducing cultivation emissions by up to 90%.
“Agriculture is on the cusp of radical change,” says Sam Watson-Jones, co-founder, SRC. “Precision, and not speed, will define the future of farming.”
His company has raised nearly £5m in funding to date, including £1.2m from Crowdcube raises, and £1.22m in government Innovate UK grants (the latter includes an £800,000 grant for its Wilma AI weed recognition technology).
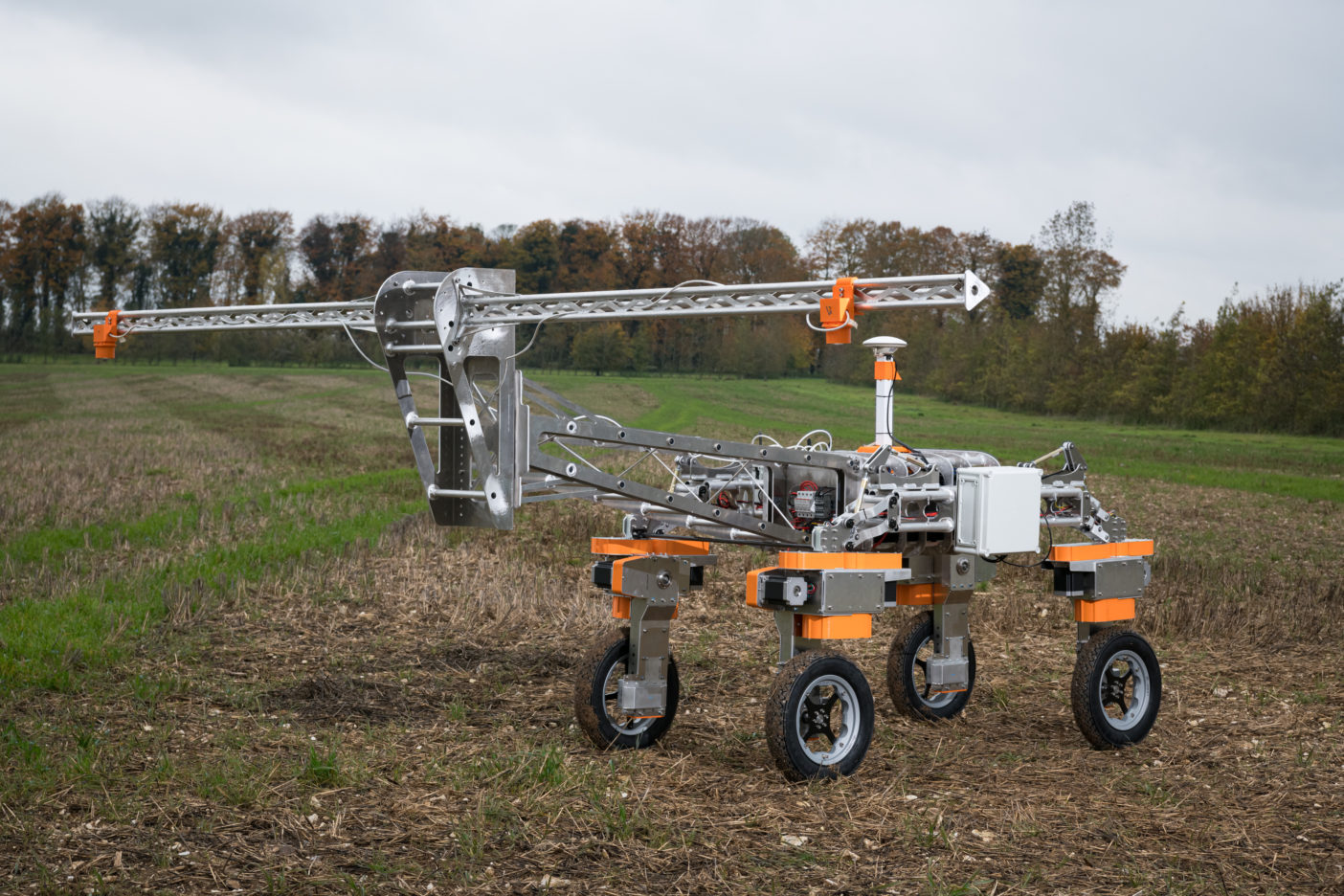
SRC is currently conducting field trials on 20 farms across the UK. Trial farms include the Waitrose Leckford Estate farm and the National Trust Wimpole Estate, which are both currently testing SRC’s first commercial weed mapping service, which uses SRC’s Tom monitoring robot to first locate the weeds.
According to Watson-Jones, this is the world’s first service for individual plant mapping at broadacre scale and Tom can cover 20ha per day autonomously, collecting about 6TB of data. He claims it can also distinguish plant details at submillimetre resolution, with less than one millimetre per pixel resolution on the ground. Weather-proof and able to be used all year round, Tom also incorporates increased speed, 5K camera capacity and extended battery life.
Callum Weir, farm manager of the 1,500–acre (600–ha) organic farm on the Wimpole Estate, says: “The key advantage of this technology is that it will enable us to be much more precise and targeted in controlling weeds, therefore helping us to increase crop yields and biodiversity. It’s also lightweight, helping reduce compaction of soils – a consequence of using traditional tractors – which will help improve soil health.”
Since its last raise, SRC has moved from proof of concept to commercially ready prototype and is now ready to manufacture its first robot fleet. An initial 10 Tom crop monitoring and mapping robots will be manufactured by Tharsus – which also manufactures Ocado’s warehouse robots – at its Blyth production facility in Northumberland, and ready for commercial service in October 2020.
John Toal, director of business development at Tharsus, believes that there is a general misconception when it comes to agriculture and the adoption of technology: “In fact, the farming community is very technology savvy. It takes very little to get them fired up about robotics in the field and this technology’s ability to address the macro-economic pressures that the farming industry needs to overcome.
“However, the farming community has been oversold and under delivered robotic tech for a number of years. By focusing on the core technical risks associated with getting a product in the field and operational, to a level of confidence required by the early majority, companies are actively changing the mindsets and perceptions of robotics currently held at a farm level.”
According to Watson-Jones, SRC aims to deliver Farming-as-a-Service in three stages. First, it is planning to service around 2,000ha (4,900 acres) with the 10 new Tom robots by January 2021, before making the model widely available from autumn 2020. The next stage is to deliver non-chemical robotic weed detection and control for 8,000ha (19,768 acres) wheat crops in 2021. This will be scaled up to service 20,000ha (49,421 acres) in the UK by 2023, comprising 70 UK farms that have signed a Memorandum of Understanding for the service, before then expanding to cover 80,000ha (197,684 acres) across the UK, USA and Canada.
“We’re on the cusp of a fourth agricultural revolution, taking farming into the digital age: and with British ideas and British technology at the helm,” says Ben Scott-Robinson, co-founder, SRC. “Robots will completely transform what’s possible on the farm. It will radically reduce chemical usage in arable farming, while improving soils, profits and yields. It’s the ultimate sustainable farming model.”

Feed the world
Another start-up with an ambition to transform the agriculture sector is Naïo Technologies. Founded in 2011 by French robotics engineers Aymeric Barthes and Gaëtan Séverac, Toulouse-based Naïo’s three weeding robot models – Oz, Dino and Ted – are designed to assist farmers in their daily work, reduce strenuous physical workload and limit the use of chemical weedkillers.
Unlike other agri–tech companies, Naïo has developed a standard navigation system for its agricultural robots, which, it claims, can be implemented on any off-road robot, and thus enables its use with many crop types. Using a combination of computer vision and GPS, Oz is designed for weeding and hoeing chores, Ted for vineyards, and the autonomous and electric Dino for large-scale vegetable farms.
To date, nearly 150 Naïo robots have been deployed at farms and vineyards both in Europe and in the USA, and Séverac believes that, “in the next 10 years, there will be robots in every field in Europe and North America”.
He says: “We recognise that the challenge is very ambitious, but we are convinced that we can meet it alongside our partners and stakeholders. Our goal is to ensure the ecological and social transition to sustainable agriculture.”
Naïo’s partners and stakeholders include France’s national investment bank Bpifrance, Pymwymic, a European community of impact investors, as well as historical shareholders Demeter and Capagro, venture capital firms that support innovative companies operating across the biomass value chain.
In Janaury 2020, these companies helped Naïo Technologies raise €14m (£11.8m) in a Series A funding round. According to Aymeric Barthès, CEO of Naïo Technologies, this investment will enable the company to reach the next level of technology maturity in order to prepare the robots for mass production.
“During the past few years, we have made a lot of progress in navigation, user experience and security aspects,” says Barthès. “Our next step is to focus on further increasing the reliability of our robots as well as developing an efficient and large-scale deployment strategy.”
Holy grail
While robots appear to be well suited to the vigour of weeding and crop planting, harvesting soft fruit mechanically represents an altogether different challenge. Each berry needs to be located, even if it’s behind a leaf, assessed for ripeness and then harvested and boxed with great care to avoid bruising.
What’s more these robots also need to be able to operate effectively in harsh conditions, including the presence of dust, varying light intensity, temperature swings and movement created by the wind.
As such, this process is very different from picking and placing a metal part on an assembly line. The agricultural robotic arm must be flexible in a dynamic environment and accurate enough not to damage the fruit as they’re being picked. Fortunately, recent developments in visual sensor technology, machine learning and autonomous propulsion have brought the goal of harvesting soft fruit mechanically within reach.
For example, the world’s first prototype raspberry–picking robot – developed by Fieldwork Robotics, a spinout from the University of Plymouth – successfully completed two field trials at a farm near Chichester in West Sussex last year in collaboration with Hall Hunter Partnership, which supplies soft fruit to Tesco, Marks & Spencer and Waitrose.
During the test, the picking process reportedly took approximately one minute for a single berry. Given the £700,000 cost taken to develop the solution, this result could be perceived as underwhelming. However, as the farming industry battles rising labour costs and Brexit-related shortages of seasonal workers, this could be the future of fruit-picking.
According to Fieldwork Robotics, each robot will be able to pick more than 25,000 raspberries a day, outpacing human workers who reportedly manage about 15,000 in an eight-hour shift.
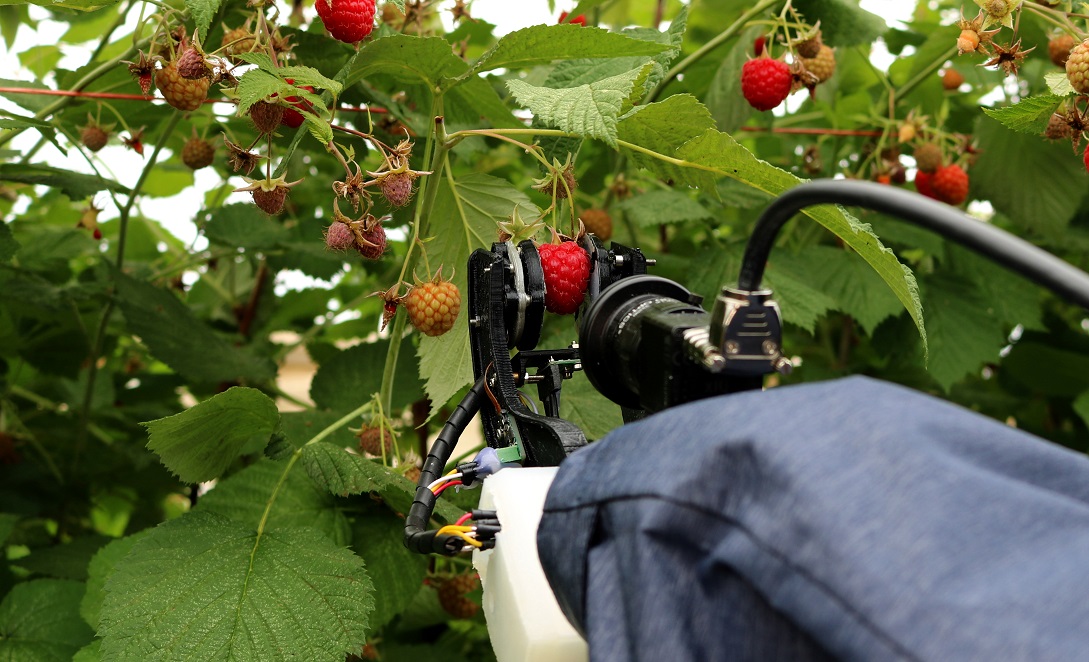
Guided by sensors and 3D cameras, the 1.8m-tall wheeled machine’s gripper zooms in on ripe fruit using machine learning. When operating at full tilt, Fieldwork claims the robot’s gripper can pick a raspberry in 10 seconds or less before dropping it in a tray where the fruit gets sorted by maturity, and moved into punnets, ready to be transported to supermarkets.
But why raspberries? “Because they are more delicate, more easily damaged than other soft fruits, and grow on bushes with complex foliage and berry distribution,” says Dr Martin Stoelen, a lecturer in robotics at the University of Plymouth, whose work is being developed and and commercialised by Fieldwork Robotics.
Also, Rui Andres, portfolio manager at Frontier IP, one of the main backers of Fieldwork, says UK farmers typically pay £1 to £2 per kilogramme of raspberries picked by human workers and Fieldwork intends to lease its robots to farmers for less. He believes this could make the robot a potentially attractive proposition for growers under pressure from the rising minimum wage, with labour accounting for half of their costs.
According to the National Farmers’ Union (NFU), UK farms growing apples, berries and field crops require 70,000 seasonal workers a year. The berry industry alone employs 29,000, but trade body British Summer Fruits (BSF) estimates it will need an extra 2,000 pickers in summer 2020, as people eat more berries. In 2019, NFU recorded more than 6,000 unfilled vacancies on UK farms.
Nicholas Marston, BSF chairman, concurs: “Fruit growers were 15-30% short of seasonal pickers in 2019. It’s a struggle. There were definitely crop losses last year and the year before.” And even if the robot revolution becomes reality, Marston cautions: “It will be 10 years before robots will work as effectively as people.”
This article originally appeared in the April 2020 issue of Robotics & Innovation magazine