Katie Searles speaks to those at the forefront of deploying robotics in the UK’s nuclear sector, and discovers if the technology can remove humans from hazardous environments…
According to National Centre for Nuclear Robotics, the UK holds some 4.9 million tonnes of nuclear waste, and, with today’s technology, it could take up to 120 years and cost as much as £200bn to make it safe. Thus, new ways are needed to tackle the country’s legacy waste – solutions that are faster, safer and cheaper than what is available now. By uniting robotics, AI, sensors, radiation, and resilient embedded systems, there is an opportunity to bring one of Europe’s biggest and most complex environmental challenges to a timely end.
But what exactly is required for safe nuclear decommissioning? And what are the challenges involved with designing robots to be robust, reliable, safe and able to withstand highly radioactive environments? Much work is being done by government, private and public agencies to answer these questions, not least the Nuclear Decommissioning Authority (NDA), which has been charged with cleaning up the UK’s oldest nuclear sites and ensuring these 17 facilities are safe and ready for future use.
Amid attempting this momentous undertaking, the NDA also wants to reduce the number of decommissioning activities that place humans in hazardous environments by 50% by 2030. To help realise this, the nuclear sector needs to “embrace new, emerging technologies, to help make a difference and improve how we go about doing things safer, faster, cheaper, more environmentally friendly and at pace,” says Rav Chunilal, head of robotics and AI at Sellafield Ltd, which is responsible for the safe and secure operation and clean-up of the Sellafield nuclear site, located on the Cumbria coast and owned by the NDA.
According to Chunilal, a range of robotic solutions have been developed, trialled and tested by the nuclear sector, which is also harnessing lessons learned by other industries including oil and gas, as well as construction. From quadrupeds to unmanned aerial vehicles (UAVs) and underwater robots, the nuclear sector is working to create solutions that can perform inspection, maintenance and mapping tasks in spaces inaccessible and sometimes dangerous for humans.
Total nonstop action
Crucially, robots also do not require toilet breaks, food or sleep. “Robots are good at repeating things again and again, whereas humans are not so good at repeating tasks because we get tired, we get sloppy and we lose concentration,” says Professor Tom Scott from the University of Bristol and co-director of the Engineering and Physical Sciences Research Council’s Robotics and AI in Nuclear (RAIN) research consortium.
To illustrate his point, Scott provides an example of making fuel elements for nuclear reactors, which involves repeatedly picking up fuel pellets and placing them in a tube one after the other. “For a human to do that, they’ll have to handle material in the glove box, they’ll have to wear PPE, they’ll have to have two layers of under gloves, and the actual rubber gloves.
“The pressure in the glove box is held at a negative pressure, which means the gloves suck in,” continues Scott. “A human operative has to use their bottom two fingers to hold the gloves on their hands, which means they’ve only got three digits to work with on each hand. Furthermore, because the gloves are lead lined, their fingers might cramp up after about five minutes, unless they are an experienced operative.”
Cramp isn’t the only issue to contend with, however. During Rav Chunilal’s presentation on robotics for hazardous environments at Robotics and Automation Conference 2021 in November, he recounted an incident involving an operator at Sellafield who accidentally punctured one of his gloves, resulting in radioactive material coming into direct contact with their finger.
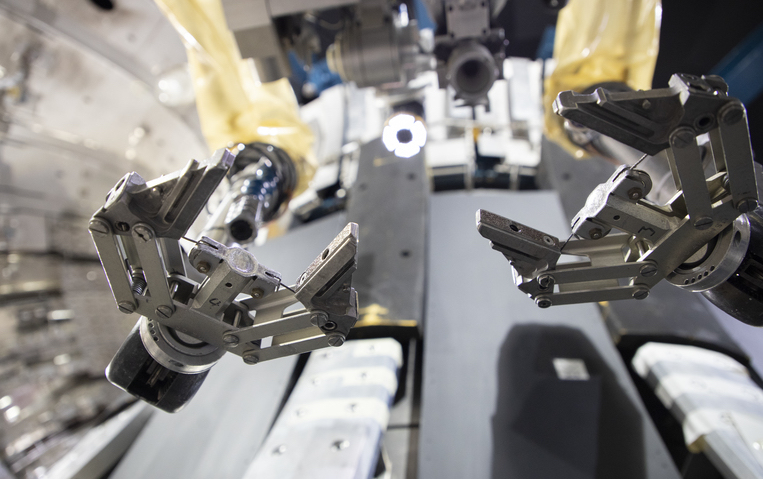
Fortunately, these kinds of safety issues are of no concern for robotic systems. Additionally, robots don’t block radiation-reaching sensor equipment, unlike a human operator, which can block as much as 40%. Indeed, the lightweight carbon-fibre or aluminium technology of a robot is transparent to radiation, which thereby provides a truer measure.
But while robotic solutions are better equipped to working in environments containing radiation, the technology is not totally impervious. “Different technical things can go wrong,” Scott explains. “Sometimes it might be optical encoders on robot joints becoming cloudy because the radioactivity turns the glass black or brown and light stops going through it. The optical encoder stops working, giving it a system error, which is terminal for the robot – it won’t work because it doesn’t know where its joints are.”
Scott details how, similarly to humans, the level of radiation affecting the robot can be monitored using dosimetry – the measurement, calculation and assessment of the ionising radiation dose absorbed by an object. Thus, researchers can keep a running total of how much radiation the robot has received and take informed decisions on when to remove it.
New approaches
Surprisingly, the tech-heavy nuclear sector still relies on some old-fashioned fail-safes to recover robots in case of system failure, such as tethering. However, several organisations are attempting to drag the sector’s less innovative approaches firmly into the modern day.
For example, the Connect-R project is a UK Research & Innovation-backed collective of academics developing an industrial-scale, self-building robotic structure for use in unsafe working conditions. And in its efforts to transform the way hazardous duties are carried out, the team has successfully managed to replace the electronic control system that is susceptible to radiation damage. Additionally, the UK Atomic Energy Authority (UKAEA) Remote Applications in Challenging Environment (RACE) has created specially designed hazmat suits for robots.
“We had experience in developing coats, little plastic bags, radiation protection hazmat suits for robots,” says Guy Burroughes, senior control system software engineer at UKAEA. [The robots] have a large range of motion so making a coat or cover is extremely challenging. But it’s something that we have expertise in and were able to deliver.
“It meant that we have been able to lead the world for deployment of quadrupeds within a nuclear decommissioning space,” he continues, before emphasising the importance of “choosing the environment wisely, training the robot to walk the safest route and avoiding the spicy bit in the centre”.
“At the end of the day, it means that a human doesn’t have to take that dose [of radiation], which is great. If a robot goes into a room that then completely collapses, that’s fine if you get the data out of it because that has saved a human from having to go do that task. That’s a win for everyone.”
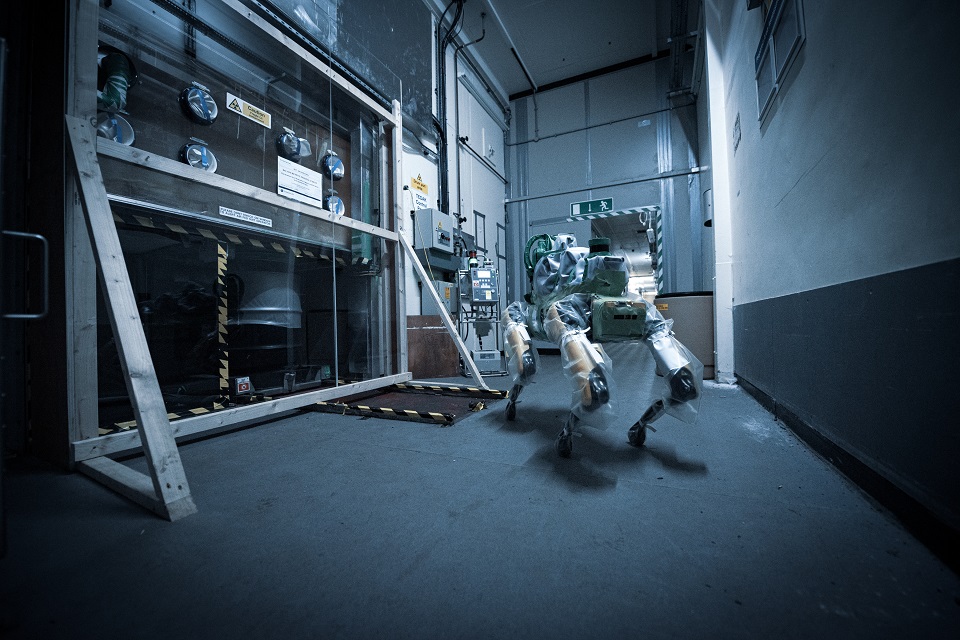
The data that these robotic solutions collate can be critical for the teams maintaining nuclear facilities, as well as over the lifetime of the decommissioning cycle. Burroughes notes that, in the hands of an expert, this data has the potential to enable those working in nuclear to do their jobs “faster, safer and cheaper”. And through use of this data and additional technologies such as digital twins and AI, the nuclear sector is adopting a preventative maintenance strategy where monitoring systems harnessing machine learning could have the potential to alert humans to any anomalies.
Furthermore, thanks to the development of robotics that can both fly and swim, the nuclear industry can oversee the tallest chimney and deepest waters. In 2014, a team from the University of Bristol became the first to develop and use a UAV on a UK nuclear facility. Before even stepping foot on the Sellafield site, the researchers had already created the most comprehensive multi-rotor UAV in the world at the time. Since then, Sellafield has used, and continues to use, air-based robotics to collect visual data from hard-to-reach environments across its site. According to Chunilal, his team is looking to conduct semi-autonomous inspection and surveys using UAVs in “a routine manner on the site” and has even conducted surveys remotely from as far as 100 miles away.
While the development and trialling of robotic technology is inspiring, the teams working with these robots on a daily basis understand that it is just the start of a long journey. As Burroughes explains, everyone now accepts robotics in the automotive industry and in industrial automation. For nuclear however, it is the development of four-legged mapping robotics that is the first big step in getting the industry to think seriously about using robots for a range of tasks. “It’s going to revolutionise the way that we think about decommissioning and hopefully change the equations when it comes to cost per watt, on fusion energy and nuclear energy,” he adds.
Chunilal agrees and says that he wants to see a step-change at Sellafield, making both robotics and AI the new business-as-usual at the Cumbrian facility. As a result, his team is working to make these solutions available as a tool kit for the industry.
“We’re looking at how to standardise the approaches we’re putting into robotics and how we put systems in place, so that we can take one bit of kit, deploy it and have it working on one site before replicating it at other sites. And again, that all comes back to helping us deploy at pace,” he concludes.
Price of power
While some nuclear sites in the UK are being made safe for ancillary uses, nuclear power, while controversial, still has the potential to be a clean energy source. However, cost remains a major barrier. As Professor Tom Scott from the University of Bristol explains, nuclear energy in the UK and the western world currently costs four times what it does in the East.He says: “In many ways, the processes we’re using are still the ones we were using in the 1950s and ‘60s, when China and Asia didn’t have nuclear reactors. They’ve got a different generation approach to how they do nuclear. In Southeast Asia – nuclear is the cheapest form of electricity. This is not the case in England. “But if we did a better job of the automation, the integration of robots and sensory systems into nuclear power plants, then yes, we could make nuclear power cheaper, but without sacrificing safety. In fact, we’d make nuclear power plants safer.”
Hinkley Point C in Somerset is the first nuclear power station to be built in the UK for over 20 years and will feature two new nuclear reactors with the potential to provide zero-carbon electricity for around six million homes. According to Scott, this new power station was not designed for robots, and so to see future builds planned with robotics in mind he stresses that there needs to be more widespread uptake of robotic systems.
“It is going to take a little while to do that. But I think the industry has woken up to the fact that it needs to do it and needs to come up with modern technologies, because that’s the only way it is going to contribute as much as it should to combating climate change.”
Dr Adam Stokes, a member of the Connect-R project and deputy director at the Edinburgh Centre of Robotics, also believes there is an opportunity to “co-create” solutions in the next generation of nuclear. “If we design public assets to contain the affordances required for robotics then we vastly simplify the tasks that robots have to perform, and we ensure through-life safety and reliability without the requirement for humans to put themselves in harm’s way.”
This article originally appeared in the January 2022 issue of Robotics & Innovation Magazine